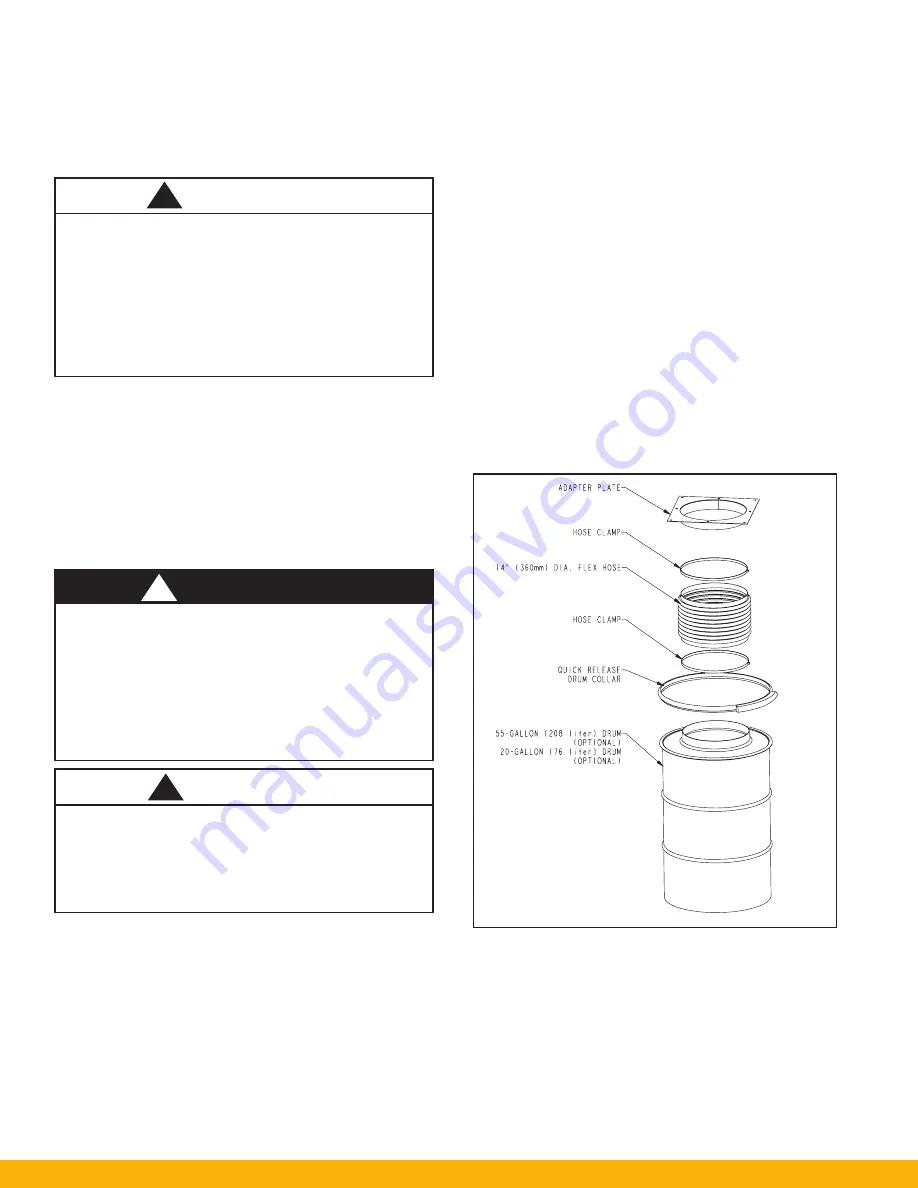
18
3.6.2 Duct Silencer Installation
A duct-type (in-line) silencer is designed to bolt directly to the blow-
er outlet damper flange. Make certain there is adequate room for
the silencer in the discharge direction. Provide at least 24” (61 cm)
of unobstructed space at the end of the silencer discharge. The air
discharge should be directed into an open area, free of obstructions
and with consideration for personnel safety.
CRUSH HAZARD
The silencer will require a separate support. Do not
use the blower damper or outlet flange to support the
silencer. Apply silicone around the bolt holes of the
connecting flanges, lift the silencer into position and
secure with the hardware provided. Install permanent
supports (customer-supplied) and tighten all hard-
ware before removing the lifting device.
