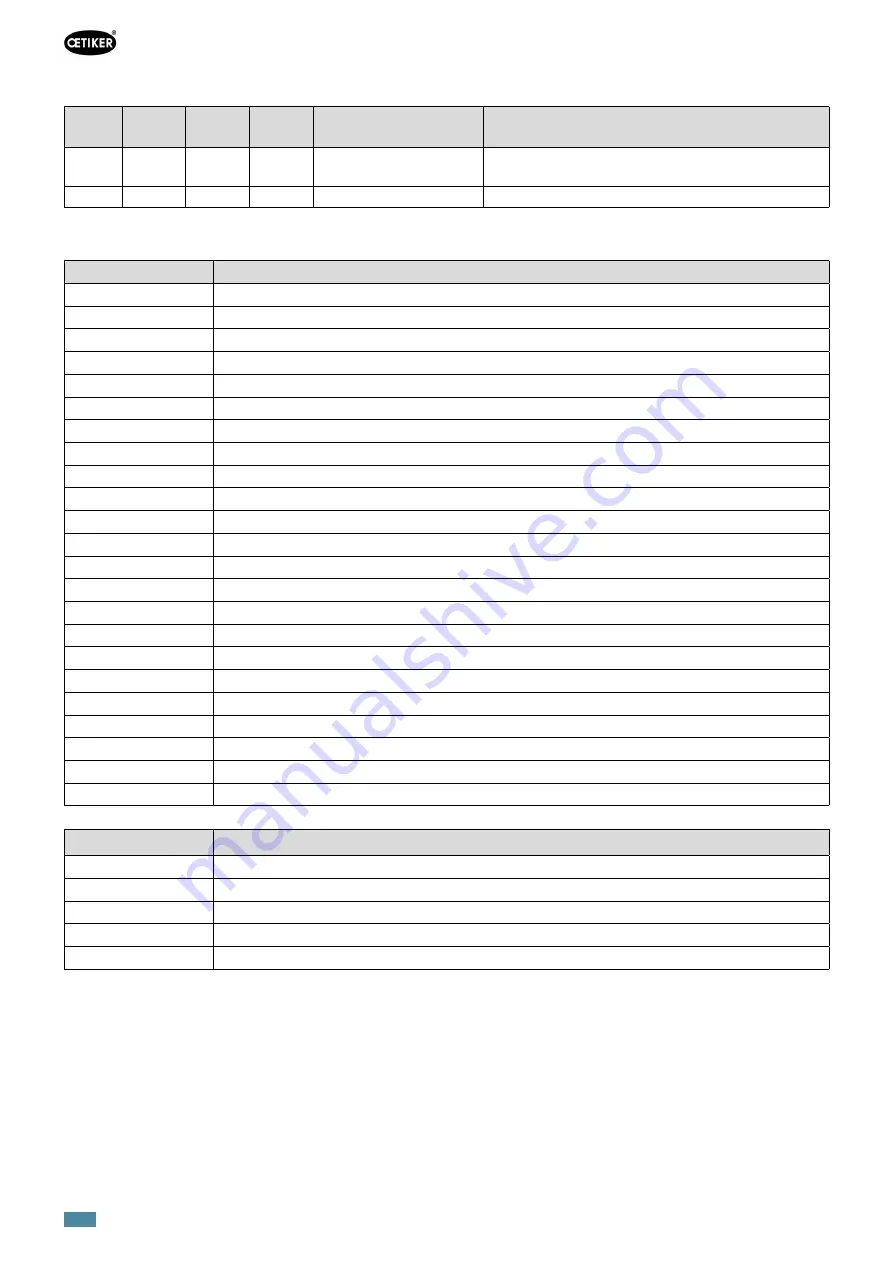
94
OETIKER EPC 01
aPPenDIX
Issue 11.22
08905306
Offset Length
[Byte]
Bit
Offset
Type
Data
Description
112
2
Int
Verification result
Result of the verification work step. oK = 0, not
oK = error number.
114
4
---
n/a
Codes Definitions
Code
Description
0
aPn Menu
10
In function menu. Pincer test can be started
11
in function menu. Pincer test must be started
40
friction test ready for triggering
41
friction test running
60
simple force Test: Ready to triggering
61
simple force Test: Test running
62
simple force Test: Ready to retriggering
70
Two stage guided force test lower force: Ready to triggering
71
Two stage guided force test lower force: Test running
72
Two stage guided force test lower force: Ready to retriggering
86
Two stage guided force test higher force: Ready to triggering
57
Two stage guided force test higher force: Test running
88
Two stage guided force test higher force: Ready to retriggering
96
Gap test smaller gap and lower force ready to triggering
97
Gap test smaller gap and lower force running
98
Gap test smaller gap and higher force ready for triggering
99
Gap test smaller gap and higher force running
100
Gap test higher gap and lower force ready for triggering
101
Gap test higher gap and lower force running
102
Gap test higher gap and higher force ready for triggering
103
Gap test higher gap and higher force running
104
end of pincer test
Code
Description
0
Pincer jaw fully open
10
open gap achieved
20
Hold function completed
30
Closure function completed
40
Verification function completed