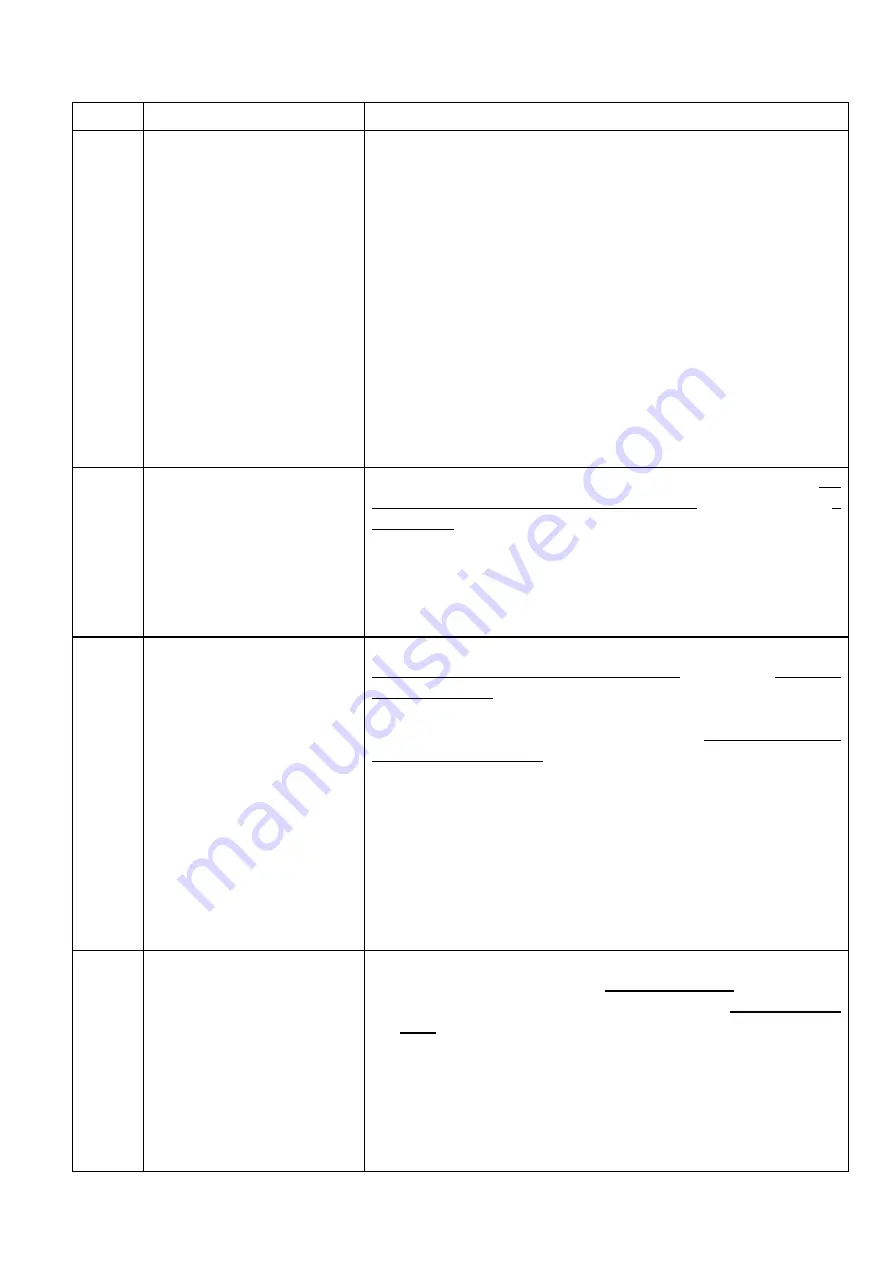
39
Display Name
Content
J02
Selection of driving method
Initial value: 1
The input condition of the driving ON/OFF signal is switched.
External control terminal: X1 terminal
Overflow detection sensor input: IN1 terminal
0: Driving by AND with the external control terminal signal and the overflow
detection sensor (Both conditions must be on the driving sides).(X1 open:
Driving)
1: Driving by AND with the reversed logic of the external control terminal signal
and the overflow detection sensor (Both conditions must be on the driving
sides).(X1 open: Stopping)
2: Driving/stopping by RUN/STOP keys of the operation panel
3: Driving by AND with the operation panel RUN/STOP keys and the overflow
detection sensor.
Even during panel locking, the RUN/STOP key is effective when the panel control
has been selected.
It is not possible to get the ON/OFF delay timer to work with the external control
terminal signal.
J03
Selection of JOG driving
Initial value: 0
Even when the driving is stopping by the external control (J02 is 0 or 1), it is
possible to drive compulsorily only while the RUN button of the operation panel is
being pressed. Please use it at the initial supply of the work or discharging or at
the time of adjustment. The JOG lamp (green) on the side of the RUN button
lights when JOG drive can be done.
0
:
JOG driving function is not used
1
:
JOG (compulsory single) driving function is used.
Even if a knob lock or the operation lock is set, the JOG driving is effective.
J04
Setting of F-V curve
Initial value:H
Unchangeable during driving
The F/V curve is set according to the main body used.
Data can be changed only while driving is stopping. Please surely confirm the
setting before driving. When the setting is mistaken, the accident such as burning
of the magnet will occur.
As the data setting changes with the main body used, set it to an appropriate
value with surely reading P.47, when you change the data of the F/V curve.
F: Selection of curves of full wave system such as N25
H: Selection of curves of half wave system such as N40(Initial value)
P:
Exclusive for G63 and interchangeable curve with ECB96
C: Selection of curves of high frequency system such as HF10
0
~
17: Specifying directly of curve
№
*
When you use
№
0-17, please examine the characteristic of the load current
and set it after investigations not so as to get overloaded.
*
When a special specification such as S20, N25-1 is driven by half wave, please
select also the full wave for the F/V curb.
J05 Selection
of
feed-
back mode
Initial value: 0
Unchangeable during driving.
Feedback data at the time of driving is selected.
0: Output voltage becomes to a stable constant voltage mode.
1: Amplitude of vibration main body becomes to a stable constant amplitude
mode.
2: Impossible of choice
3: Gain data used by the constant amplitude control is automatically set. After
setting data, it automatically becomes to the constant amplitude mode.
*
Unusable for even applicable main bodies using inapplicable bowls or modified
main bodies. Moreover, it may be unusable also if number of leaf springs was
changed.