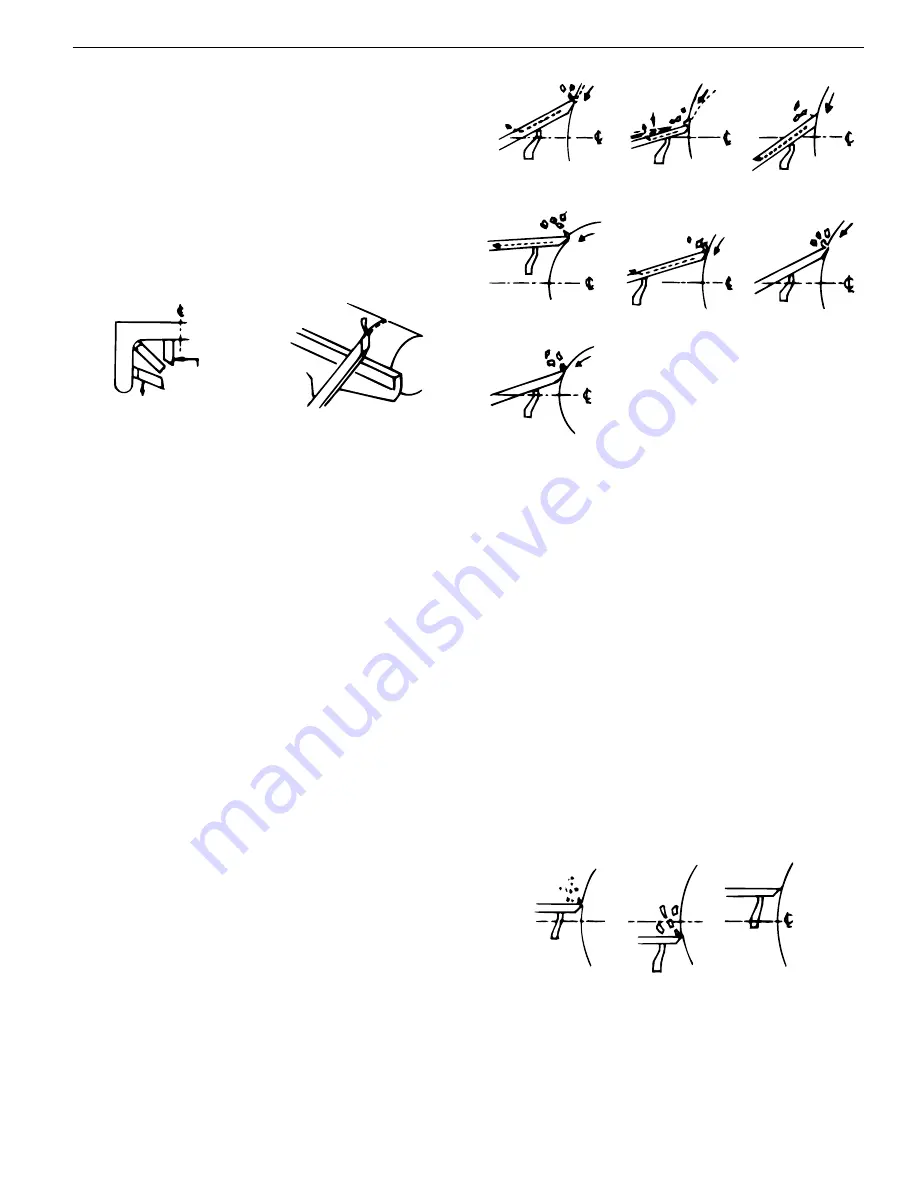
9
Palmgren Operating Manual & Parts List
84315
OPERATION (CONTINUED)
When You Can Cut and When You Must Scrape
There are two different approaches:
•
One approach is toward a circumference of the workpiece (for
example turning down the outer surface of a cylinder or the
inner wall of a hollow round box). In this approach, the surface
being turned travels under the chisel edge like an endless belt.
•
The second approach is toward the diameter of a workpiece (as
when turning the face of a faceplate turning, or the side of a
large shoulder on a spindle turning). In this approach, the sur-
face being turned rotates like a disc under the chisel edge.
