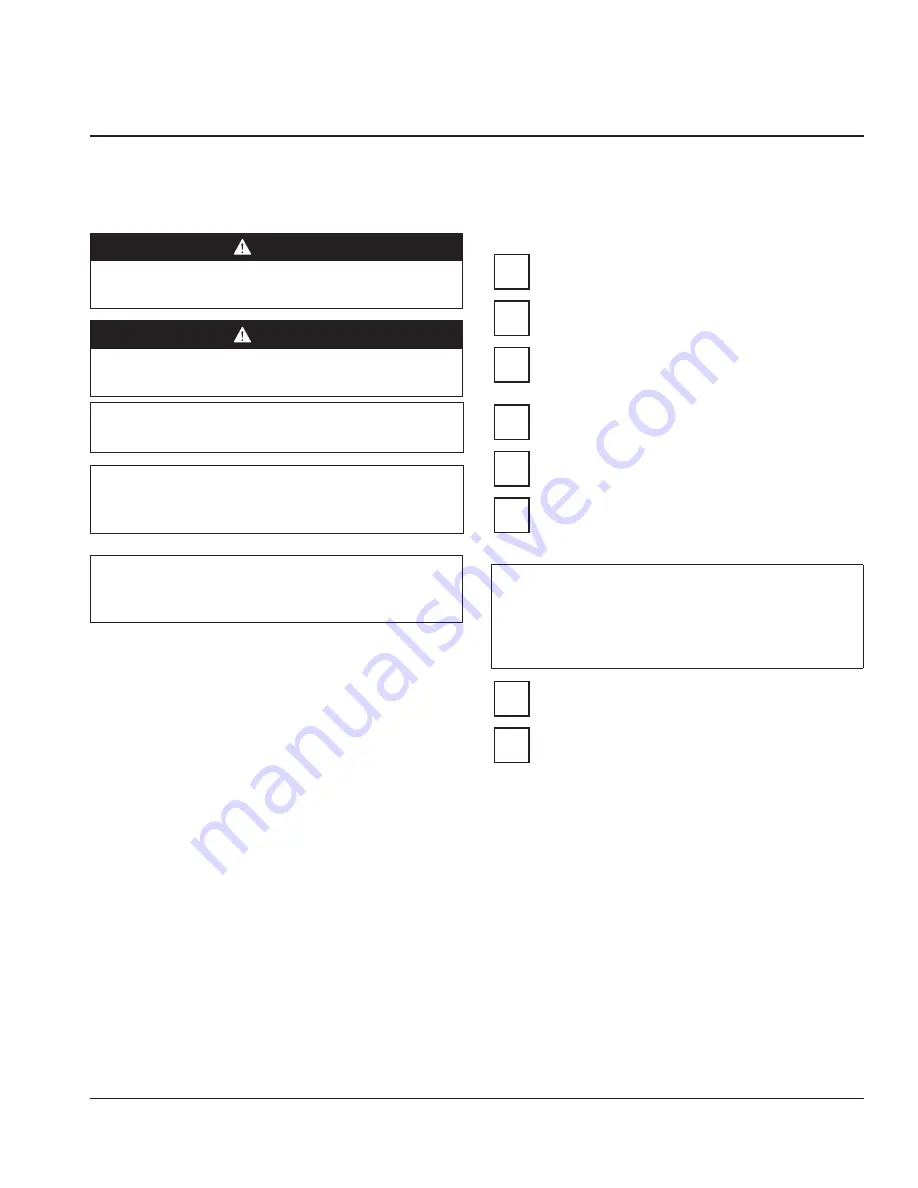
Part Number: 9290312 May/17/2016 9
Step-by-Step Installation
These instructions are provided to assist the qualified installer. Contact your Manitowoc Foodservice Service Agent or call
Manitowoc Foodservice for information regarding start-up services.
DANGER
Use appropriate safety equipment during installation
and servicing.
DANGER
Installation must comply with all applicable fire and
health codes in your jurisdiction.
n
Warning
Remove all removable panels before lifting and installing.
n
Warning
Do not damage the refrigeration circuit when installing,
maintaining or servicing the unit.
IIportant
All plumbing must conform to local, state and national
codes.
PRE-INSTALLATION CHECKLIST
Any damage should be noted and reported to the
delivering carrier immediately.
Check the lower portion of the unit to be sure
casters are not bent.
Visually inspect the refrigeration package,
compressor compartment housing. Be sure lines
are secure and base is still intact.
Inspect installation location behind the unit for
electrical outlet location and Nitrogen (N
2
).
Check for correct voltage at outlet dedicated for
the Nitrogen Beverage Dispenser.
Verify floor of install location is within 1/2” (1.3 cm)
of level front to back, side to side and all casters are
touching the floor.
n
Warning
The mass of this appliance will allow it to move
uncontrolled on an inclined surface. Adequate means
must be provided to prevent uncontrolled movement
at all times.
Check that internal connections are secure and did
not vibrate loose during shipment.
Installation location has proper ventilation where
unit has access to ambient air.
Section 2
Installation