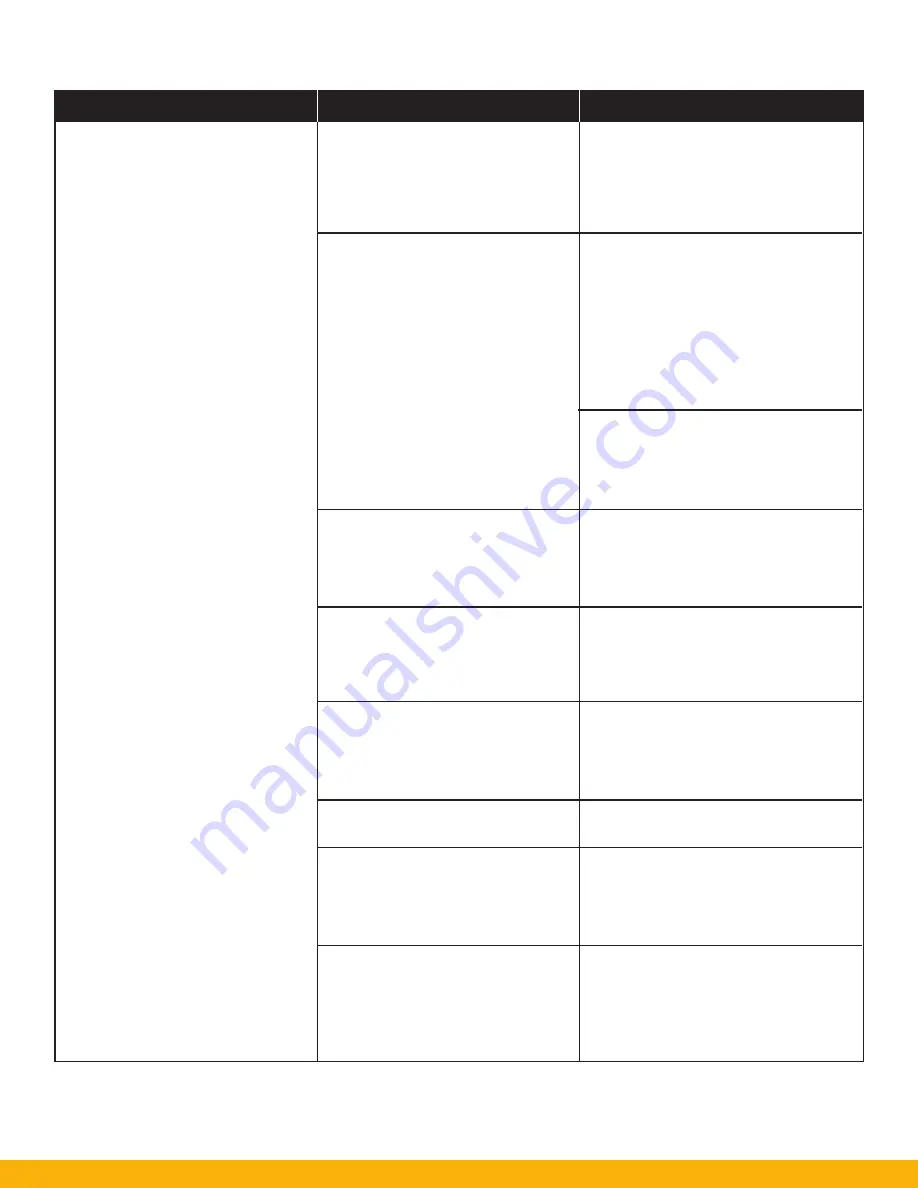
29
PROBLEM
Continual, excessive pressure drop
(over 5” [127 mmAq]) on filter monitor-
ing panel.
POSSIBLE CAUSES
Compressed air supply problems.
Pulse cleaning system not functioning
properly.
DPC not properly adjusted.
Pulse system not properly adjusted.
Pulse settings incorrect.
Dust storage drum is full.
Filters are at the end of their service life.
Air inlet and/or outlet ducting are
undersized.
RECOMMENDED SOLUTIONS
Check incoming compressed air for proper
supply at air manifold reservoir (90-110 PSIG
[6.4-7.2 BAR]), pulse flow (1.7 SCF standard
cubic feet [48.1 liters] per pulse)) and pulse
duration (100 milliseconds). Correct any prob-
lems.
Check incoming 110-115 VAC power to
cleaning control panel. Check control panel
boards for blown fuses. Check 110-115 VAC
supply power circuit (transformer, primary/
secondary fuses, etc.). Replace as necessary.
Consult the cleaning control panel Installation
and Operation Manual for additional trouble-
shooting procedures.
Check for 110-115 VAC supply voltage to the
timer board and voltage output from timer-
boards to solenoid valves. Consult DPM/DPC
Pulse Control Panel Installation and Operation
Manual for additional assistance.
Reduce high set-point on DPC to 3” (76
mm). Reduce low set-point on DPC to 2.5”
(64 mm) (refer to Section 5.4 or DPM/DPC
Pulse Control Panel Installation and Operation
Manual ).
Check for proper pulse valve operation (refer
to Section 5 or DPM/DPC Pulse Control Panel
Installation and Operation Manual ). Replace
damaged parts as necessary.
Adjust pulse duration to 0.100 seconds
(position 3). Adjust pulse delay interval to
10 seconds (position 2). Consult DPC/DPM
Pulse Control Panel Installation and Operation
Manual for additional assistance.
Empty drum and clean out hopper (refer to
Section 6.3).
Replace cartridge filters with ProTura
®
Nanofiber cartridge filters from Parker. Each
cartridge filter has a filter part number affixed
to end cap (refer to Table 2 for the ProTura
®
Nanofiber cartridge filters).
Increase air inlet and/or ducting sizes to reduce
duct line static pressure losses. Follow duct-
ing design methods as listed in Industrial
Ventilation Manual by American Conference of
Governmental Industrial Hygienists.
Summary of Contents for SFC
Page 1: ...Downward Flow Cartridge Dust Collector Owner s Manual Model SFC...
Page 7: ...v Page intentionally left blank...
Page 11: ...4 FIGURE 2 SFC Typical SINGLE UNIT Installation Diagram PARKER PARKER 44 10335 0001...
Page 12: ...5 FIGURE 3 Recommended Unit Clearances 44 10337 0001...
Page 14: ...7 FIGURE 4 Single Hopper SFC 44 10309 0001...
Page 15: ...8 FIGURE 5 Multiple Hopper SFC 44 10309 0002...
Page 16: ...9 FIGURE 6 Multiple Hopper SFC 44 10309 0003...
Page 17: ...10 FIGURE 7 Multiple Modules SFC 44 10310 0001...
Page 19: ...12 FIGURE 8 SFC Pressure Gauge Installation 44 10333 0001 Rev A...
Page 20: ...13 FIGURE 9 Solenoid Wiring to Pulse Controls for 2 3 4 and 5 Tier Units...
Page 21: ...14 FIGURE 10 Pneumatic Valve Assembly 44 10332 0001...
Page 24: ...17 FIGURE 12 Abrasive Inlet Installation 44 10338 0001...
Page 27: ...20 FIGURE 16 EDAP Interconnection FIGURE 15 EDAP Installation 48 10007...
Page 30: ...23 FIGURE 17 SFC Series Door Filter Installation 44 10329 0001...
Page 37: ...30 7 Illustrated Parts FIGURE 21 SFC Series 44 10330 0001 FIGURE 22 SFC Series Explosion Vents...