3.6.3 Rotary Air Lock Installation
If a rotary air lock was ordered with the unit, the hopper discharge
will have an adapter already bolted to it. Make certain the bolts
connecting the adapter to the hopper discharge are securely
tightened.
Remove all packing from the rotary air lock and determine its
appropriate position. Keep in mind required clearances, electrical
connections and maintenance. Apply sealant to the flange of the
rotary air lock and to the adapter using 3/8” bolts, washers and
lock washers.
ELECTRICAL SHOCK HAZARD
Disconnect and lockout all power to the rotary
air lock before servicing. All electrical connections
should be made by a qualified electrician according
to all applicable codes. Refer to the nameplate and/
or documentation for voltage, amperage, cycle and
proper wiring. Refer to rotary air lock vendor docu-
mentation attached with air lock device.
MOVING PARTS
There are moving parts on the rotary air lock. Do not
allow any object to be placed in or near the rotary air
lock during operation. Verify rotary air lock rotation
matches rotation arrows affixed to assembly.
3.6.4 Abrasive Inlet Installation
The abrasive inlet is designed to use the front access panel(s) of
the SFC Series modules as the inlet area to the unit. There are two
styles available – a single or dual module abrasive inlet. Each is
designed to fit over the appropriate number of front access panels
to serve as a single inlet point for one or two modules (refer to
Figure 12).
Remove the front access panel(s) located above the QuickSeal
filter access doors. Save the hardware. The hardware will be used
to attach the abrasive inlet. Remove any remaining gasket material
from around the perimeter of the opening.
Apply a 1/4” (6 mm) bead of sealant around the perimeter of
the access opening in a “figure 8” pattern around the bolt holes.
Align the hole pattern on the abrasive inlet with the hole pat-
tern on the unit and bolt together using the hardware removed
earlier. Fasten the inlet ducting securely to the abrasive inlet
assembly.
The bottom plate of the abrasive inlet will serve as an inspec-
tion plate. If access to the abrasive inlet is required, remove
and clean out the bottom plate of the inlet prior to servicing. Do
not damage the ribbon of gasket and reuse after cleaning the
gasket surfaces.
3.6.5 Drum Lid Installation
The drum lid package is an optional accessory for the SFC
Series dust collectors. Refer to Figure 13.
Remove the drum lid package from it shipping carton. Place the
drum lid on the 55-gallon (208 liter) drum or the 20-gallon (76
liter) drum. Slide the 14” (360mm) diameter hose over the drum
lid and secure with hose clamp. Position the drum assembly
under the unit, slide the hose up onto the 14” adapter collar on
the hopper and secure it with a clamp.
!
D A N G E R
44-10046-0001
FIGURE 13
Drum Lid Installation
!
WARNING
!
WARNING
Summary of Contents for SFC
Page 1: ...Downward Flow Cartridge Dust Collector Owner s Manual Model SFC...
Page 7: ...v Page intentionally left blank...
Page 11: ...4 FIGURE 2 SFC Typical SINGLE UNIT Installation Diagram PARKER PARKER 44 10335 0001...
Page 12: ...5 FIGURE 3 Recommended Unit Clearances 44 10337 0001...
Page 14: ...7 FIGURE 4 Single Hopper SFC 44 10309 0001...
Page 15: ...8 FIGURE 5 Multiple Hopper SFC 44 10309 0002...
Page 16: ...9 FIGURE 6 Multiple Hopper SFC 44 10309 0003...
Page 17: ...10 FIGURE 7 Multiple Modules SFC 44 10310 0001...
Page 19: ...12 FIGURE 8 SFC Pressure Gauge Installation 44 10333 0001 Rev A...
Page 20: ...13 FIGURE 9 Solenoid Wiring to Pulse Controls for 2 3 4 and 5 Tier Units...
Page 21: ...14 FIGURE 10 Pneumatic Valve Assembly 44 10332 0001...
Page 24: ...17 FIGURE 12 Abrasive Inlet Installation 44 10338 0001...
Page 27: ...20 FIGURE 16 EDAP Interconnection FIGURE 15 EDAP Installation 48 10007...
Page 30: ...23 FIGURE 17 SFC Series Door Filter Installation 44 10329 0001...
Page 37: ...30 7 Illustrated Parts FIGURE 21 SFC Series 44 10330 0001 FIGURE 22 SFC Series Explosion Vents...