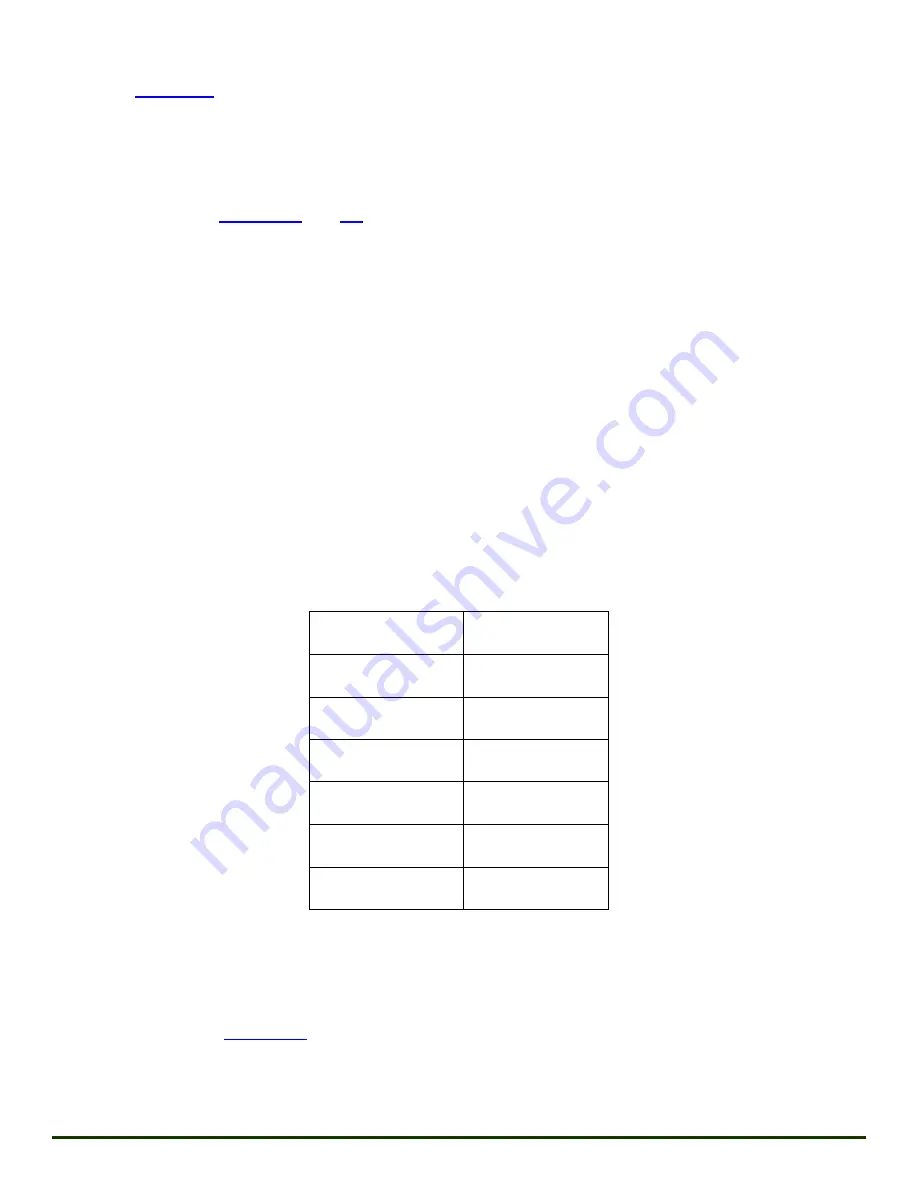
11)
Check for system leaks or unusual noises. If unusual noises are heard, shut the pump off and see
Section 13
.
12)
Increase speed and pressure slowly, checking for leaks or unusual noises.
13)
Insure that lubrication oil pressure, flow, and temperature are kept in the recommended ranges
throughout operation of the pump. For recommended lubrication pressure, flow, and temperature
ranges; see
Section 5.1
and
5.8
.
14)
In cold service starts, it is best to let the oil warm up prior to running the pump at high RPMs or high
pressures.
15)
If the pump was delivered with valves installed, then the valves were already seated during the FAT
test. If the valve seats were replaced in the field, the following procedure must be followed to set the
valve seats:
a)
The tapered valve seats must be fully seated to allow optimum flow area between the valve and
the seat. Washout may also occur between the valve and the fluid end if the valves are not fully
seated.
b)
Connect a 3/4” to 1” orifice test choke to the discharge circuit and adjust it to full open. Shift the
transmission to first gear, and increase the throttle setting to achieve 50-100 crank RPM. Slowly
increase discharge pressure using the test choke until a series of audible popping noises are
heard. This indicates the seats have properly set in the taper. The approximate seating pressure
for each fluid end plunger size is as follows:
Plunger Diameter Seating Pressure
2.75"
14,320 PSI
3.00"
12,030 PSI
3.25"
8,840 PSI
3.50"
8,840 PSI
4.00"
6,765 PSI
4.50"
5,345 PSI
16)
If the fluid end plunger or packing has been replaced, then the packing nut may need to be
retightened after the pump is run under pressure for a few revolutions. The packing in this pump is
non-adjustable; therefore, fully tightening the packing nut is required to properly set the gland
length. See
Section 9.2
for instructions on this.
Revision K 03/12/2019
MSI - A Division of Dixie Iron Works, Ltd. All rights reserved.
Page 39