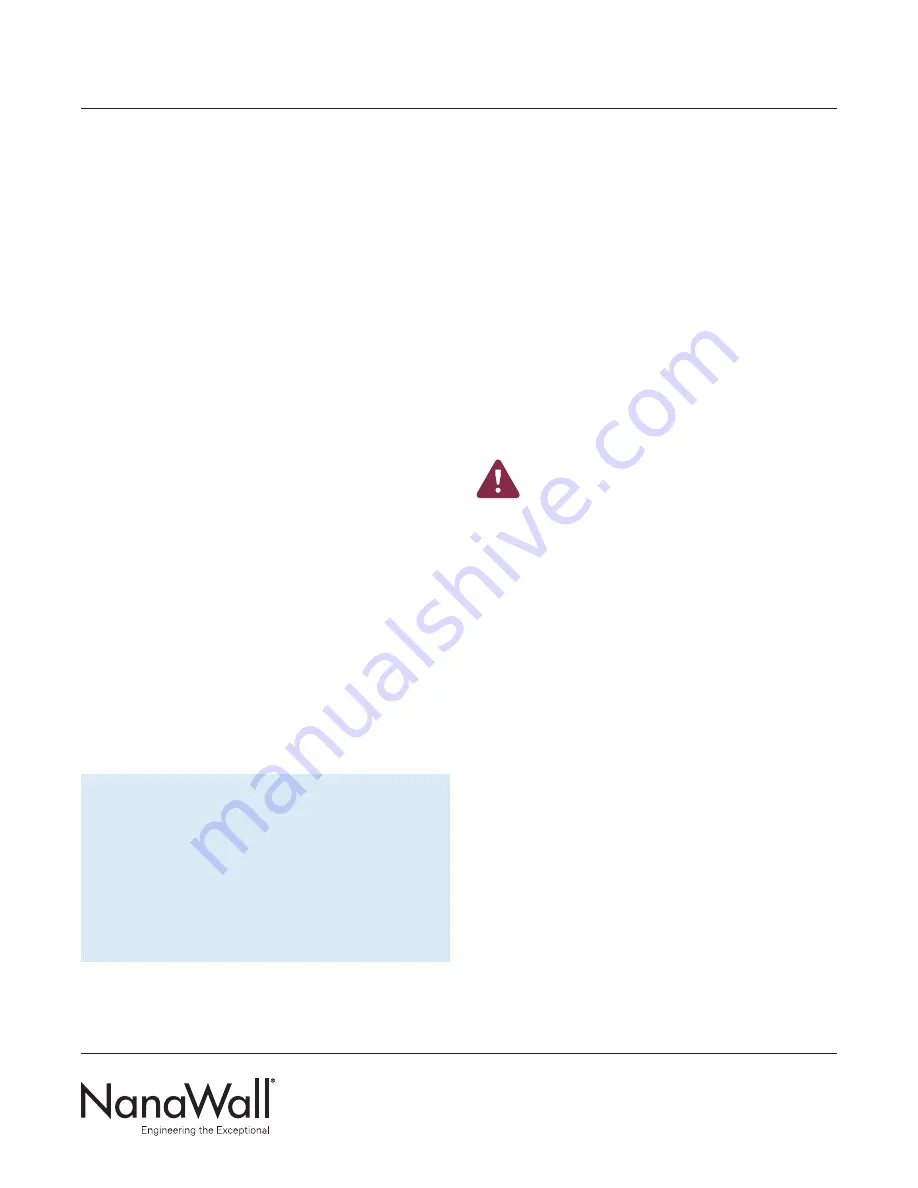
NANAWALL HSW75 OWNER’S MANUAL
7
Attention should also be made to the minimum edge
distance that must be maintained for different substrates.
Generally, for wood frame, minimum embedment is 2 1/2
"
and minimum edge distance is 3/4
"
, for concrete
minimum embedment is 1 1/4
"
min. and minimum edge
distance is 2
"
.
Step A5
For all anchorage options, set the assembled part of the
upper track into the rough opening at the proper position
relative to the support structure and the finish floor.
Step A6
Support the upper track
temporarily in a safe manner
.
Step A7
Place hard plastic horseshoe shims tightly at every fixing
point between the upper track and the header. Anchor
the head track with appropriate screws through the pre
-
drilled holes or as needed.
See Sheet 5 of the Installation
Manual.
Step A8
Assemble and install other segments of the upper track
in a similar manner. Make certain that the angles between
different upper track components are exact. If the
stacking bay has parallel legs, make sure that the legs are
exactly parallel.
IMPORTANT:
ADJUST EACH ANCHORAGE
POINT AS NEEDED TO MAKE THE UPPER TRACK
ABSOLUTELY LEVEL AND PLUMB. USE A TRANSIT/
LASER AND OTHER SIMILAR PRECISE MEASURING
EQUIPMENT TO MAKE THESE DETERMINATIONS.
MAKE SURE NO SHIMS ARE FORCED TO ENSURE
THAT THE UPPER TRACK IS NOT BOWED.
Upper track segments must be joined such that
they are even, tight
,
and aligned perfectly.
Otherwise, the
running carriages may wear out
prematurely, which will then not be covered by
warranty. Placing shims at the meeting points of track
segments may help in keeping the segments even,
even though there may not be anchorage holes at this
point. See Sheet 5 of the Installation Manual.
Make sure that all surfaces of the upper track
are clean and free of any debris, especially cuttings
from drilled holes.
Do not attach anything from the side against
the head track.
Do not drill any holes for sockets, pivot points,
and floor closers, yet!
B. PANEL INSTALLATION FOR ALL
SLIDING PANELS
As there can be many possible configurations, panel
installation will vary with each unit. Below are guidelines
for a 5 panel unit shown in Diagram 1. Determine the
interior/exterior side of the panels and install them such
that they are facing the correct direction. Please also refer
to
E. PANEL INSTALLATION OF A SINGLE/DOUBLE
ACTION END PANEL (NON-SLIDING)
after following
the instructions in
C
and
D
.
Step B1
Check all the carriers on all the folding panels.
Make sure
all the locking nuts are securely tight.
Do not make any
adjustments on the carriers, yet.
Step B2
Before inserting the panels, add stoppers at the very ends
of the top track to prevent panels from coming off the
track.
See Sheet 8 of the Installation Manual.