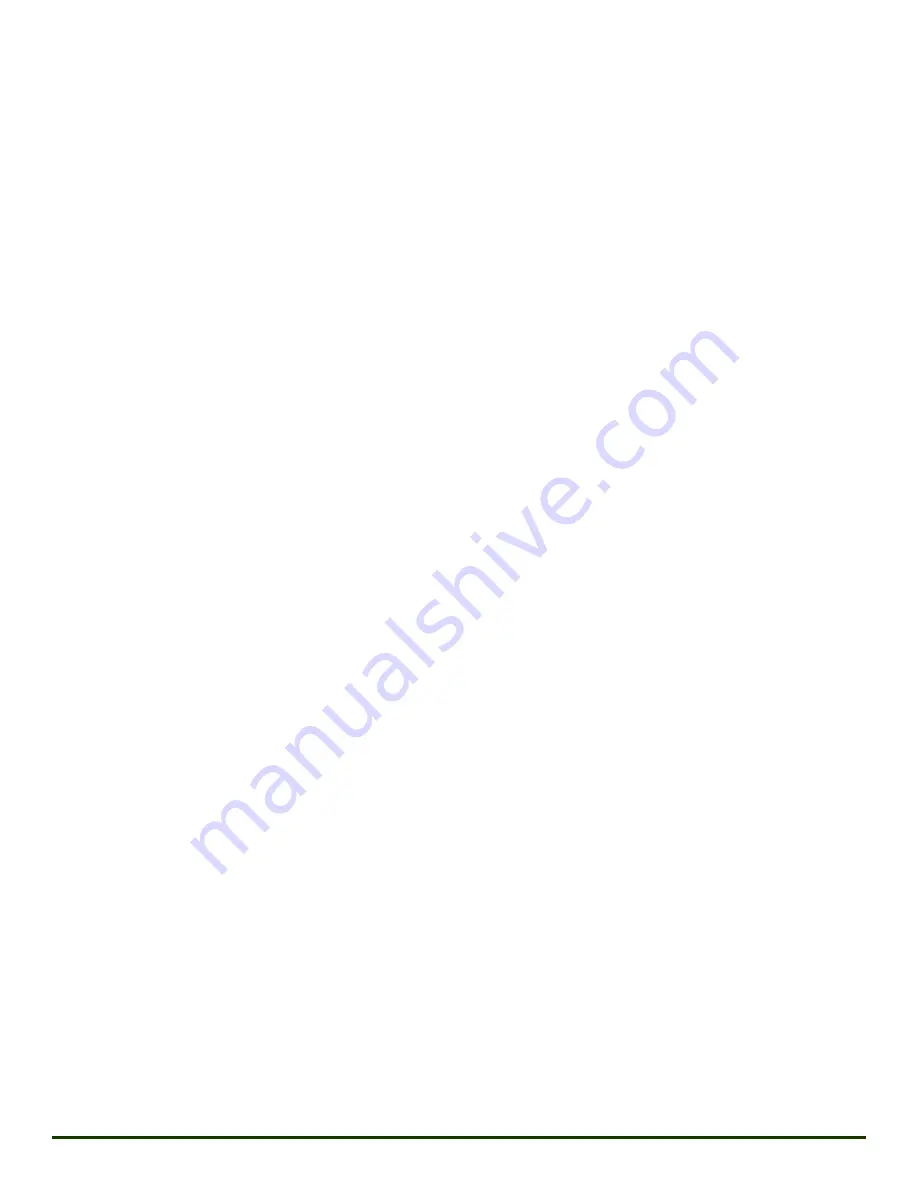
9.2
Replacing Fluid End Plunger and Packing
The fluid end plungers and packing should be inspected for wear or corrosion after each well service job and be
replaced as needed.
CAUTION:
Do not perform any service on the fluid end until you have verified that there is no
pressure in the discharge system, the suction charge pump is off and isolated, and suction pressure has
been relieved. A closed valve near the discharge can trap pressure between the discharge and the closed
suction valves of the pump. Bleed off this pressure before continuing. Do not perform service on the
fluid end with the drive engine running. If there is a bladder-type pulsation dampener on the system,
either isolate it or bleed the nitrogen pressure from the bladder. Failure to follow these precautions can
lead to serious injury.
1)
After heeding the safety precautions, remove the suction cover using the valve cover tool (FEC0024)
and a 10 lb. hammer. Replace cover nut seal if damaged.
MSI Hybrid™ Well Service Pump Enhancement – The suction cover nuts consist of a thread half and a
gland half and are attached with a shoulder screw to allow one piece extraction yet also allow the two
parts to rotate independently. This design effectively prevents seal bore galling and scoring that is
common in one piece cover nuts.
CAUTION:
Well service fluid will be trapped between the inlet and outlet valves and will spill out
when removing the suction valve covers. Expectation of and preparation for this is important for safety
and environmental reasons. A catch pan, appropriate absorbent materials, and personal protective
equipment (PPE) will be needed.
2)
Open the weather cover and loosen the retaining screws on the plunger safety cover using a 9/16”
wrench and slide it towards the rear of the pump to expose the packing service port.
3)
With a 9/16” wrench, back out the packing nut retention screw approximately 2 turns. This will
disengage the rotation arresting slot of the fluid end adapter and allow the packing nut to rotate.
Loosen the packing nut at least one full turn using the included packing nut tool (FEC0368).
MSI Hybrid™ Well Service Pump Enhancement – The lubrication lines plumb into the fluid end adapter
and do not need to be removed before unscrewing the packing nut.
4)
Unscrew the fluid end plunger from the power end plunger using the plunger tool and extract it from
the fluid cylinder through the suction cover bore. Be careful not to damage the fluid end plunger
while removing it. Check each fluid end plunger for wear, scoring, pitting, and corrosion on the
hard surface area, and check for damage to the face and threads that mate with the power end
plunger. Replace as needed.
MSI Hybrid™ Well Service Pump Enhancement – An added benefit to the design of this pump is that
during routine fluid end maintenance the power end is never opened to atmosphere. The power end
plunger remains in place and acts as a barrier to prevent blowing dirt, sand, and foreign objects from
entering the power end and damaging bearings or lubrication pumps.
5)
Continue unscrewing the packing nut until the threads are no longer engaged yet the nut is still
supported by the fluid end adapter, then turn until a tapped hole is facing up. Screw the threaded end
Revision K 03/12/2019
MSI - A Division of Dixie Iron Works, Ltd. All rights reserved.
Page 47