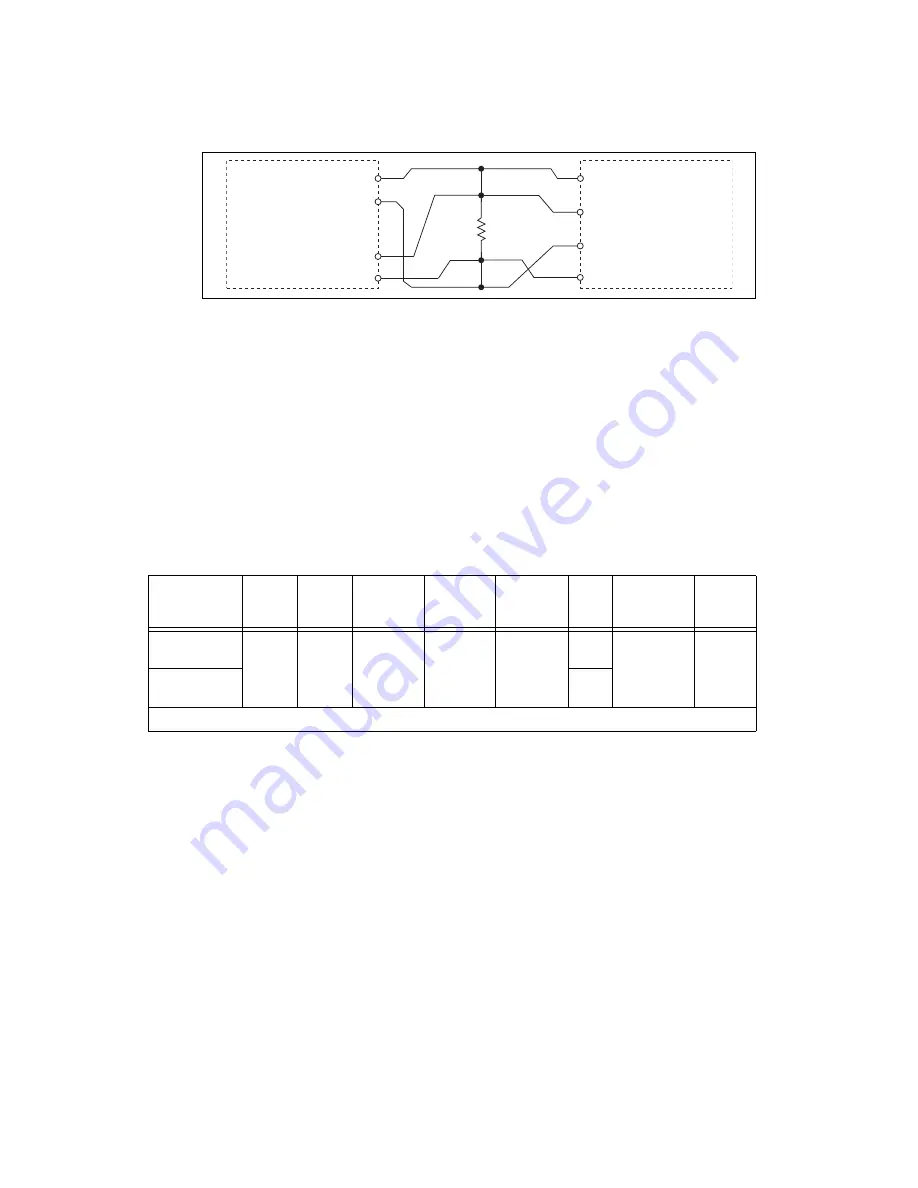
NI 9219 Calibration Procedure
16
ni.com
Figure 8.
4-Wire RTD Accuracy Verification Connections to the NI 9219
2.
Create an AI voltage channel in the 1 V range on the NI 9219.
3.
Commit the task to place the NI 9219 in voltage mode. This prevents the module from interfering
with the resistance measurements of the DMM.
4.
Configure the DMM for a 4-wire resistance measurement in the appropriate range according to the
test point from Table 17.
5.
Enable Auto Zero on the DMM.
6.
Acquire a resistance reading with the DMM. Record this measurement as
ref
.
7.
Disconnect the DMM from the resistor to ensure that the terminals on the DMM do not interfere
with the resistor while the NI 9219 makes measurements.
8.
Clear the task.
9.
Create an AI RTD channel on the NI 9219. Configure the channel according to Table 16.
10. Acquire 20 unscaled I32 4-wire readings with the NI 9219. Record the average of the readings as
data
unscaled
.
11. Scale the data by using the formula below to change the unscaled data into
.
where
range
max
is the maximum value for the selected range in Table 17.
12. Perform the following calculation using the recorded
ref
and
channel
values.
Table 16.
NI 9219 Configuration for 4-Wire RTD Accuracy Verification
Measurement
Type
Min
(°C)
Max
(°C)
Excitation
Source
Excitation
Value
Resistance
Config
r0
*
ADC
Timing
Mode
Sample
Timing
Type
4-Wire RTD
Pt1000
0
800
Internal
0.0005
4-Wire
1000
High
Resolution
On
Demand
4-Wire RTD
Pt100
100
*
RTD nominal resistance at 0 °C.
R
TestPoint
Ω
HI
LO
NI 9219
DMM
Ω
SENSE
HI
LO
EX+ (3)
HI (4)
EX– (5)
LO (6)
Ch
x
channel
data
unscaled
2
24
-----------------------------
range
max
=
Accuracy
channel
ref
–
=