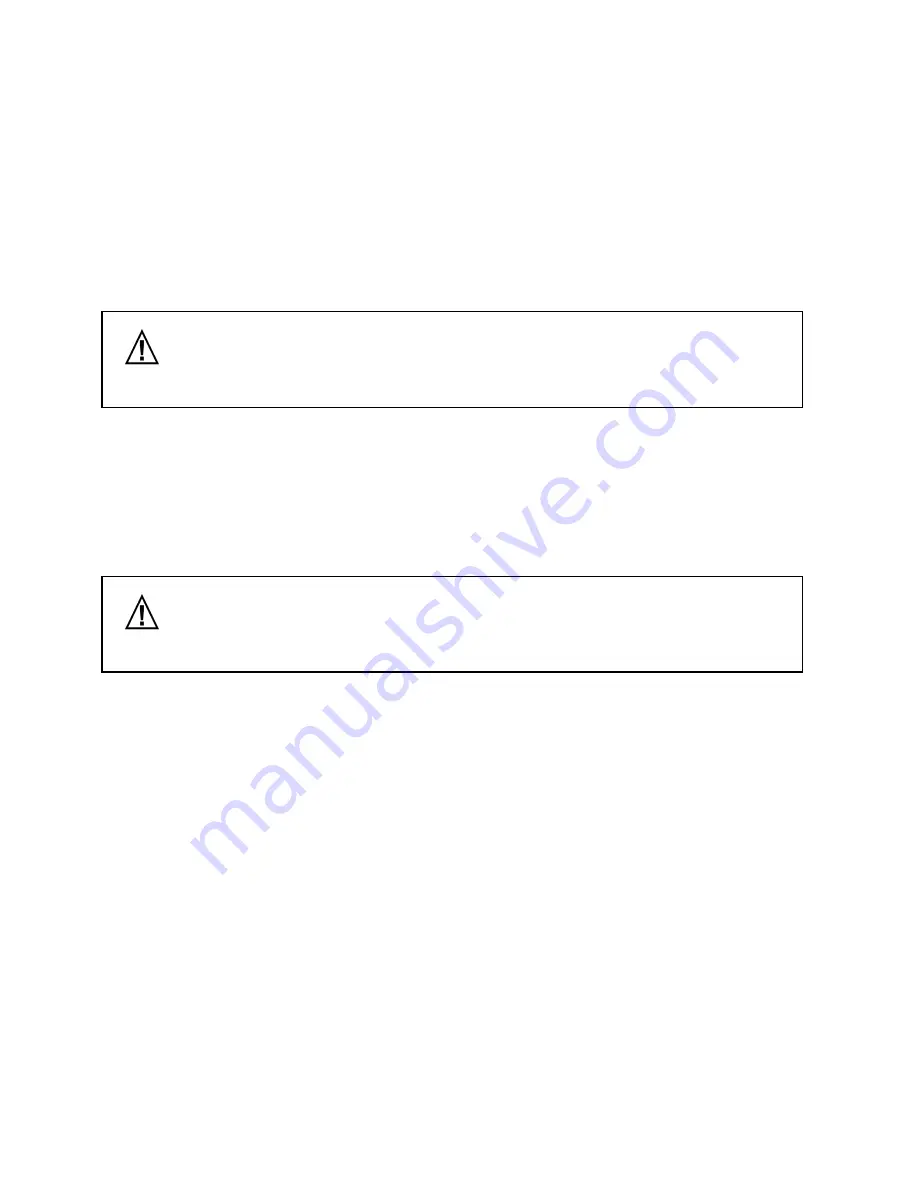
7.3.2
Driver Board
The driver board contains two potentiometers which are used to set under voltage and over current
protection in the polyphase chopper circuitry. These potentiometer do not normally need
adjustment in the field.
7.3.2.1 Over Current Protection
Over current protection should only be calibrated after consultation with the factory.
Gross misadjustment can cause chopper and inverter failure.
Place a dc voltmeter between test point TP6 (positive) and test point TP7 (negative). With only
the control power applied, adjust potentiometer P1 to 6.00 V.
7.3.2.2 Under Voltage Protection
Under voltage protection should only be calibrated after consultation with the factory.
Gross misadjustment can cause chopper and inverter failure.
Connect the power supply to an adjustable ac source and connect an ac voltmeter to monitor the
voltage applied to the input terminals. Tests can be performed under no load conditions. Set the
ac source to rated voltage. Turn the control power, press the start switch, and a adust the output
voltage to 10% full scale output. Decrease the ac source to a value between 75% to 82% of rated
voltage. Adjust potentiometer P2 until the output drops to zero; the transition will be abrupt.
Decrease the ac source to a value between 72% to 79% of rated voltage. The main contactor
should turn off.
112
Summary of Contents for DP SERIES II
Page 1: ...OPERATING AND SERVICE MANUAL DP SERIES II DC POWER SUPPLIES...
Page 2: ......
Page 3: ...MAGNA POWER ELECTRONICS INC 39 ROYAL ROAD FLEMINGTON NJ 08822 January 6 2010...
Page 4: ......
Page 6: ...improper use of the equipment and accessories ii...
Page 28: ...Figure 1 2 DP Series air cooled 10 kW to 30 kW package drawing with D Version front panel 15...
Page 47: ...Figure 3 7 Set remote sense Figure 3 8 Set internal control 34...
Page 48: ...Figure 3 9 Set external control Figure 3 10 Set rotary input 35...
Page 49: ...Figure 3 11 Set keypad input Figure 3 12 Set external program input 36...
Page 50: ...Figure 3 13 Set remote input Figure 3 14 Set external interlock 37...
Page 53: ...Figure 3 15 Calibration 40...
Page 61: ...Figure 3 24 Calibration 48...
Page 63: ...Figure 3 25 a Local and b remote sensing 50...
Page 64: ...Figure 3 26 External a resistive b voltage and current programming 51...
Page 111: ...98...
Page 113: ...Figure 5 1 Configuration setup Figure 5 2 GPIB communications setup 100...
Page 118: ...Figure 5 7 Register Panel Figure 5 8 Calibration Panel 105...
Page 119: ...Figure 5 9 Firmware Panel Figure 5 10 Modulation Panel for Version D models only 106...
Page 121: ...Figure 6 1 Block diagram 108...
Page 139: ...Figure B 1 Information Panel Figure B 2 Configure Panel 126...
Page 140: ...Figure B 3 Reboot in Progress Panel Figure B 4 Web Control Panel 127...
Page 145: ...Figure D 1 RS485 a 2 wire and b 4 wire connections 132...