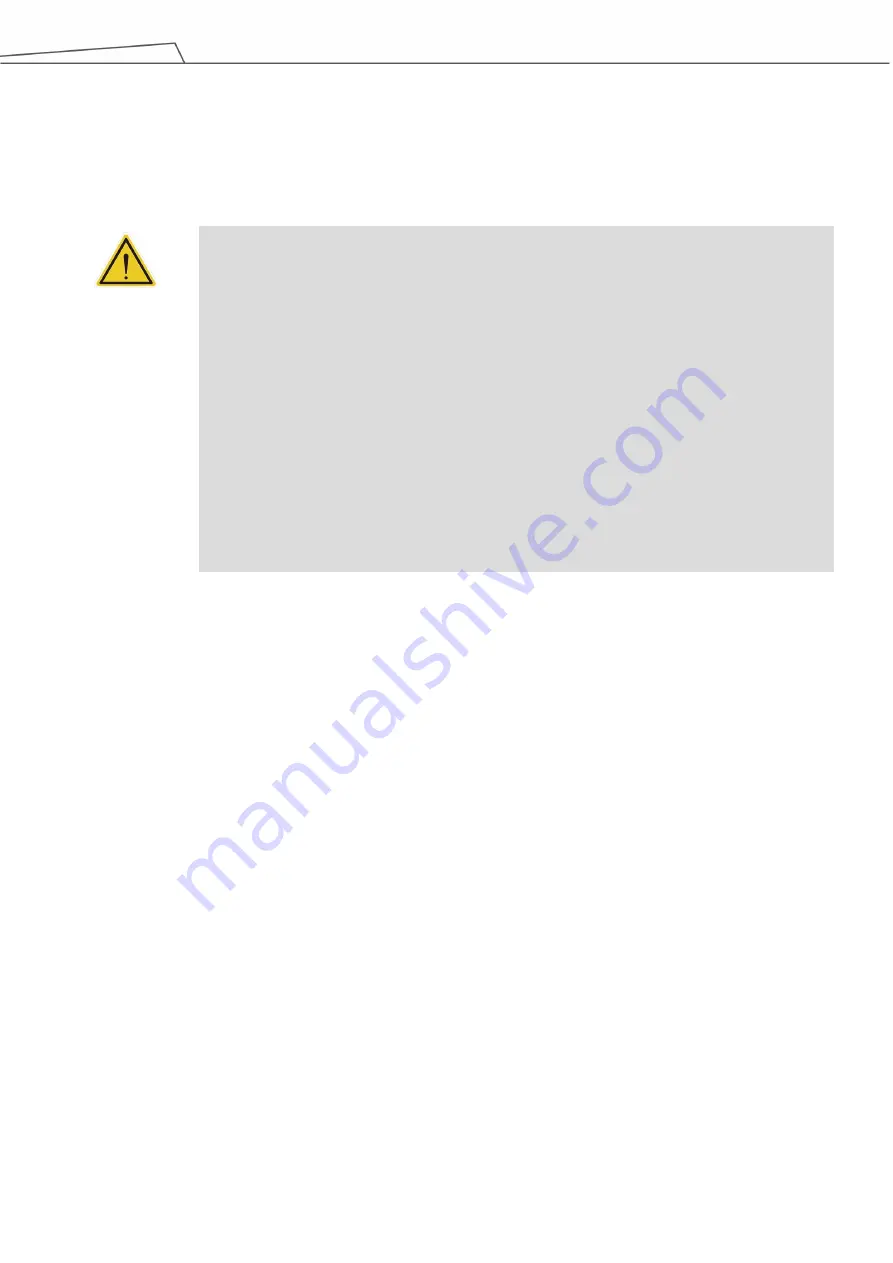
Medium & Heavy Payload Series-Hardware Installation Manual TM12/14 Series Hardware Version: 3.2
69
6. Unboxing & Installation
6.1 Overview
These instructions guide Users of the TM Robot through the first set up. Users must thoroughly read and
understand
this Guide
before performing the operations of this Chapter. Fail to do so may cause serious danger.
6.2 Inspecting the Equipment
6.2.1 Before Unpacking
Carefully inspect all shipping crates for evidence of damage during transit. If any damage is indicated,
request that the carrier's agent be present at the time the container is unpacked
6.2.2 Upon Unpacking
Before signing the carrier’s delivery sheet, compare the actual items received (not just the packing slip)
with your equipment purchase order and verify that all items are present and that the shipment is correct
and free of visible damage. If the items received do not match the packing slip or are damaged, do not
sign the receipt, contact your corporation support as soon as possible. If the items received do not match
your order, contact your corporation support immediately. Inspect each item for external damage as it is
removed from its container. If any damage is evident, contact your corporation support (see HOW Can I
Get Help? on 1.2)
Retain all shipping containers and packaging materials. These items may be necessary to settle claims or
at a later date, to relocate equipment.
WARNING:
If this is your first time using the TM Robot, follow instructions in this chapter to perform
installation and initial set up. If the robot has been implemented in the working environment,
please note the following:
1. To avoid potential hazards after changing the original environment setting, verify with
current responsible operator and to back up all necessary software settings and
hardware wirings scheme.
2. Remove all of the control box's external I/O connections including the analog I/O,
EtherCAT port and network port. Remove all air lines or external power lines connected
to the optional equipment before Commissioning.
3. Remove all of the control box's connections to external devices / external storage
devices through USB interface, Serial port, and network interface.
4. Unload any object/end effector attached to the end flange, and any electrical connection
between the end effector and end module / control box of the robot.
5. Unload any hardware attached to the robot arm.