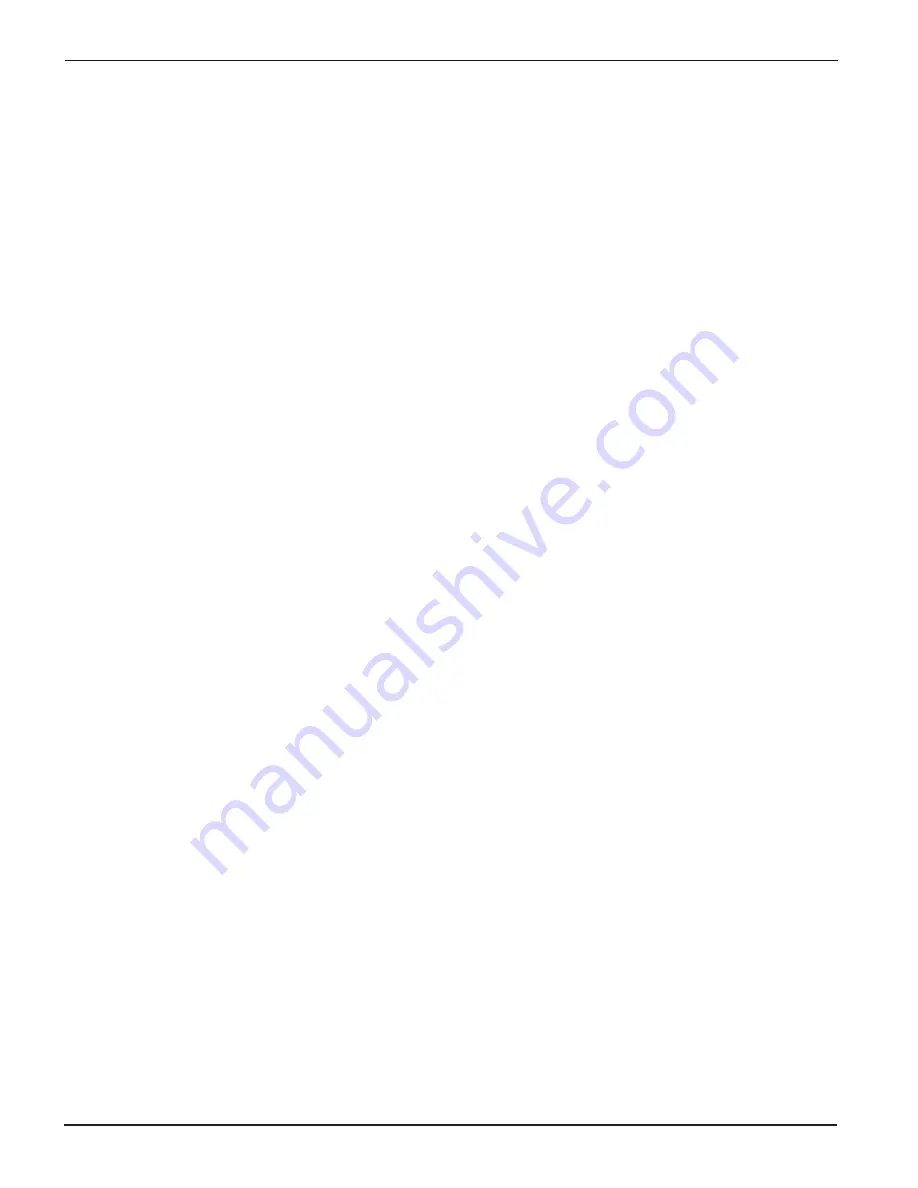
12
IMS-MN-LMDA42C_A.pdf
About this Product
LMD CANopen
About this Product
This manual is valid for NEMA 17 (42mm) LMD CANopen devices with M12 circular connectors.
This chapter lists the type code for this product. The type code can be used to identify whether
the product is a standard product or a customized model.
Unit Overview
The “LMD CANopen” consists of a stepper motor and integrated electronics. The product
integrates interfaces, drive and control electronics, and the power stage. There are three basic
control variants:
•
Closed Loop with hMT
: loop is closed by a 1000-line (4000 edge) magnetic encoder. May be
operated as:
–
hMT off
: standard encoder functions for position and stall monitoring.
–
hMT on
: enhanced closed loop functions such as anti-stall and position make-up.
•
Absolute with hMT
: Closed loop with multi-turn absolute encoder, which will retain position
information for a limited time upon loss/removal of power. The standard encoder and hMT
features will function as on a closed loop model. See Appendix D for details.
•
Open Loop
: open loop stepper control.
Operating Modes
The “LMD CANopen” uses DS301 communication profile as the interface between device
profiles and CAN bus. It was specified in 1995 under the name DS301 and defines uniform
standards for common data exchange between different device types under CANopen.
The DSP402 device profile describes standardized objects for positioning, monitoring and
settings of drives.
•
Profile position
: defines the positioning of the drive. Speed, position, and acceleration can be
limited. Profiled moves using a trajectory generator are also possible.
•
Homing mode
: describes the various methods to find a home position, reference point, date,
or zero point on start up, or via an immediate mode command.
•
Profile Velocity
: used to control velocity of the drive with no special regard of the position.
It supplies limit functions and trajectory generation.
•
Profile Torque
: defines the torque control with all related parameters. (Available on closed
loop models only.)
•
Cyclic Synchronous Position
: used to define position control where the device, or multiple
devices, initiate and complete a point to point move at a specified time.