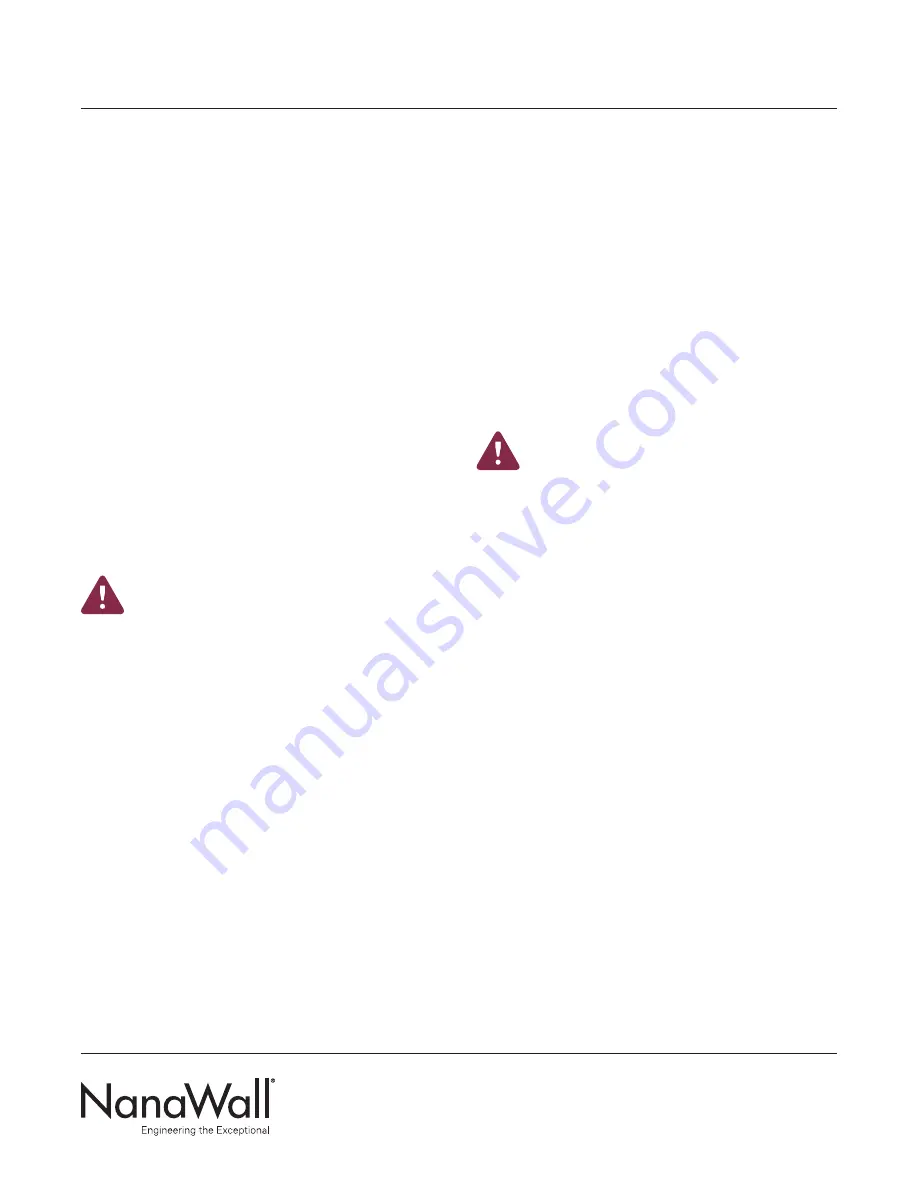
NANAWALL HSW75 OWNER’S MANUAL
9
To adjust the height of the panels, remove the end cap
on the side of the carrier of the top rail and loosen the set
screw holding the carriage bolt and the nut using a 22 mm
open jaw wrench. Clamp on the flat part of the bolt that is
located near the bottom of the roller with the 11 mm open
jaw wrench and adjust the height. Counter-clockwise
rotation = less floor clearance; clockwise rotation = more
floor clearance.
After final adjustments make sure to
really tighten down the nut first and then the set screw
to secure the bolt/axle from turning.
After you adjusted all sliding panels, measure the width
for the single action end panel (non-sliding) again and
make sure it fits into the opening. If necessary use the
stopper in the top track to adjust the dimension. The
stopper on the inside of the top track at the end of the
plain of the opening should be touching the running
carriage and is used as a reference point on that side for
the overall width of the unit.
Now you can start drilling holes for sockets and
pivot boxes! Do not install the single/double
action end panel (non-sliding), yet!
D.
SOCKETS AND PIVOT BOX
Holes and slots in the floor for the sockets and pivot
boxes have to be made at exact precise spots. There is no
second chance if the hole/slot location is off.
See Sheet 9
and 10 of the Installation Manual.
With a laser, find the center line of the head track on the
floor along the length of the opening, and mark it with a
chalk line. Close the unit such that the panels are in the
correct closed positions by offsetting them to one another
so that any side protruding locking mechanism is not in
the way. Make sure the panels are straight and the correct
4 mm gap between panels is maintained.
Start with the
panel furthest away from the parking bay
and add blue
masking tape underneath the approximate location of
the locking bolts. Slowly and carefully engage the locking
points until it touches the tape. The tip of the locking
bolts should make a mark on the blue tape that would be
the center point of the socket hole.
From the custom product drawings and the locking type
on the panels, drill the appropriate size socket holes. If
concrete, use a diamond core drill bit with the proper
diameter size. Also for the pivot box chisel out the
appropriate space needed.
Slide the proper sockets and pivot boxes into the holes. If
necessary, use suitable material to fix them in place.
Now you can start drilling holes for sockets,
pivot points and floor closers for the single/
double action end panel (non-sliding)!
E.
PANEL INSTALLATION FOR SINGLE/
DOUBLE ACTION END PANELS (NON-SLIDING)
CENTERED AND OFFSET INCLUDING PIVOT
POINT AND FLOOR CLOSER INSTALLATION
Holes and slots in the floor for the pivot points and floor
closers have to be made at exact precise spots. There is
no second chance if the hole/slot location is off.
See Sheet
11-15 of the Installation Manual.
Step E1
Start at the bottom and use the chalk line as a reference
line. Measure the overall width of the panel and compare it
with the dimension on the custom product drawing. To
this dimension add 3/16
"
(4 mm) at each end to make sure
the correct 3/16
"
(4 mm) gap between the panels and
between the panel to the wall is maintained. Then the
panel has to fit in the remaining opening.
Step E2
For the center pivot end panel (non-sliding) with pivot
point, the dimension for the center of the pivot axle to the
adjacent edge of the panel (end cap) should be 1 11/16
"