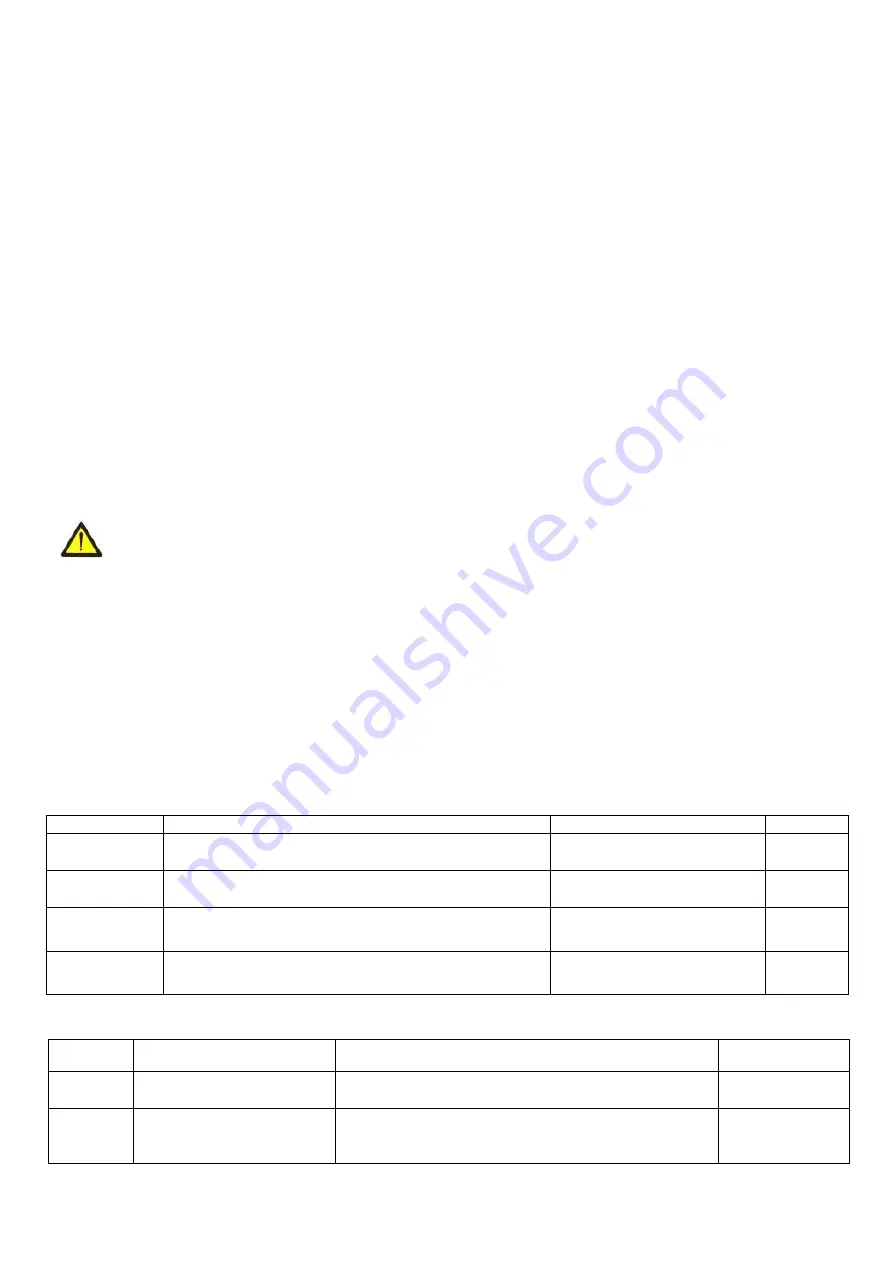
~
8
~
ЕТ-485
NOVATEK-ELECTRO
In the remote server redirection mode, if connection to the client-specified Modbus TCP server in Ethernet
network has been established, queries to other devices are also sent to this server and an answer from it is
awaited.
N o te
– The answer is received from the first answering addressee, therefore there must be no devices
with same Modbus addresses (identifiers) in Modbus network and among the addressees, available through
the remote server.
If a query failed to be redirected (e.g. in the RS-485 slave mode, if connection to the remote server was broken),
ET-485 can generate and transfer the client-specified Modbus exception code (default
– code 10) to the client.
If there is no answer, ET-485 can generate and transfer the client-specified Modbus exception code (default
–
code 11) to the client.
If the answer to the query has been received,
ЕТ-485 transfers it to the client, which sent the query.
In case of any format errors, an “Error” indicator shall become activated for 0.5 seconds and no response is
provided to the client.
6.4 THE OPERATION OF ET-485 IN THE MODE OF ACTIVE CONNECTION TO THE CLIENT
In this mode in addition to providing other connections
ET-485 autonomously establishes and further maintains
active connection to the client (data collection remote server) with a set host name or IP address.
ET-485 receives Modbus TCP queries from this client and returns responses. The mode allows one user to work with
one or more ET-485 units via the Internet without static address assignment to each unit (see appendix B).
7 SETTING
7.1 GE N E R A L IN F ORMA T ION
Configurable parameters are described in section 7.2. All parameters are saved at the power off.
Unit configuration can be done in two ways:
through WEB-interface, see Section 7.3;
through Modbus-interface, see Section 7.4;
WARNING! ANY CHANGES IN UNIT CONFIGURATION MAY RESULT IN BLOCKING OR
OBSTRUCTION WHILE TRYING TO REACH THE UNIT OVER THE NETWORK.
In this case, all parameters should be factory reset (see Section 3.2).
7.2 P A R A ME T E R S OF
ЕТ-485
A collection of parameters available via Modbus protocol is provided in Table 3. The inner structure of any
collection of parameters is similar to the structure of collection, which is described in table 7 (apart from start-address).
The presentation format of parameters in Modbus registers is detailed in Table 4.
The unit describing parameters are given in Table 5.
The unit current mode parameters are available for reading and recording and specified in Table 6.
All parameters to determine the current condition of the unit (available for read-only) are provided in Table 7.
All parameters available in the configuration mode only are provided in Table 8.
ACC identification state parameters (table 9) are available for ACC and in a parameter mode.
ACC identification control parameters are available only for ACC and are described in table 10.
Table 3
– Collection of parameters available via Modbus protocol
Collection
Description
Access
Address
Acting settings Current unit configuration
In any mode,
read-only
200
–298,
1200
–1241
Saved settings The collection is saved regardless of power supply
and further used as the restart.
In configuration mode only,
read-only
300
–398,
1300
–1341
Factory
settings
Fixed collection, which can be activated as shown in
sections 7.3 and 7.4
In configuration mode only,
read-only
400
–498,
1400
–1441
Changeable
settings
All parameters listed in table 8, which can be modi-fied
and incorporated as described in Section 7.4
In configuration mode only,
reading and writing
500
–598,
1500
–1541
Table 4
– Presentation format of parameters in Modbus registers
Parameter
Range of values
Description
Number of
Registers
Number 0-65535
Integer (16 bits) in a standard range of Modbus
register
1
Number
0-4294967295 in two
registers,
upper part
– first
Integer number, which can not exceed the limit for
Modbus register (65535)
2