•
Sometimes the optimum approach will be a combination of
both methods.
Either a cutting or scraping action can be used when the approach
is toward a circumference – the shaving is removed like a peeling
from a potato. Scraping can only be used when the approach is
toward a diameter. The reason is obvious when you consider that
faceplate turning practically always requires removal of wood
across the grain. Wood does not peel easily across the grain and
attempts to use any inappropriate cutting methods will likely
result in damage to the workpiece. There is also danger that the
tool could be pulled from the hands of the operator.
In general, a cutting action is used for the majority of spindle turn-
ing operations while faceplate turning is usually accomplished by
the scraping method. When a combination approach is to be used,
the operator will have to judge, by the feel of the work, when to
stop cutting and start scraping.
Never
try to cut when it becomes
difficult to hold the chisel against the roughness of the wood grain.
How to Position Tool Rest for Circumference Cutting
When cutting, the object is to pierce the outer skin of wood to a
certain desired depth and then to hold the chisel steady with the
bevel edge parallel to the work circumference so that it will peel
off a shaving at this desired depth.
•
The only sure method of holding the chisel steady is to rest the
bevel against the work (Figure 25A). When the tool rest is at the
proper height, the chisel can be held with the bevel pressed
against the work, and the tool rest will act as a fulcrum to sup-
port the chisel against the downward force of the revolving
work.
•
If the rest is placed too low, so that the chisel is held with the
bevel out from the work (Figure 25B), the cutting edge will con-
tinue to dig deeper into the work. It will dig in until the “bite”
becomes so deep that your hands have difficulty holding the
chisel – then the improperly supported chisel will begin to
bounce or chatter against the workpiece.
•
If the rest is placed too low, the chisel must be held extremely
high to position the bevel against the work (Figure 25C). Then
the rest loses most of its value as a fulcrum and the downward
force of the revolving workpiece tends to kick the chisel back
out of your hands.
•
If the rest is placed too high (Figure 25D) and the chisel is cor-
rectly positioned for cutting, it strikes the workpiece near the
top where the direction of force exerted by the workpiece is
nearly horizontal – and kickback will again result.
•
If the rest is placed too far out from the work surface (Figure
25E), then, when correctly held, the chisel is again too high on
the work. Also, you have less leverage on your side of the tool
rest and it is even more difficult to hold the chisel. With large
diameter work (Figure 25F), the tool rest can be above the
workpiece centerline, and somewhat out from the work sur-
face. With small diameter work (Figure 25G), the rest should be
closer to the work surface. As work grows smaller, the rest
should be repositioned.
How to Position Tool Rest for Circumference Scraping
In scraping operations, the tool rest position is not as critical as it is
for cutting operations.
•
The chisel generally is held horizontally, though it can be held
at an angle to reach into tight places. Considering that the wire
edge of the chisel does the scraping, Figures 26B and 26C show
the results of too low or too high a position for the rest.
•
Figure 26A shows the chisel action with the rest correctly
positioned.
How to Position Chisel and Rest for Diameter Scraping
When scraping on the diameter, that portion of surface to the right
of center is moving upward (Figure 27A). If a chisel is placed in this
area, it will simply be carried up off the rest and out of your hands.
•
All diameter approach operations must be done at the left of
center.
Diameter
Approach
Circumference
Approach
Figure 24
Steady
Thrust
Against
Hands
Chatter
Kickback
Kickback
Bevel
Against
Work
Chisel Rest
Too High
On Work
Handle
Kicked Up
Large
Diameter
Small
Diameter
No Support
For
Bevel
Point
Digging In
Chisel Cutting Properly
Rest Too Distant - Chisel Too High
Point Too Far From Rest
Rest Too Low
Chisel Too Horizontal
Rest
Too Low
Chisel
Too High
Figure 25
Fig. 25A
Fig. 25B
Fig. 25C
Fig. 25D
Fig. 25G
Fig. 25E
Fig. 25F
No Stock
Removed
Edge
Digging
In
Correct
Figure 26
Fig. 26A
Fig. 26B
Fig. 26C