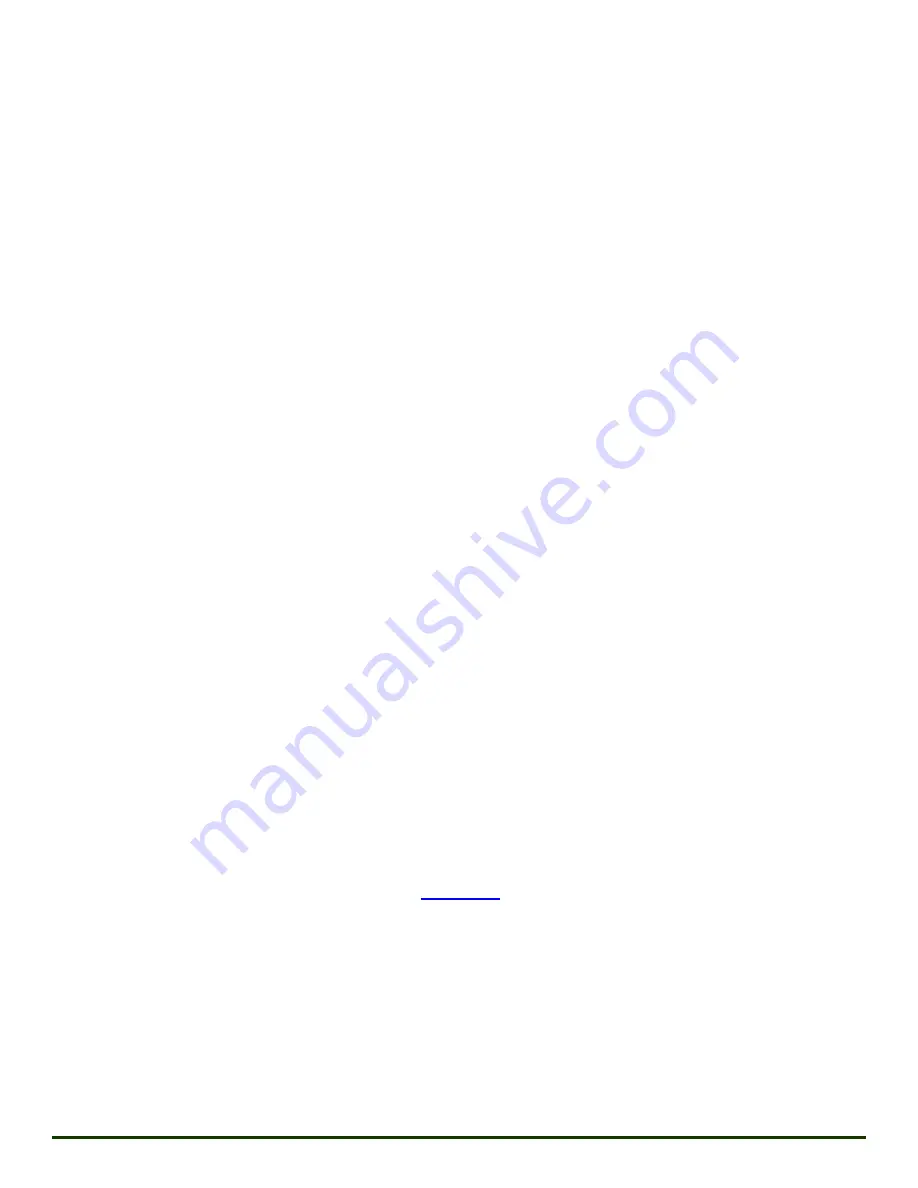
of the packing nut tool into the packing nut and extract through the packing service port. Inspect the
o-rings on the packing nut for signs of cutting, chemical attack, or dry rot. Replace as required.
MSI Hybrid™ Well Service Pump Enhancement – It is not necessary to use special tools to retain the
stuffing box adapter (junk ring) in the fluid end. There is sufficient space to leave the ring in the
packing nut and extract through the packing service port.
6)
Remove the stuffing box adapter from the packing nut by tapping out with a brass punch, be careful
not to damage the seal bore. Inspect the o-rings and back-up rings on the adapter for signs of
cutting, chemical attack, or dry rot. Replace as required.
7)
Remove the packing set from the packing nut. Examine each ring of packing, the header ring, and
the brass lantern ring for excessive wear and scoring. Replace as required.
8)
Blow compressed air through each lubrication port on the packing nut to ensure that the lubrication
passage is unobstructed.
CAUTION
: Always wear appropriate PPE, especially eye protection, when using compressed air to
clean pump parts.
9)
Reinstall packing in the reverse order from which it was removed: wiper seal, lantern ring, packing
set (header ring last), stuffing box adapter. Lightly coat all parts with assembly grease such as
Lubriplate® No. 105 Assembly Paste.
10)
Reinstall the packing nut using the packing nut tool and screw in until tight and then back it off one
turn. This will reduce the chances of damaging the packing seals when installing the fluid end
plunger.
MSI Hybrid™ Well Service Pump Enhancement – It is not necessary to keep packing nuts matched with
a particular cylinder. Since there are no plumbing connections on the packing nut to keep indexed, any
packing nut can be installed in any plunger bore.
11)
Clean the fluid end plunger and lubricate the threads with an anti-seize thread compound. Coat the
hard surface area of each plunger with a light lubricant only, and insert it into the packing. Using the
plunger tool and a 10 lb. hammer, bump the plunger into the packing while holding it as straight as
possible to the packing bore centerline. Continue bumping the plunger through the packing until the
threaded end just passes through the packing nut. Using the driveline, turn the crankshaft slowly
until the power end plunger contacts the threaded end of the fluid end plunger. Tighten the fluid end
plunger to the torque value specified in
Section 14
.
MSI Hybrid™ Well Service Pump Enhancement – The fluid end plunger threads into a steel part instead
of an iron casting and utilizes an ACME thread form instead of a UNC thread. This design helps to
eliminate damage such as breakage of threads and reduces potential for cross-threading.
12)
Tighten each packing nut until it comes to a solid stop. There should be about 1/32" gap between
the packing nut face and fluid end adapter face. This indicates that the packing nut is fully engaged.
13)
The packing nut retention screw must be aligned with the rotation arresting slot of the fluid end
adapter. It may be necessary to rotate the packing nut slightly CCW to achieve alignment. Once
Revision K 03/12/2019
MSI - A Division of Dixie Iron Works, Ltd. All rights reserved.
Page 48