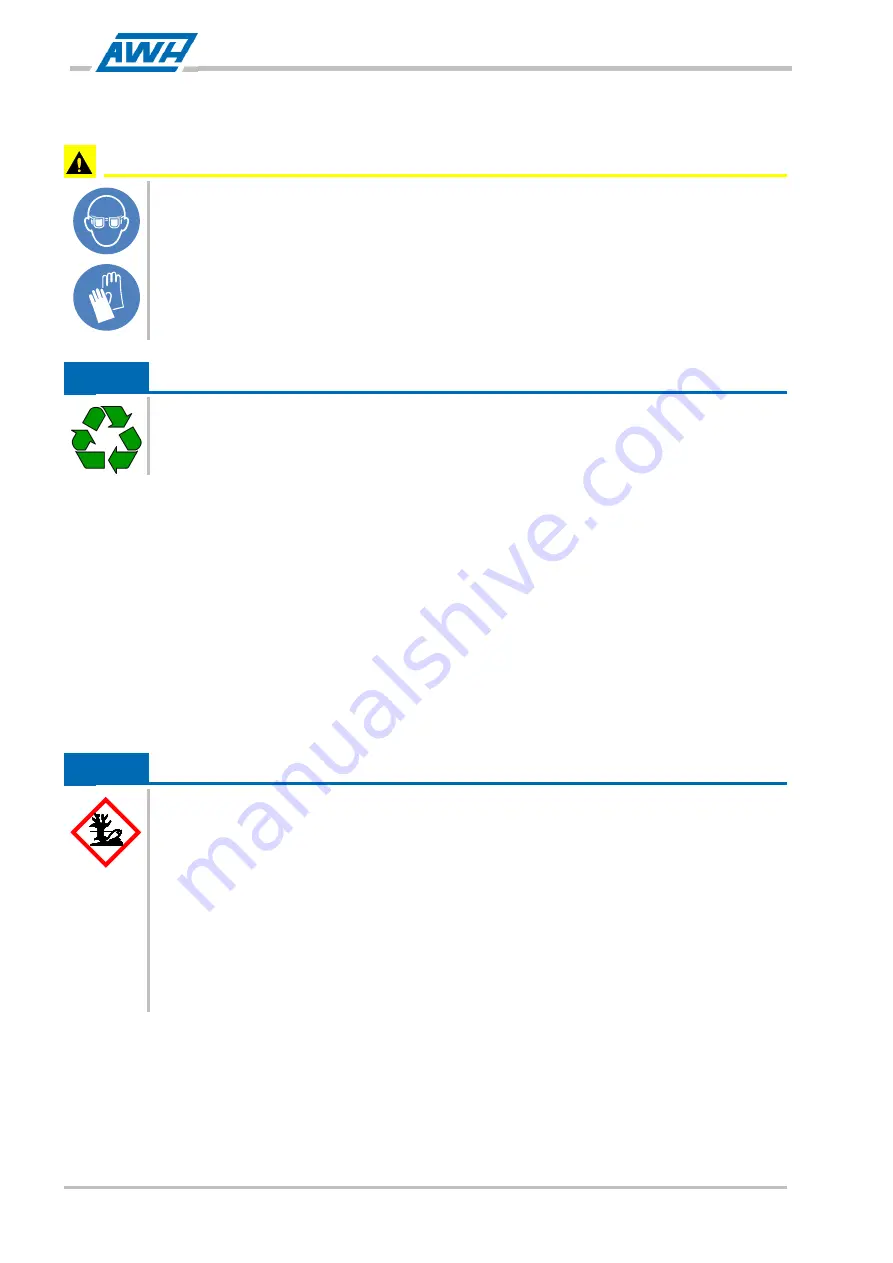
Container Cleaning System TANKO®EX-R64T
74/80
Translation - Operating/installation instructions 2020/03
9 Putting the Device out of
Service
9.1
Disposal
CAUTION
Risk of injuries from harmful fluids!
During disposal, there is a risk of injury from contact with harmful fluids.
There is a risk of minor or moderate injuries.
Wear personal protective equipment (e.g. protective gloves, safety shoes, safety goggles).
NOTE
The cleaning device is primarily made of stainless steel. Stainless steel is a valuable raw
material and can easily be recycled.
After removal, for the correct disposal of the complete device
–
Clean it (see
Section 7.4.3 Notes on Cleaning
) and
–
Disassemble it into assembly groups and individual parts.
Unless other arrangements have been made for return or disposal, disassembled components should
be recycled:
–
Scrap any parts made of metal
–
Recycle any parts made of plastic
If necessary, contact a specialist company to arrange for disposal.
Comply with the locally applicable health, safety, disposal and environmental protection regulations.
NOTE
Risk of environmental damage as a result of improper disposal!
Cleaning agents, consumables and lubricants must NOT be allowed to get into the
groundwater, waterways or sewer system.
There is a risk of environmental damage.
Dispose of any cleaning agents, lubricants and consumables (e.g. brushes and cloths)
that were used for cleaning in accordance with the local regulations and in
accordance with the information in the manufacturer's safety data sheets.
Dispose of packaging materials in an environmentally friendly manner and have them
recycled.