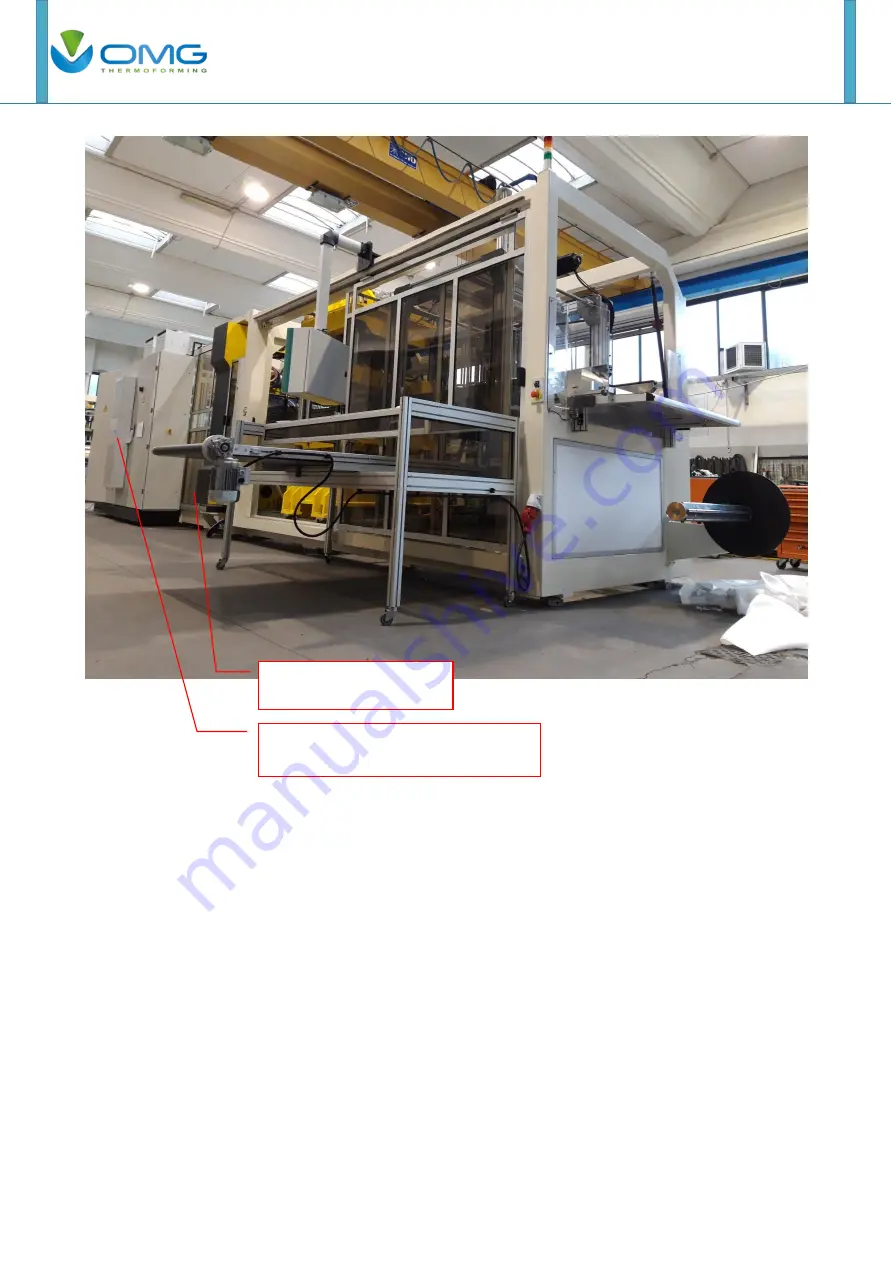
MF 64
Author: Donato Gavino Murru [email protected]
Pag.
22
a
179
Front side
Electrical cabinet - Security doors
with door lock release control
Sliding security doors
MF 64
Author: Donato Gavino Murru [email protected]
Pag.
22
a
179
Front side
Electrical cabinet - Security doors
with door lock release control
Sliding security doors