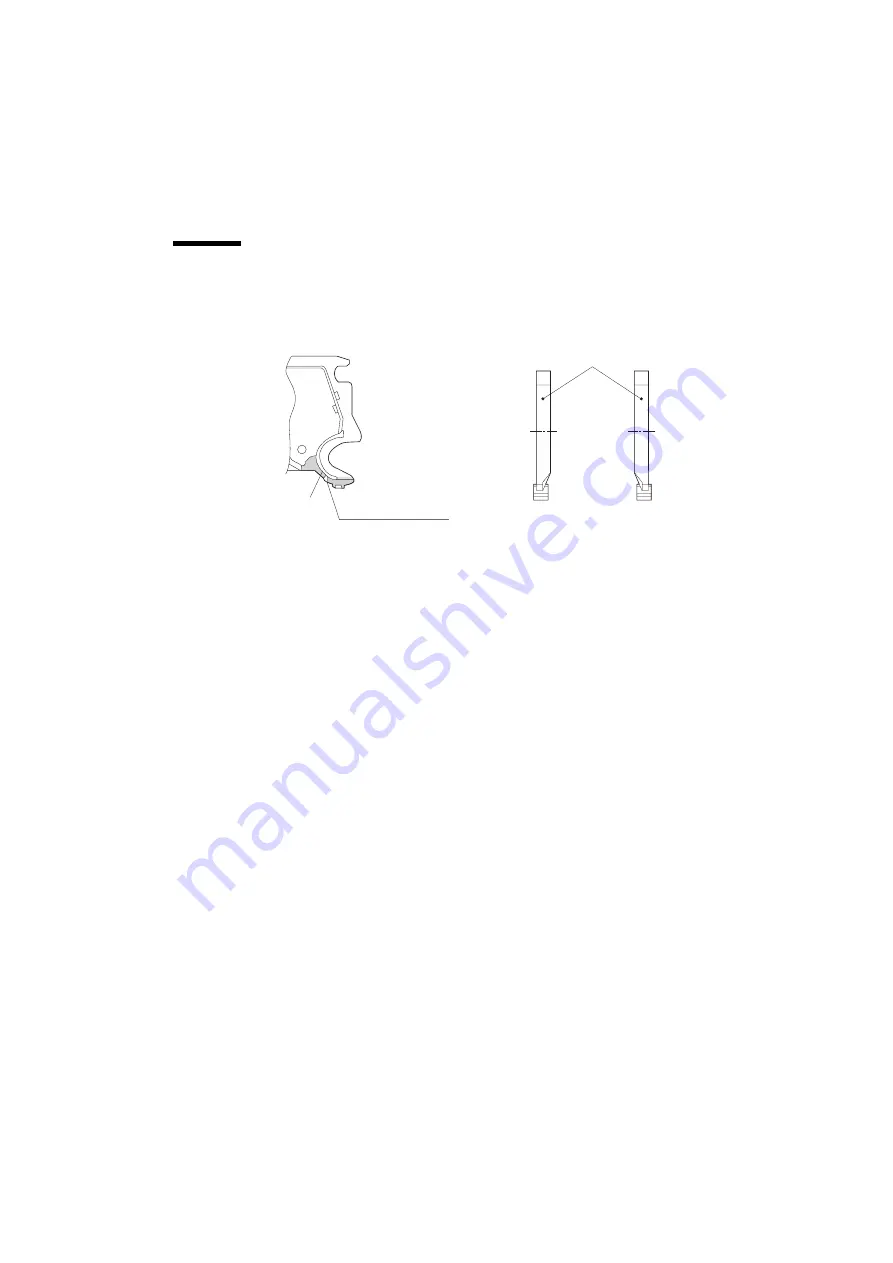
404
TSM Océ 3121
Dis-/assembly
4 The position of the magnetic seal in the developing unit
When fitting the magnetic seal, hold it firmly against the opening. Ensure that
the magnetic seal and the housing are in firm contact.
Magnetic seal
Opening
(reference for butting)
Magnetic seal
(rear)
(front)
Magnetic seal
Opening (reference for
butting)
Magnetic seal
(Rear)
(Front)
Summary of Contents for 3121
Page 1: ...Technical Service Manual Oc 3121 3122 Oc Oc Oc Oc 3121 3122...
Page 6: ...Technical Service Manual Oc 3121 3122 Oc Oc Oc Oc INSTALLATION...
Page 72: ...Technical Service Manual Oc 3121 3122 Oc Oc Oc Oc IMAGE QUALITY...
Page 76: ...Confidential 1998 Oc Technologies B V ed 1 Image quality 3 2 Image adjustment basic procedure...
Page 93: ...20 TSM Oc 3121 Image quality Isolating a PBA printer image fault...
Page 94: ...Confidential 1998 Oc Technologies B V ed 1 Image quality 21 5 Isolating a PBA FAX image fault...
Page 105: ...Technical Service Manual Oc 3121 3122 Oc Oc Oc Oc TROUBLE SHOOTING...
