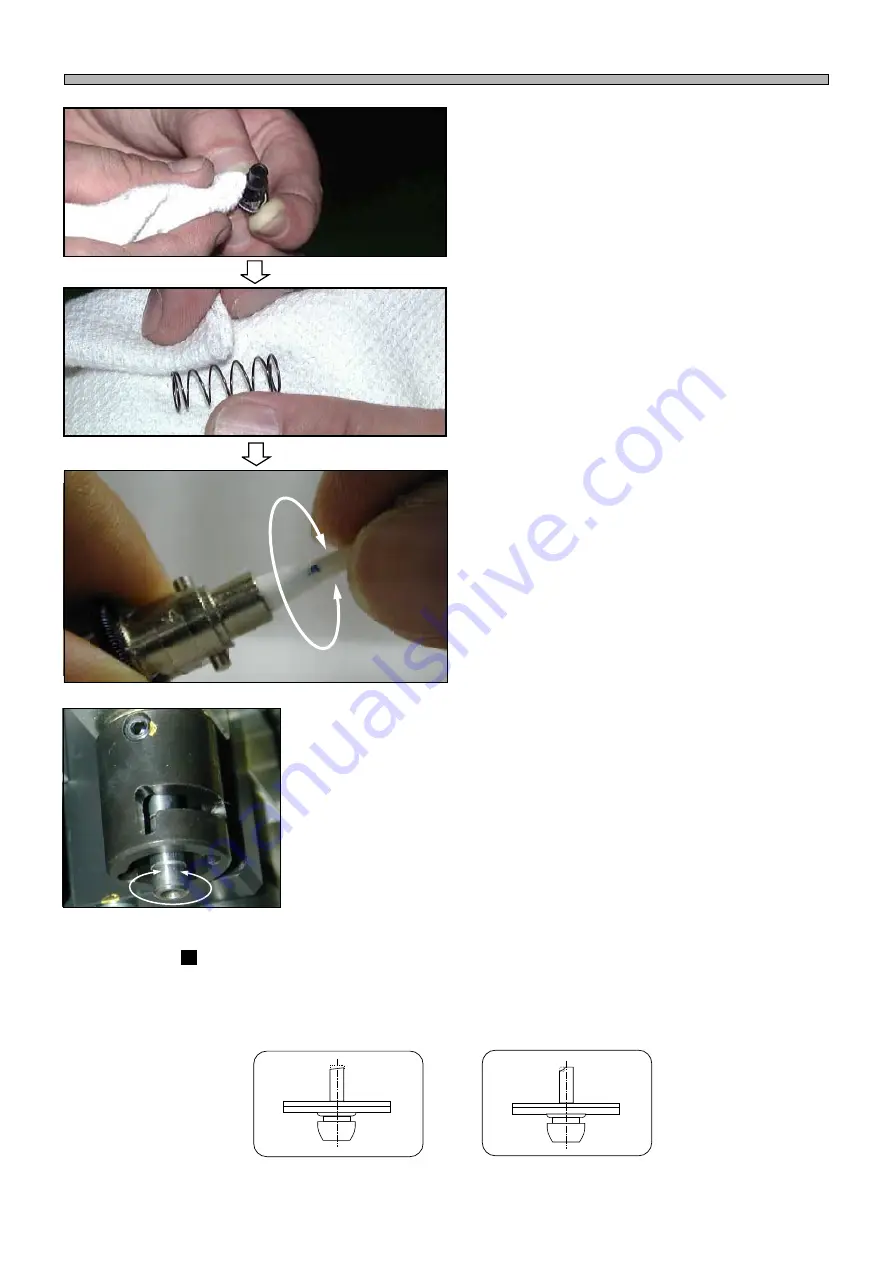
Page 1-34
Check Every 140 Hours (Once a Week)
4.
Clean dirt on the outer circumference
of the nozzle holder with a cloth.
5.
Clean dirt on the spring for nozzle
cushion with a cloth.
6
. Soak a swab in alcohol, insert it into
the nozzle holder, and turn it in
θθθθθ
direction two or three times.
∗
The nozzle holder should be set aside until the
internal alcohol dries up.
7
. Wipe up the contamination of the
outer regions of the nozzle-holder
shaft, with a cloth soaked in alcohol.
∗
The nozzle-holder shaft should be set aside
until the alcohol in the outer regions dries up.
Checking the nozzle tip
You need to check for wear of and damage to the nozzle tip for stable pickup. When the
nozzle tip looks like following drawings, it is necessary to exchange the nozzle.
In cleaning the nozzle tip, also check for it.
444C-E-MMA01-A05-06
444C-471P
444C-426P
Wear of the nozzle tip
Damage to the nozzle tip
444C-403E
444C-404E
444C-521P
E24C-407P