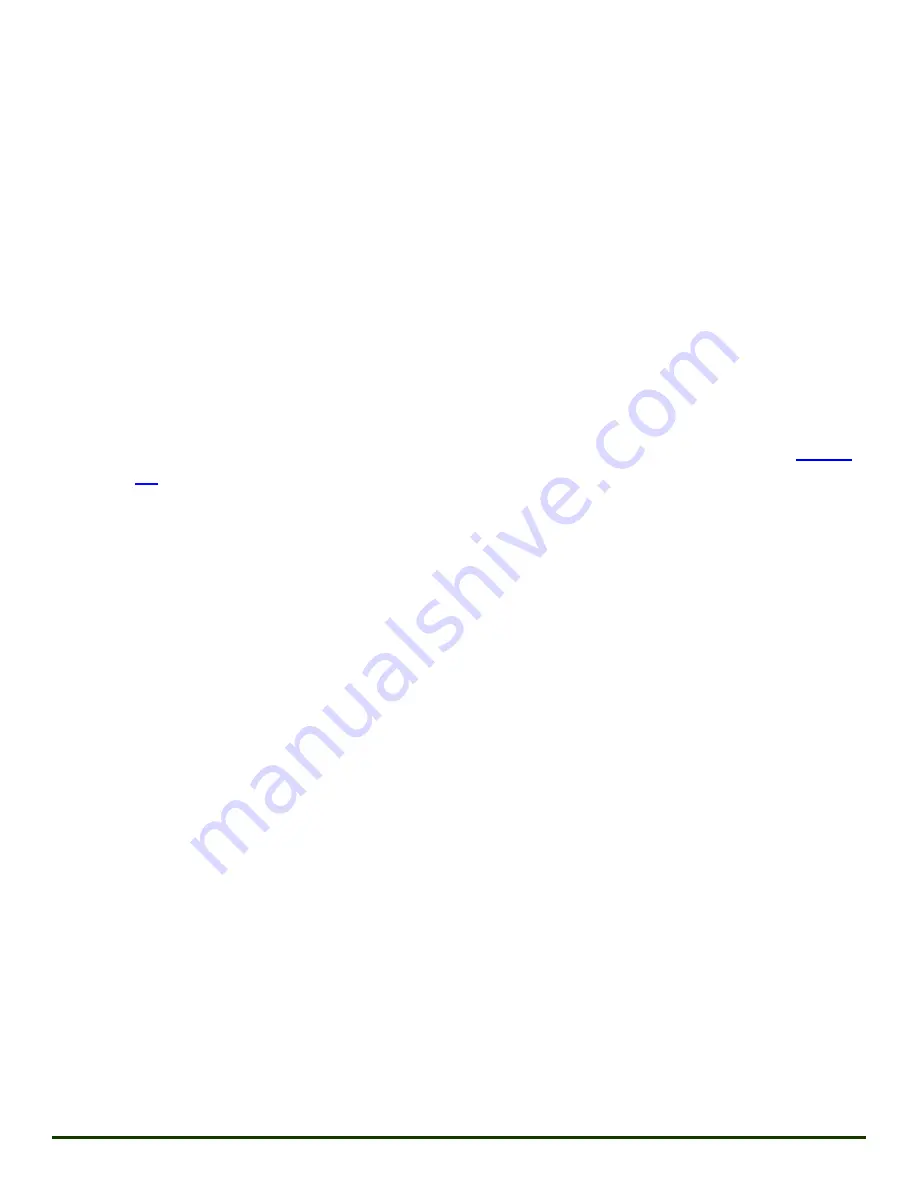
CAUTION:
MSI highly recommends that only valves and seats from the same manufacturer be used.
In comparison the parts may look similar but slight variations in design and manufacture could cause the
pump to operate unsatisfactorily. The flow characteristics of the valve, valve seat, valve stop, and valve
spring are all designed for optimum flow through an MSI fluid end. Using valve components not
supplied by MSI can result in rough operation of the pump due to insufficient fluid flow area around the
valve. Insufficient flow area will result in excessive turbulence, cavitations, damaging vibrations, and
premature wear of the fluid end and its internal components. Excessive vibrations can result in manifold
and flow line fatigue failures, which could result in injury, death, equipment damage, and loss of well
control.
8)
Reinstall the suction valve spring and the suction valve stop making certain the valve stop is turned
until the retaining spring is securely seated in the groove in the cylinder. Do not leave the valve stop
in a position where the plunger may strike it. If the spring does not securely engage the slot remove
the valve stop and reset the spring by bending it slightly away from the valve stop.
9)
Remove the seals from each of the discharge and suction covers. Clean the covers thoroughly and if
necessary remove surface rust from cover and fluid cylinder seal bores with 220-240 grit Emory
cloth. Reinstall new seals, making sure they are facing the direction shown in the sketch in
Section
9.1
.
10)
Coat the suction cover and discharge cover threads with anti-seize thread compound, and coat the
seal with light grease. Finally, install the cover nuts with the valve cover tool and a 10 lb. hammer.
Revision K 03/12/2019
MSI - A Division of Dixie Iron Works, Ltd. All rights reserved.
Page 52