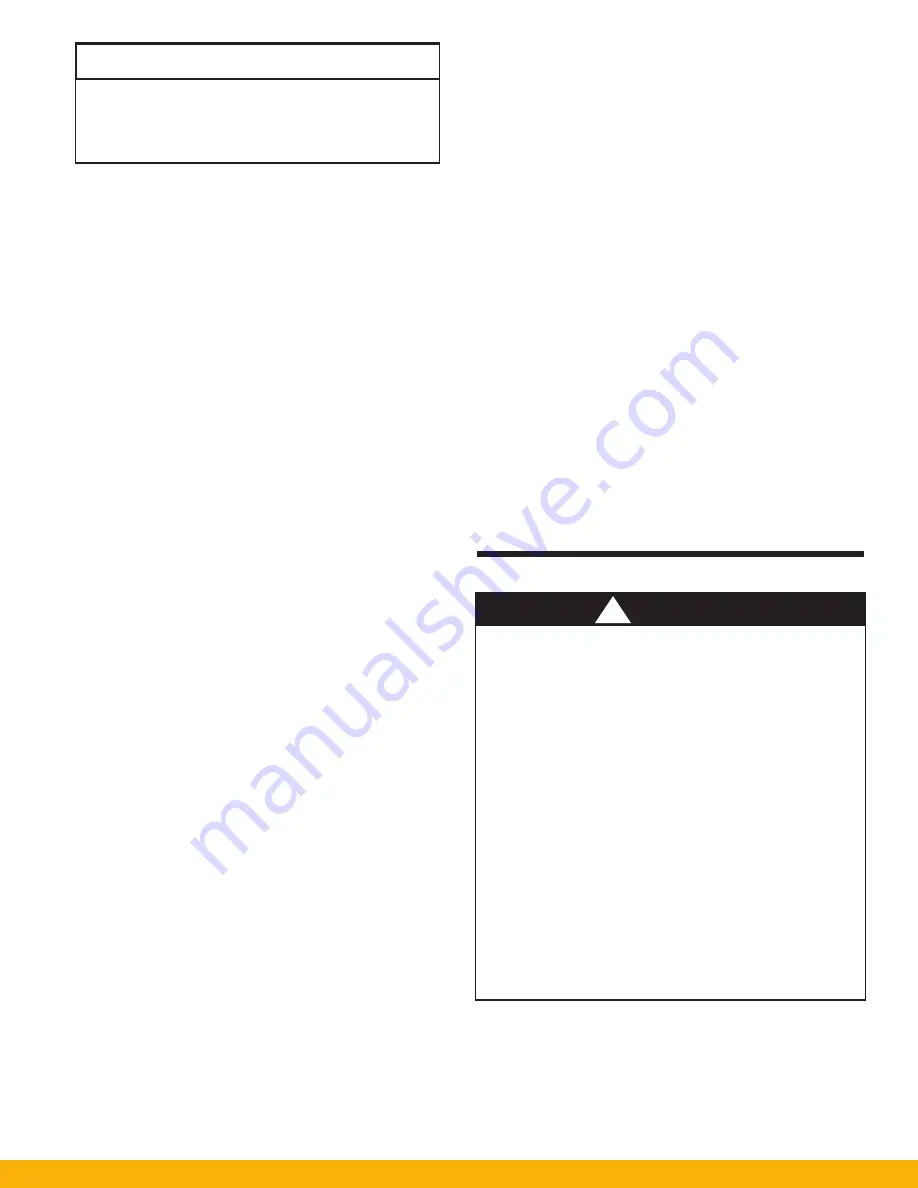
24
Verify dust collector system airflow is adjusted to design
conditions with a new, clean filter using the volume
control dampers installed in the system. Failure to prop-
erly adjust system airflow will affect cartridge filter life.
The air volume should be adjusted based on the performance
of the entire system. The air volume control damper must be
adjusted to the system design airflow. Closing the volume
control damper decreases system airflow. Opening the volume
control damper increases system airflow.
Turn on the compressed air supply to the dust collector air
manifold reservoir. Adjust the pressure regulator until the
gauge reads 90-110 PSIG (6.2-7.6 BAR).
4.2 Checklist
Check the discharge of the blower assembly. Initially,
some
dust may discharge from the blower assembly as the filters are
being seasoned. This may last several minutes after which the
discharge air should remain visibly clean.
Measure the total airflow and static pressure at the inlet to the
SFC unit. Adjust the blower damper for the desired airflow.
Check to ensure that adequate air is being drawn into each
of the collection points of the system. Adjust the individual
dampers for each operation to balance the system airflow.
Recheck the total system airflow and adjust the blower damper
to desired system airflow. This procedure may need to be
repeated several times until the entire system is within system
design airflow specifications.
Check the differential pressure reading across the dust collector
clean-to-dirty air sections. A normal differential pressure drop
reading is between 1”-5” w.g. (25-127 mmAq). At start-up,
this reading is generally in the 1”-3” w.g. (25-76 mmAq) range.
Please list the reading here for future reference.
