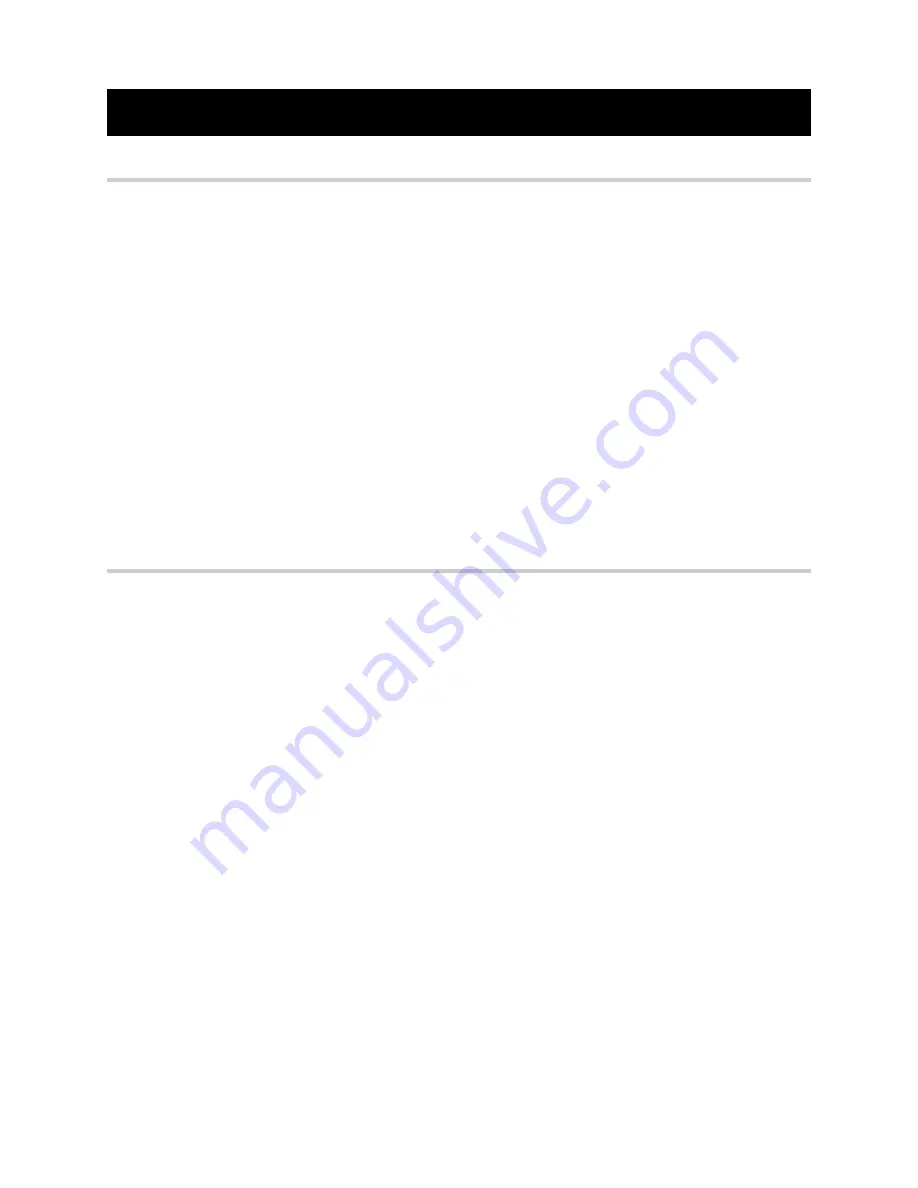
10-1
Certification for the Drive
650G AC Drive
Chapter 10
C
ERTIFICATION FOR THE
D
RIVE
Requirements for EMC Compliance
Earthing Requirements
IMPORTANT:
Protective earthing always takes precedence over EMC earthing.
Protective Earth (PE) Connections
Note:
In accordance with installations to EN60204, only one protective earth conductor is
permitted at each protective earth terminal contacting point.
Local wiring regulations may require the protective earth connection of the motor to be
connected locally, i.e. not as specified in these instructions. This will not cause shielding
problems because of the relatively high RF impedance of the local earth connection.
EMC Earth Connections
For compliance with EMC requirements, the “0V/signal ground” is to be separately earthed.
When a number of units are used in a system, these terminals should be connected together at a
single, local earthing point.
Control and signal cables connections should be made with screeened cables, with the screen
connected only at the VSD end. However, if high frequency noise is still a problem, earth screen
at the non VSD end via a 0.1
µ
F capacitor.
Note:
Connect the screen (at the VSD end) to the VSD protective earth point, and not to the
control board terminals.
Requirements for UL Compliance
Solid-State Motor Overload Protection
These devices provide Class 10 motor overload protection. The maximum internal overload
protection level (current limit) is 150% for 30 seconds.
An external motor overload protective device must be provided by the installer where the motor
has a full-load ampere rating of less than 50% of the drive output rating; or when the DISABLE
STALL trip (
S
STLL) is set to True (1); or when the STALL TIME parameter is increased above
480 seconds (refer to the 650G Software Manual, Chapter 1 : STALL TRIP.
Motor over temperature sensing is required. Motors used in conjunction with the drive
controller shall be protected with PTC sensor(s) or relays suitable for use with the variable speed
drive. Technical details can be found in Chapter 3 Installing the Drive.
Short Circuit Rating
The following drives are suitable for use on a circuit capable of delivering not more than:
220-240V product, 1
φ
- 5000 RMS Symmetrical Amperes
220-240V product, 3
φ
- 7500 RMS Symmetrical Amperes
380-460V product, 3
φ
-10000 RMS Symmetrical Amperes
Solid-State Short-Circuit Protection
These devices are provided with Solid-State Short-Circuit (output) Protection. Branch circuit
protection requirements must be in accordance with the latest edition of the National Electrical
Code NEC/NFPA-70.
Recommended Branch Circuit Protection
It is recommended that UL Listed (JDDZ) non-renewable cartridge fuses, Class K5 or H; or UL
Listed (JDRX) renewable cartridge fuses, Class H, are installed upstream of the drive.
Motor Base Frequency
The motor base frequency rating is 240Hz maximum.
Field Wiring Temperature Rating
Use 75°C Copper conductors only.