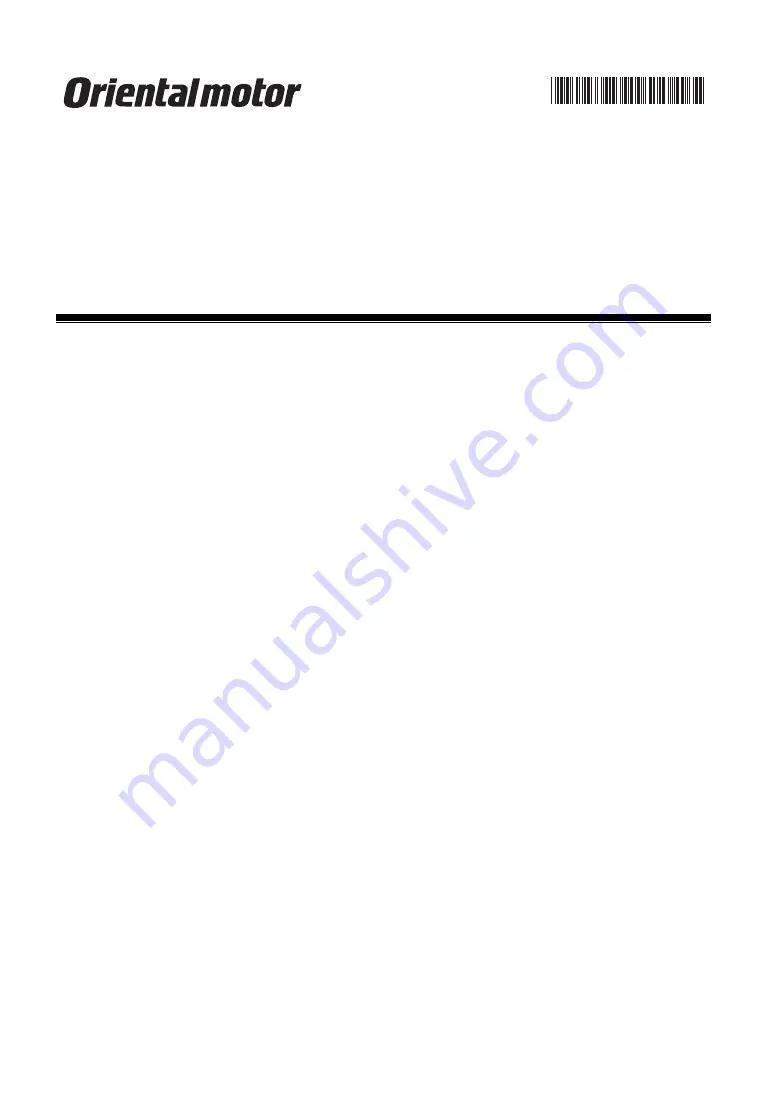
HP-19036-3
Stored Program Controller
EMP400
Series
OPERATING MANUAL
Thank you for purchasing an Oriental Motor product.
This Operating Manual describes product handling procedures and safety precautions.
•
Please read it thoroughly to ensure safe operation.
•
Always keep the manual where it is readily available.
Summary of Contents for EMP400 Series
Page 115: ......