Initial dust collector differential pressure reading across filters is
__________” w.g. or __________ (mmAq) on __________ (date).
4.3 Checking the Pulse Cleaning System
Confirm the type of pulse cleaning controller delivered with your
system. Your system was delivered with one of the following:
• DPM Pulse Control Panel
• DPC Pulse Monitor Panel
Check the pulse cleaning system for proper operation. The
compressed air pressure should be between 90-110 PSIG
(6.2-7.6 BAR). Parker’s pulse control panels are factory set to
pulse every 10 seconds. Refer to the DPM/DPC Installation
and Operation Manual specified with the dust collector to
change these initial settings. Check to ensure the pulse
(diaphragm) valves are “firing” at approximately 10-second
intervals and deliver a crisp sounding pulse to each filter.
The valves should not deliver a weak sound. If an extended
“hiss” is heard afterwards, the pulse is too long, which does not
assist in cleaning, and wastes compressed air.
• If your system is supplied with a DPM Pulse Monitor Panel,
place the “Continuous Clean/PS” switch on the timerboard
to the “Continuous Clean” position. Or if the system is sup-
plied with DPC Pulse Control, place the “Continuous Clean/
PS” switch on the timerboard to PS position. The MOT AUX
terminals at the timerboard should be field wired for the
pulsing to become active. To activate, energize the motor
starter to close the isolated auxiliary contact wired to the
timerboard MOT AUX terminals. Verify consistent firing of
each solenoid valve exhaust port.
NOTE: It is important that the compressed air pressure is in the
90-110 PSIG range (6.2-7.6 BAR) immediately prior to
pulse. If the delivery capability of your compressed air
source cannot return the manifold pressure to above 90
PSIG during the “Pulse Delay” (factory set at 10 sec.) inter-
val, adjust the pulse delay at the timerboard and monitor
the pressure. A longer interval will raise the operating pres-
sure, which is the pulse delay. (Adjust from position 2 to
position 3 on the timer board.) Allow sufficient time for the
system to stabilize after each adjustment before making
any further adjustment. Adjust until the desired manifold
pressure is reached.
4.3.1 Digital Pulse Monitor (DPM) Panel
The DPM is always set to “Continuous Clean” pulse mode, which
means pulse cleaning is operating continuously when the system
is online. Refer to the DPM/DPC Installation and Operation Manual
for additional information.
4.3.2 Digital Pulse Control (DPC) Panel
The DPC Pulse Control Panel is set for “Pressure Switch” or “PS”
pulse mode. With the DPC control, the desired pressure can be
maintained by adjusting the high and low set-points on the panel.
The factory setting is 3.0 (high set-point) and 2.5 (low set-point).
This allows a 0.5” “deadband” and the pulse system will maintain
the desired pressure. The high and low set-points on the DPC can
be adjusted as the filters season and continuous pulsing occurs.
Adjust upward in 0.5” increments until pulsing stops. Continue
adjustments, when required, until the high set-point reaches 5”.
No further adjustments should be made over 5” w.g.
5. Service
Before servicing dust collector:
• Wear appropriate protective clothing when servic-
ing dust collector.
•Disconnect and lockout electrical power to the unit
and control panel.
•Close off and slowly bleed the compressed air
supply from the air manifold reservoir. Air manifold
reservoir pressure should be reduced to 0 PSIG (0
BAR).
•Collected dust may be hazardous. Consult proper
authorities for handling and disposal.
• Collected dust may be a potential fire hazard.
Welding, grinding or operations involving open
flames should not be performed without fire pro-
tection measures in place. Refer to Section 1 of
this manual for additional precautions.
• Disposal of collected dust must be according to
federal, state and local regulations and all appropri-
ate authorities.
5.1 Cartridge Filter Removal and Replacement
ProTura
®
Nanofiber filters are the only replacement filters which pro-
vide the highest level of performance expected from the SFC Dust
Collector.
CAUTION
!
D A N G E R
Summary of Contents for SFC
Page 1: ...Downward Flow Cartridge Dust Collector Owner s Manual Model SFC...
Page 7: ...v Page intentionally left blank...
Page 11: ...4 FIGURE 2 SFC Typical SINGLE UNIT Installation Diagram PARKER PARKER 44 10335 0001...
Page 12: ...5 FIGURE 3 Recommended Unit Clearances 44 10337 0001...
Page 14: ...7 FIGURE 4 Single Hopper SFC 44 10309 0001...
Page 15: ...8 FIGURE 5 Multiple Hopper SFC 44 10309 0002...
Page 16: ...9 FIGURE 6 Multiple Hopper SFC 44 10309 0003...
Page 17: ...10 FIGURE 7 Multiple Modules SFC 44 10310 0001...
Page 19: ...12 FIGURE 8 SFC Pressure Gauge Installation 44 10333 0001 Rev A...
Page 20: ...13 FIGURE 9 Solenoid Wiring to Pulse Controls for 2 3 4 and 5 Tier Units...
Page 21: ...14 FIGURE 10 Pneumatic Valve Assembly 44 10332 0001...
Page 24: ...17 FIGURE 12 Abrasive Inlet Installation 44 10338 0001...
Page 27: ...20 FIGURE 16 EDAP Interconnection FIGURE 15 EDAP Installation 48 10007...
Page 30: ...23 FIGURE 17 SFC Series Door Filter Installation 44 10329 0001...
Page 37: ...30 7 Illustrated Parts FIGURE 21 SFC Series 44 10330 0001 FIGURE 22 SFC Series Explosion Vents...