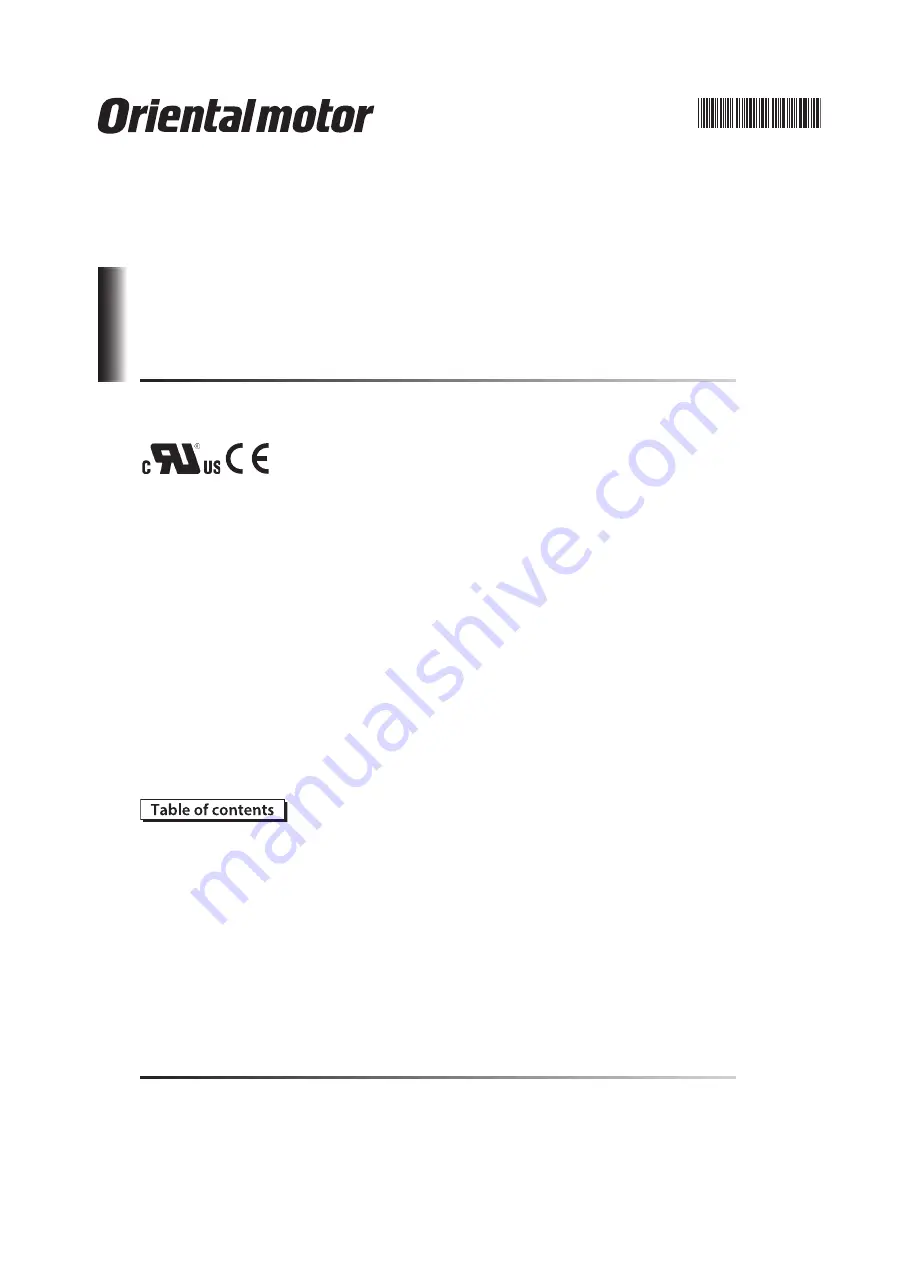
HL-8024-3
Rack and Pinion Systems
LAS
Series
OPERATING MANUAL
Thank you for purchasing an Oriental Motor product.
This Operating Manual describes product handling procedures and safety precautions.
•
Please read it thoroughly to ensure safe operation.
•
Always keep the manual where it is readily available.
1 Introduction .............................. 2
2 Safety precautions ................... 4
3 Precautions for use ................... 7
4 Preparation ................................ 9
5 Installation ...............................13
6 Connection ..............................21
7 Settings ....................................35
8 Protective functions ............... 37
9 Inspection ................................39
10 Troubleshooting and
remedial actions ..................... 40
11 Main specifications ................ 42
12 Options (sold separately) ...... 43