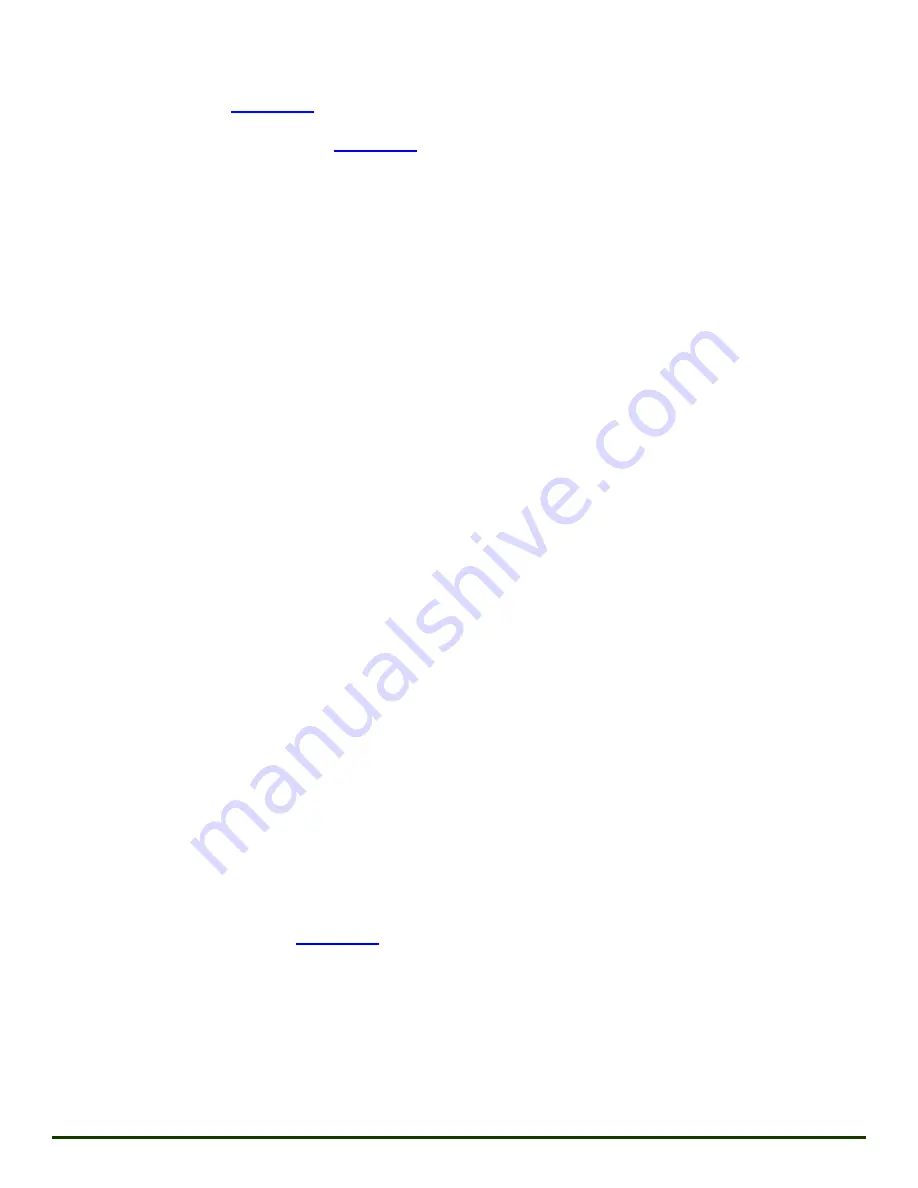
9.6
Replacing the Fluid End
Follow the procedure in
Section 9.2
for removing the fluid end plungers, packing nuts, and valves.
Follow the recommendations found in
Section 4.1
for preparing to lift the fluid.
The fluid end is attached to the power end by the tension indicating Maxbolts™. Do not begin to remove these
bolts until a lifting harness is in place and the slack has been removed.
1)
Remove packing lubrication supply and discharge lines from the fluid end adapters.
2)
Loosen all tension indicating Maxbolts™ using a 1-3/8” 12 point standard socket and a 1” 12 point
standard socket (triplex only). Remove all but the two top center bolts. As these last two bolts are
loosened, work the lift hoist so that it is positioned over the fluid end’s center of gravity. With some
tension on the lifting harness, carefully remove the last two bolts. The center of gravity is
approximately over the center of the front face. Maintain control of the fluid end after it is free from
the power end.
3)
If the fluid end is being removed for inspection, the inside must be cleaned to bare metal and a liquid
dye penetrant or magnetic-particle inspection performed to see if there are any stress cracks in any of
the large bores. Do not reuse a fluid end that contains stress cracks. The fluid end cannot be
repaired by welding. If it is cracked, it must be replaced.
CAUTION
: A primary cause of failure in steel fluid ends is cracks which initiate at corrosion pitting
sites. Carefully examine the fluid end wetted surfaces for corrosion pitting. Severe pitting greatly
increases the likelihood of crack formation and failure can occur relatively unexpectedly.
4)
Whether replacing the old fluid end or installing a new one, inspect all openings for damage or
contaminates. Clean as necessary.
5)
Before installing a fluid end, clean the mating IDs on the power end frame and the male pilot on the
fluid end adapter rings, then lightly hand polished with a 220 to 240-grit Emory cloth. Coat the
mating surfaces with a light oil or grease.
6)
Before installing the fluid end, clean the Maxbolts™ and coat all contact areas (threads, underneath
bolt head, deck of fluid end counterbore) with Dow Corning® G-n Metal Assembly Paste. Be
certain to replace the hardened steel washers if using a stainless steel fluid end.
CAUTION
: Using high quality assembly paste is crucial to achieving proper tension in the Maxbolts™.
Low quality assembly pastes may prevent the bolt from achieving proper pre-load.
7)
Prepare for lifting per
Section 4.1
, and have two top Maxbolts™ ready to thread into place. Lift the
fluid end in place. Do not release the holding pressure against the fluid end until the first two top
bolts are hand tight.
8)
Apply torque to the Maxbolts™ until the indicator reaches approximately 90%-95%. If the
indicator is not working, replace the bolts with new ones obtained from MSI.
CAUTION
: Do not attempt to tighten the Maxbolts™ with a torque value. Use only the dial indicator
to determine when the pre-load has been achieved, this is the most accurate method. Insufficient pre-
Revision K 03/12/2019
MSI - A Division of Dixie Iron Works, Ltd. All rights reserved.
Page 58