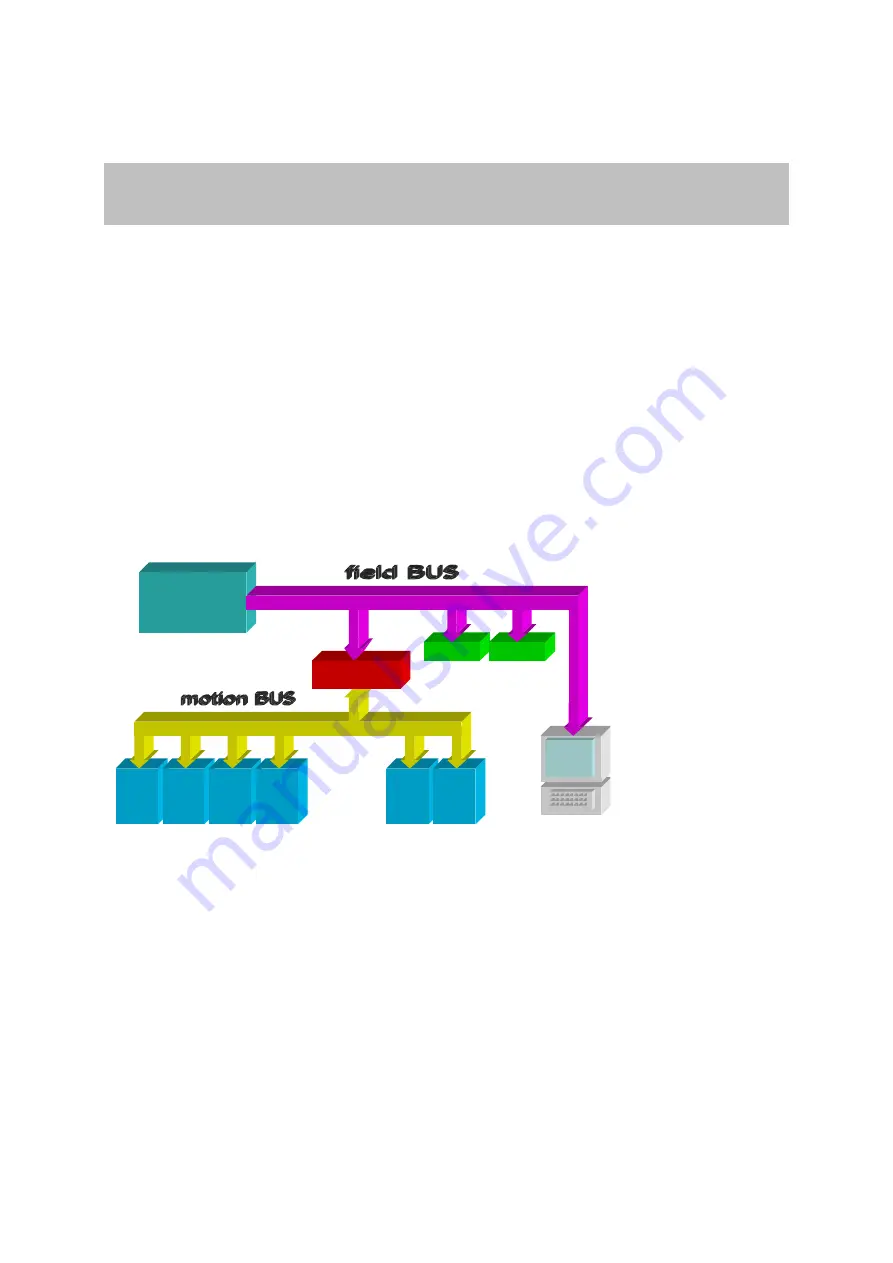
Parker Hannifin S.p.A. - Divisione S.B.C. “SPD” User’s Manual
7
1.4 Expansibility: the Parker-S.B.C. bridge and its
philosophy
Manufacturing companies of machines that use “servo” motor drives frequently have the need
of combining the PLC with the axis control.
The two programmable components are often heterogeneous; the first one sees to the machine
logics management, whereas the second one sees top the motor motion profile management.
The skills required to manage the two products are so different that they require different
persons, with a consequent increase of costs and new problems to manage, that is, the
interface between two non-homogeneous worlds.
Besides having all of the features required by the market of a servo converter, the Parker-
S.B.C. drives for brushless motors are also capable of executing “motion” functions that can
be used for a large number of applications, without having the typical need of programming
an axis control. Their feature is that they can operate as “MOTION ENGINE”, that is, with a
component that commands the motor to execute the desired motion profile, while the
MACHINE LOGICS is still managed by the PLC or by the machine PC.
Drive
S.B.C.
Drive
S.B.C.
Drive
S.B.C.
Drive
S.B.C.
Drive
S.B.C.
Drive
S.B.C.
PLC / PC
I / O
Bridge
I / O
The group of converters used for an application become a single peripheral unit of the
PLC/PC using standard FIELD BUS (Profibus or DeviceNet), and the architecture of the plant
control system becomes of the type shown in the figure.
With the Bridge philosophy, the user or the manufacturer can write motion programs using a
standard PLC, thus avoiding to realise specific application communication protocols.
This philosophy aims at allowing the manufacturer to reach his goals, in terms of time-to-
market, allowing him to focus the efforts on the design activity and avoiding multiple
problems connected to the drive use and interfacing.