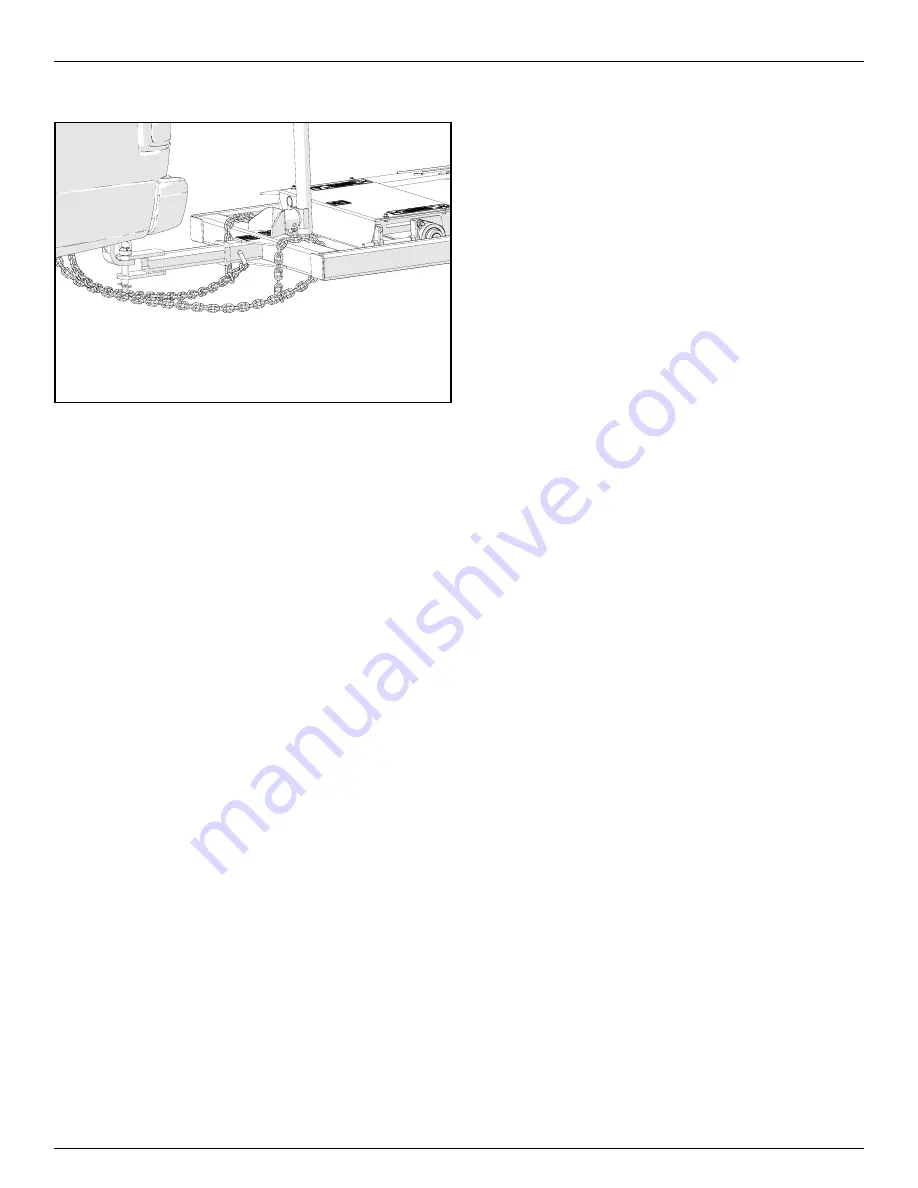
3 - TRANSPORT OPERATIONS
3-11
15. Secure the safety chains around the Kwik-Pit drawbar
cage to prevent unexpected separation.
Fig. # 3-24 Secure the Safety Chains Around the Kwik-Pit
Drawbar Cage
14. Attach other end(s) of safety chain(s) to towing vehicle.
(See"Use a Safety Chain" on page 2-12)
15. Tow the unit to the next location.
Detaching Kwik-Pit From The Towing Vehicle
1. Follow the steps in reverse order defined in
Summary of Contents for Kwik-Pit 26 Series
Page 2: ......
Page 10: ...1 4 1 GENERAL INFORMATION This Page Is Intentionally Left Blank...
Page 46: ...2 SAFETY INFORMATION 2 36 This Page Is Intentionally Left Blank...
Page 58: ...3 TRANSPORT OPERATIONS 3 12 This Page Is Intentionally Left Blank...
Page 116: ...5 MAINTENANCE 5 38...
Page 118: ...5 MAINTENANCE 5 40 This Page Is Intentionally Left Blank...
Page 120: ...6 TROUBLESHOOTING 6 2 This Page Is Intentionally Left Blank...
Page 126: ...8 FORMS AND DECLARATIONS 8 2 This Page Is Intentionally Left Blank...
Page 132: ......