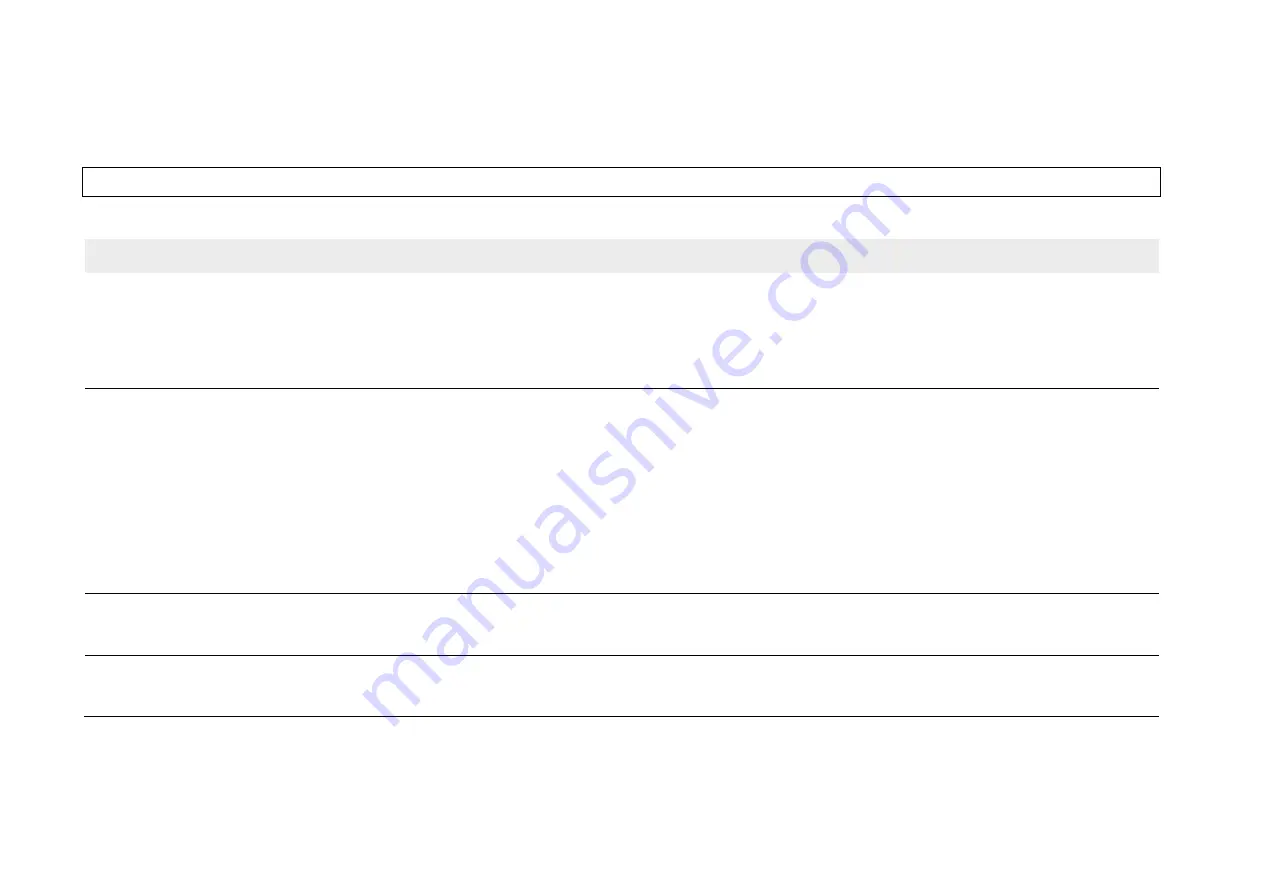
D-44
Programming
890CS Common Bus Supply - Frames B & D; 890CD Common Bus Drive and 890SD Standalone Drive - Frames E & F
FEEDBACKS
SETUP::MOTOR CONTROL::FEEDBACKS
Designed for all Motor Control Modes.
The FEEDBACKS block allows you to view speed feedback and motor current related diagnostics.
Parameter Descriptions
QUADRATIC TORQUE
PREF: 70.01
Default: FALSE
Range: FALSE/TRUE
Designed for all Motor Control Modes.
When TRUE, selects QUADRATIC allowing higher continuous ratings with less overload capability. Quadratic Torque
operation is especially suited to fan or pump applications. When FALSE, selects CONSTANT duty.
OVERLOAD LEVEL
PREF: 70.20
Default: HIGH
Range: See below
Designed for all Motor Control Modes, except PMAC control mode.
This reduces I*t limit for shaftless printing applications. However, with OVERLOAD LEVEL set to LOW, no pwm
frequency reduction occurs during overload conditions.
Enumerated Value : Level
0 : LOW
130% for 60s : sets the I*t limit
1 : HIGH
150% for 60s : sets the I*t limit
DC LINK VOLTS
PREF: 70.02
Default: —. V
Range: —. V
This shows the voltage across the dc link capacitors.
TERMINAL VOLTS
PREF: 70.03
Default: —. V
Range: —. V
This shows the rms voltage, between phases, applied by the Drive to the motor terminals.