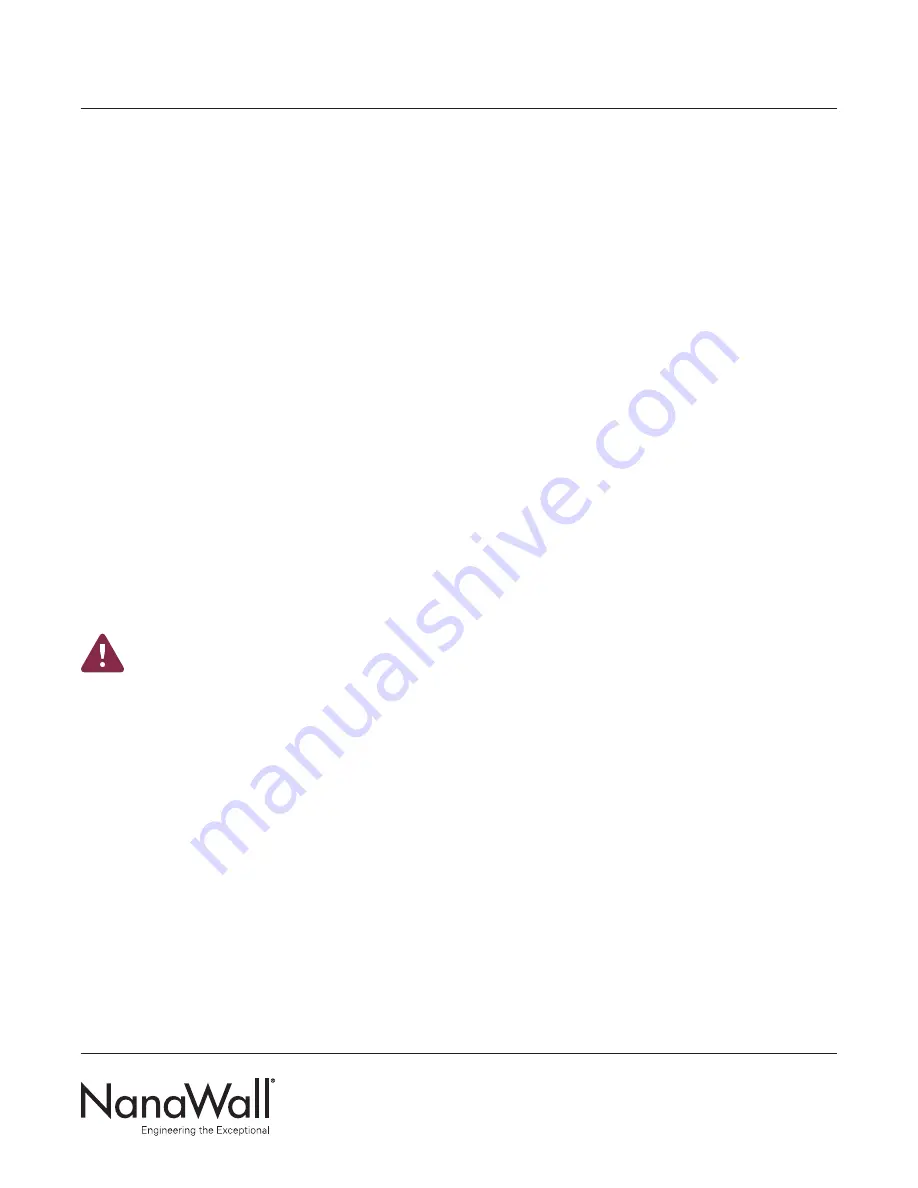
NANAWALL HSW75 OWNER’S MANUAL
6
Sheet 11. Centered Pivot Point and Bottom Door
Closer Installation
Sheet 12. Pivot Point Top Track for Single/Double Action
End Panel
Sheet 13. Single/Double Action End Panel Installation
Sheet 14. Offset Pivot Point and Floor Closer Installation
Sheet 15. Offset Pivot Point Top Track for Single Action
End Panel
Sheet 16. Installation of Profile Cylinder
Sheet 17. Height Adjustment of Top Brush
A. FRAME ASSEMBLY AND INSTALLATION
Since there can be an infinite number of variations of
stacking options and configurations, it is not possible to
have step by step specific instructions that will apply to all
units installed. Below are general instructions that focus
on the installation of a 5 panel unit as shown in
Diagram 1
.
This may not exactly apply to your particular unit.
Please refer to the Custom Product Drawings for your
specific project.
The key to having a properly installed and
operating HSW75 system is to install a perfectly
level upper track at the correct height from
the level finish floor, then after the panels are
installed, placing sockets in the floor such that
they are precisely aligned to the panel locking.
Step A1
Look for the labels on the different upper track
segments and set them on the floor as per the layout
of the head track.
Step A2
Attach as many of the upper track pieces together that
could be supported and installed easily as one piece.
Use the connectors and set screws provided.
See Sheet 4 of the Installation Manual.
Make sure that
the correct angles between segments are maintained
and that the transitions between the track segments are
perfectly aligned and smooth.
Step A3
The roller access head track section is a removable
section in the head track (RHT). This section will need to
be later removed when the panels are installed.
Step A4
The head track is pre-drilled in the factory with anchorage
holes at spacing’s of about 10
"
(250 mm) for 5/16
"
(8 mm)
diameter screws or bolts.
See Sheet 3 of the Installation
Manual.
The correct fastener spacing in the support structure
within the opening depends on substrate material, design
windload pressures (if exterior) of project, panel height
and other requirements of the project.
All anchoring
details and requirements should be determined and
verified by the project structural engineer
. Please pre-
drill any additional anchorage holes as needed.
The spacing of anchorage devices in the stacking bay
should be every 4
"
and in the stacking route every about
10
"
(250 mm). Please pre-drill any additional anchorage
holes as needed.
Use appropriate anchorage devices depending on the
project lateral load requirements and adjacent substrate
material and construction. If the factory pre-drilled holes
are sufficient, then 8 mm (5/16
"
) diameter screws can be
used. Make sure they are corrosion resistant and that the
screw head is small enough to fit inside the slot in the
middle of the head track, otherwise it will interfere with
the running carriages. Anchorage devices should
penetrate (embedment) or hold sufficiently to the
opening to withstand necessary lateral loading.