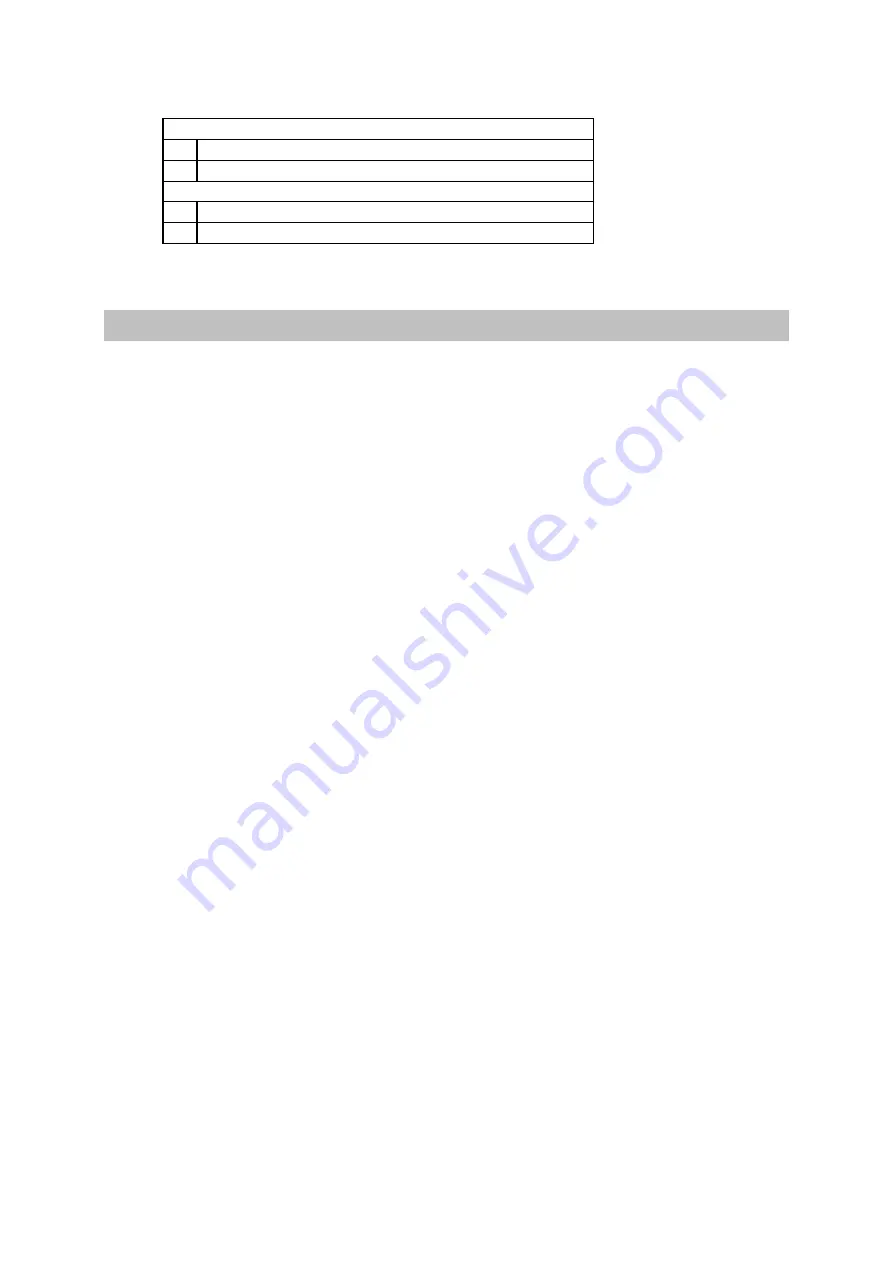
Parker Hannifin S.p.A. - Divisione S.B.C. “SPD” User’s Manual
63
9.3 Speed control adjustment
9.3.1 Some important concepts
SPEED LOOP
: The main task of a converter is to control motor speed so that it follows as
faithfully as possible the speed request that is generally known as the REFERENCE.
Faithfully following the reference means that the motor speed should equal the reference in
static conditions and also that the motor speed is as equal as possible to the speed requested
during dynamic conditions. To carry out this task, the converter must know some of the
features of the motor used and the mechanical part attached to it. This information is
communicated to the converter by using the so-called ADJUSTMENT PARAMETERS.
ERROR
: The error is the difference between the reference speed and the motor speed. The
size of the error is used by the speed loop in order to evaluate how much current must be
supplied to the motor, based on the adjustment parameters.
TORQUE
: The current that circulates in the windings of the motor is transformed in torque,
thereby allowing the motor to accelerate or decelerate.
GAIN
: Given the typical applications of the converter, when we speak of gain in this
document we refer to the rigidity of the axis, better known as the STIFFNESS. To better
illustrate what stiffness means, we can imagine a motor controlled by a converter with a
requested speed of 0. The motor shaft will appear immobile, but if we apply a torque to the
shaft, it will demonstrate an angle that is proportional to the torque applied. Suppose we
apply the rated torque of the motor and measure the stiffness in degrees. The degrees
measured will be the index of the quality of the regulator as parameterized. Clearly, it is not
only the index of quality.
9.3.2 What is needed
To adjust a converter correctly, an oscilloscope with memory must be used. A technician who
can use it to carry out the operation will also be needed. If it is not possible to use an
oscilloscope, a more approximate but applicable adjustment method will be illustrated at the
end of this section.
inputs
6
Converter on ( 24V - on ) IN
7
Stop / Start ( 24V – Stop ) IN
outputs
11 Drive OK ( 24V - ok ) OUT
12 Motor Overloaded (i
2
t) OUT