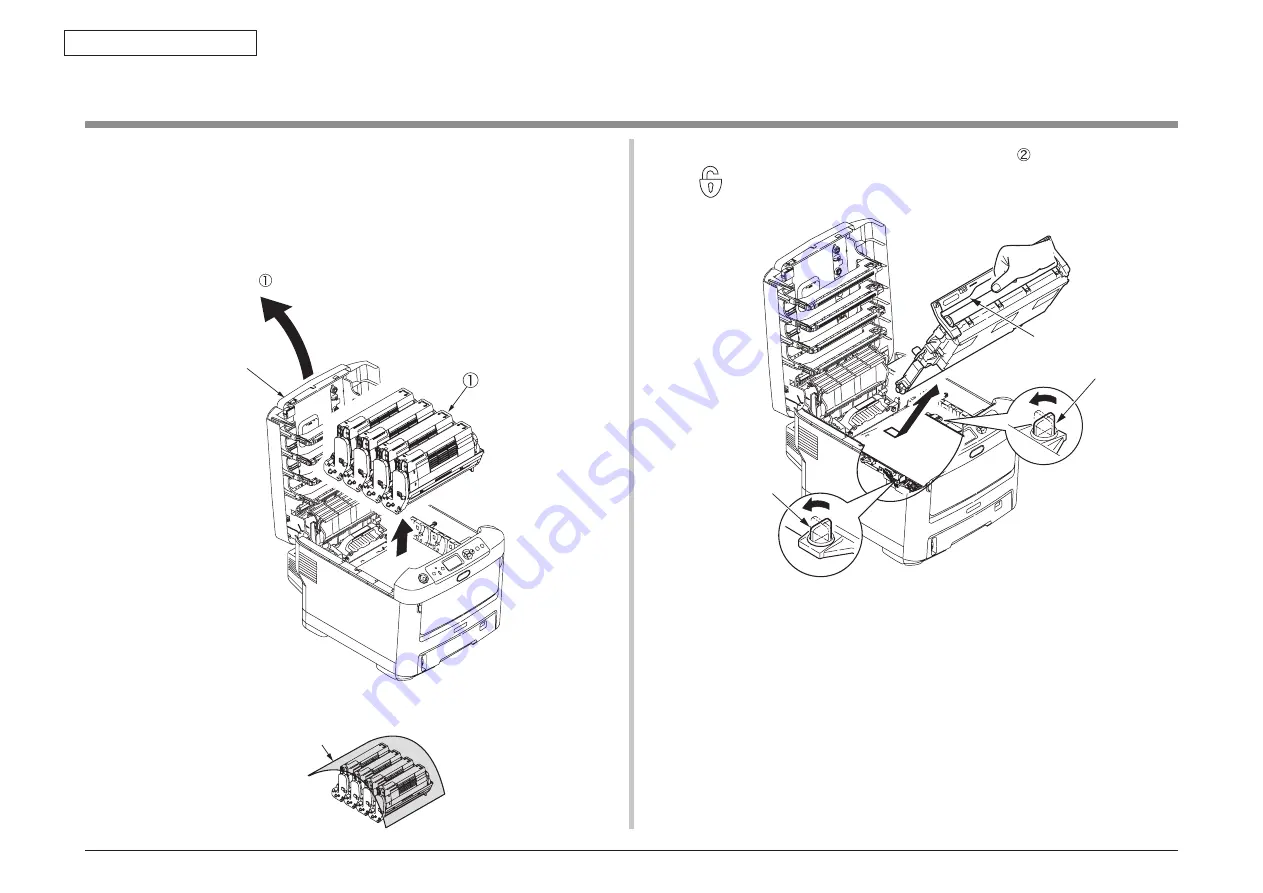
43856301TH Rev.3
63 /
Oki Data CONFIDENTIAL
4. Component replacement
4.2 Method of component replacement
In this chapter, the replacement of parts and assemblies is described by the disassemble
figures.
4.2.1 Belt unit
(1) Open the top cover.
(2) Remove the ID unit .
(3) Rotate the lock lever (blue, 2 places) of the belt unit in the direction of arrow
, and hold the lever (blue) to remove the belt unit.
Top cover
Lock lever (blue)
Lock lever (blue)
Lever (blue)
Note!
Cover the removed image drum cartridge with black paper.
Black paper