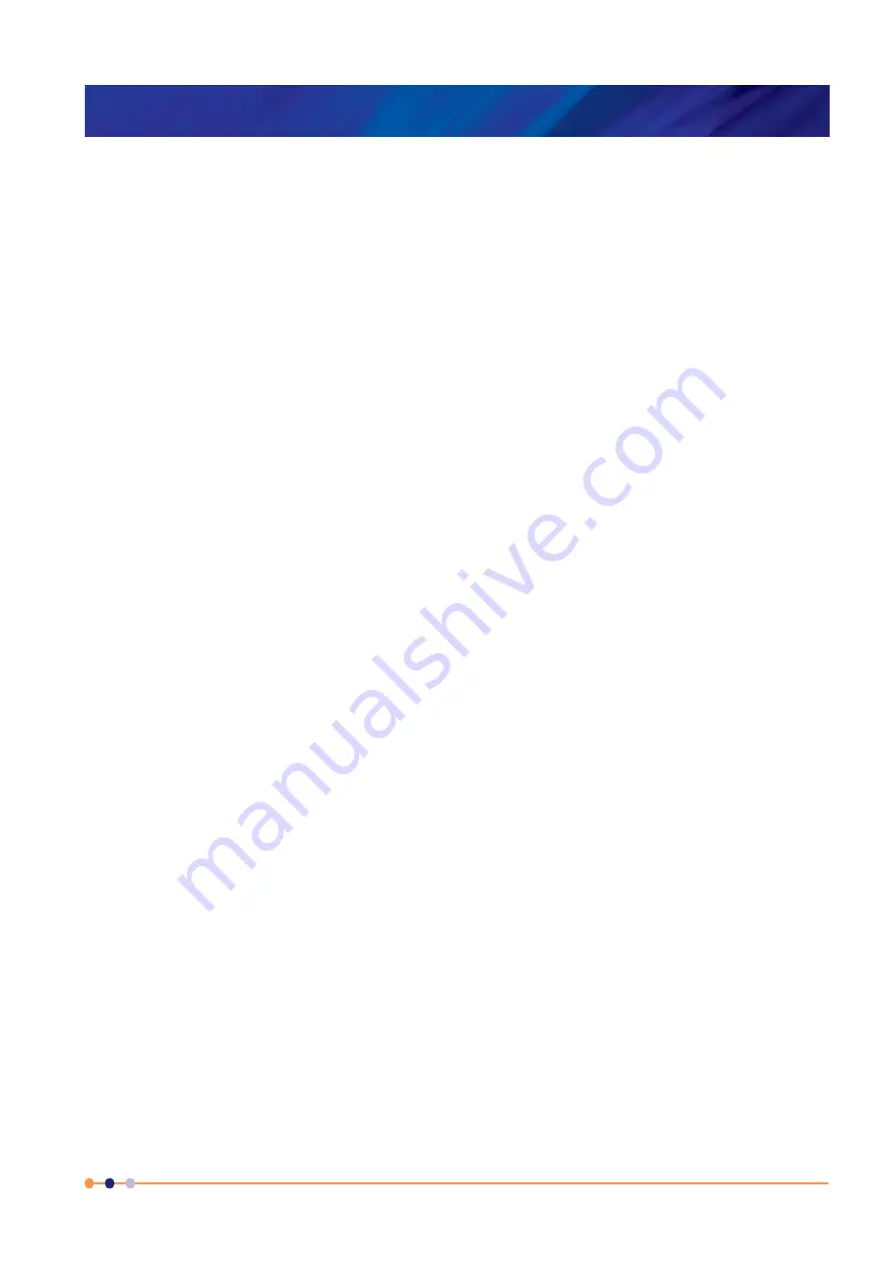
Handbook
November 2011
/
59-UMC0071
/
Issue
01
Mercury
iTC
Page 119
THEORY OF CONTROL LOOPS
Original Instructions
12
THEORY OF CONTROL LOOPS
This chapter describes the general principles of the control loops used in this unit.
12.1
General information on control loops
The iTC uses control loops to control the heater and optional gas valve.
Temperature control of the heaters uses PID control.
Temperature control of the gas valve uses a proprietary algorithm.
Control of temperature by varying the gas valve is slower than control by varying the
heater output. The iTC can be configured to operate using three possible automatic
control methods:
Automatic control of the gas valve with the heater output fixed.
This method provides a slow response to changes in temperature.
Automatic control of the heater output.
This method provides a fast response to rapid falls in temperature, but a slow
response to rapid rises in temperature.
Automatic control of both the gas valve and the heater output.
This usually provides the most stable control, as it can compensate quickly for rapid
rises or falls of temperature
12.2
General information on temperature control loops
A temperature control system consists of the following parts:
A means of measuring the sample temperature (the temperature sensor).
A variable source of heat (the heater).
A control device to monitor the sample temperature and to control the output of the
heater.
A temperature control loop is designed to maintain the temperature of the system as
close as possible to the setpoint. There are several factors that must be considered:
The heat loss from the system, which may vary with time and temperature.
There may be delay between heat being applied to the heater and a change of the
temperature reading of the sensor.
The system must respond as quickly as possible to a change of setpoint.
When a steady-state is established, the heat provided by the controller exactly balances
the heat loss to the surroundings.