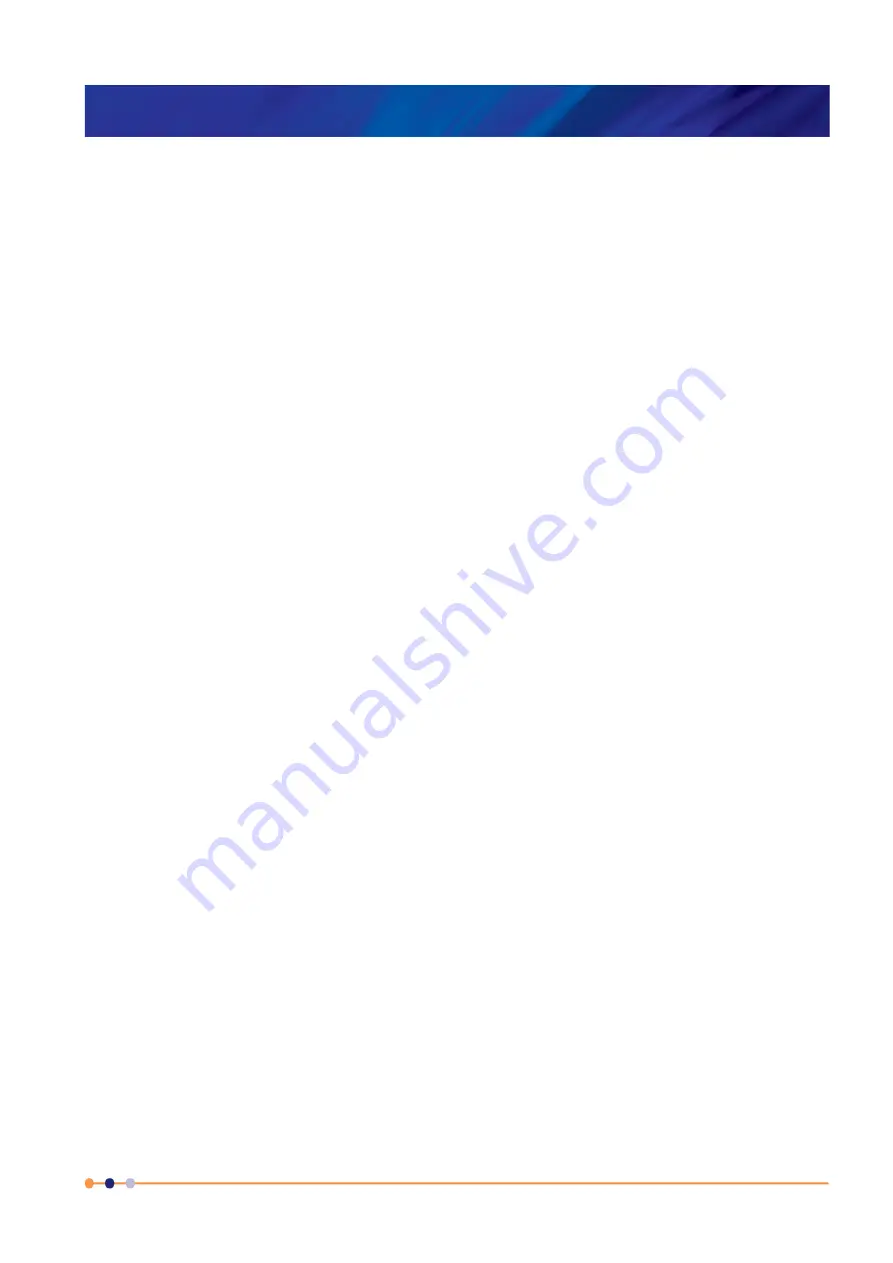
Handbook
November 2011
/
59-UMC0071
/
Issue
01
Mercury
iTC
Page 125
THEORY OF CONTROL LOOPS
Original Instructions
9
Tap the second cell in this row and enter the upper temperature for the first
temperature range.
10
Tap the third cell in this row and enter the P parameter for this temperature range in
K.
11
Tap the fourth cell in this row and enter the I parameter for this temperature range in
minutes.
12
Tap the fifth cell in this row and enter the D parameter for this temperature range in
minutes.
13
If required, tap + to add a new row. The first cell of the new row is automatically set
to 0.001K above the upper temperature programmed in the previous row.
14
Continue adding rows until PID parameters have been entered for the entire
temperature range to be used.
15
Tap
Save
to save the table.
16
Tap
Control
to return to the
Control Loop Configuration
page.
12.3
Theory of gas-flow control
12.3.1
Overview of gas control
The iTC can drive a motorised needle valve which controls the flow of a cooling gas.
Controlling the gas-flow, regulates the cooling power, which provides control of the
sample temperature.
12.3.2
Manual control of the gas flow
When the gas control is set to MANUAL mode, the valve is driven to a fixed position to
provide constant cooling power. Temperature control is then provided by controlling the
heater output.
12.3.3
Automatic control of the gas flow
When the gas control is set to AUTOMATIC mode, the position of the needle valve is
automatically controlled to provide variable cooling power. In conjunction with the
heater, this enables accurate temperature control at cryogenic temperatures.
The position of the needle valve is controlled by a control function that operates relative
to the present valve position rather than to an absolute position.
The output of the control function is related to the valve position by a Valve Gearing
parameter. This parameter defines how many steps of the stepper motor exist between
the valve fully-open and the valve fully-closed positions. Changing the Valve Gearing
parameter allows the iTC to match a variety of stepper-motor and needle-valve
combinations.