Page 188: ...Technical Service Manual Oc 3121 3122 Oc Oc Oc Oc GENERAL...
Page 201: ...Technical Service Manual Oc 3121 3122 Oc Oc Oc Oc 01 PHOTOCONDUCTOR...
Page 205: ...Technical Service Manual Oc 3121 3122 Oc Oc Oc Oc 02 CHARGING...
Page 210: ...Technical Service Manual Oc 3121 3122 Oc Oc Oc Oc 04 EXPOSURE...
Page 239: ...Technical Service Manual Oc 3121 3122 Oc Oc Oc Oc 05 DEVELOPING...
Page 242: ...302 TSM Oc 3121 Adjustments...
Page 251: ...Technical Service Manual Oc 3121 3122 Oc Oc Oc Oc 06 TRANSFER...
Page 260: ...Technical Service Manual Oc 3121 3122 Oc Oc Oc Oc 07 CLEANING...
Page 263: ...Technical Service Manual Oc 3121 3122 Oc Oc Oc Oc 08 IMAGE PROCESSING...
Page 299: ...Technical Service Manual Oc 3121 3122 Oc Oc Oc Oc 10 RDF...
Page 392: ...Confidential 1998 Oc Technologies B V ed 1 10 RDF 511 2 Inputs to the RDF Control PBA...
Page 427: ...546 TSM Oc 3121 Functional description e Sequence of operations page composition fax mode...
Page 433: ...552 TSM Oc 3121 Functional description Sequence of Operations small sizes return...
Page 450: ...Confidential 1998 Oc Technologies B V ed 1 10 RDF 701 Electrical diagrams...
Page 451: ...Technical Service Manual Oc 3121 3122 Oc Oc Oc Oc 11 DIGITAL DOCUMENT HANDLING...
Page 462: ...510 TSM Oc 3121 Functional description Inputs to and Outputs from the FAX Board...
Page 465: ...Confidential 1998 Oc Technologies B V ed 1 11 Digital document handling 513...
Page 468: ...516 TSM Oc 3121 Functional description CORE IP Board...
Page 469: ...Technical Service Manual Oc 3121 3122 Oc Oc Oc Oc 12 PAPER...
Page 509: ...Technical Service Manual Oc 3121 3122 Oc Oc Oc Oc 13 SPECIALITY INPUT...
Page 519: ...Technical Service Manual Oc 3121 3122 Oc Oc Oc Oc 16 DUPLEX...
Page 537: ...Technical Service Manual Oc 3121 3122 Oc Oc Oc Oc 17 FIXING...
Page 542: ...402 TSM Oc 3121 Dis assembly 8 Remove the two screws 7 Take out the fuser drive 6...
Page 569: ...512 TSM Oc 3121 Functional description Brush Hinge arm...
Page 570: ...Technical Service Manual Oc 3121 3122 Oc Oc Oc Oc 19 DELIVERY...
Page 606: ...Confidential 1998 Oc Technologies B V ed 1 19 DELIVERY 701 Electrical diagrams...
Page 607: ...Technical Service Manual Oc 3121 3122 Oc Oc Oc Oc 21 SORTER...
Page 721: ...Confidential 1998 Oc Technologies B V ed 1 21 SORTER 701 Electrical diagrams...
Page 722: ...Technical Service Manual Oc 3121 3122 Oc Oc Oc Oc 22 POWER CONTROL...
Page 734: ...508 TSM Oc 3121 Functional description Image processor PBA 3 3 inputs and outputs...
Page 735: ...Confidential 1998 Oc Technologies B V ed 1 22 Power Control 509 DC Control PBA 1 3 inputs...
Page 736: ...510 TSM Oc 3121 Functional description DC Control PBA 2 3 inputs...
Page 737: ...Confidential 1998 Oc Technologies B V ed 1 22 Power Control 511 DC Control PBA 3 3 inputs...
Page 740: ...514 TSM Oc 3121 Functional description DC control PBA 3 3 outputs...
Page 769: ...Confidential 1998 Oc Technologies B V ed 1 22 POWER CONTROL 1 701 Electrical diagrams...
Page 770: ...Confidential 1998 Oc Technologies B V ed 1 22 POWER CONTROL 2 702...
Page 771: ...Confidential 1998 Oc Technologies B V ed 1 22 POWER CONTROL 3 703...
Page 772: ...Confidential 1998 Oc Technologies B V ed 1 22 POWER CONTROL 4 704...
Page 773: ...Technical Service Manual Oc 3121 3122 Oc Oc Oc Oc 23 DRIVE...
Page 778: ...Technical Service Manual Oc 3121 3122 Oc Oc Oc Oc MISCELLANEOUS...
Page 785: ...Technical Service Manual Oc 3121 3122 Oc Oc Oc Oc PREVENTIVE MAINTENANCE...
Page 793: ...Technical Service Manual Oc 3121 3122 Oc Oc Oc Oc TECHNICAL DATA...
Page 809: ...Technical Service Manual Oc 3121 3122 Oc Oc Oc Oc SDS DESCRIPTION...