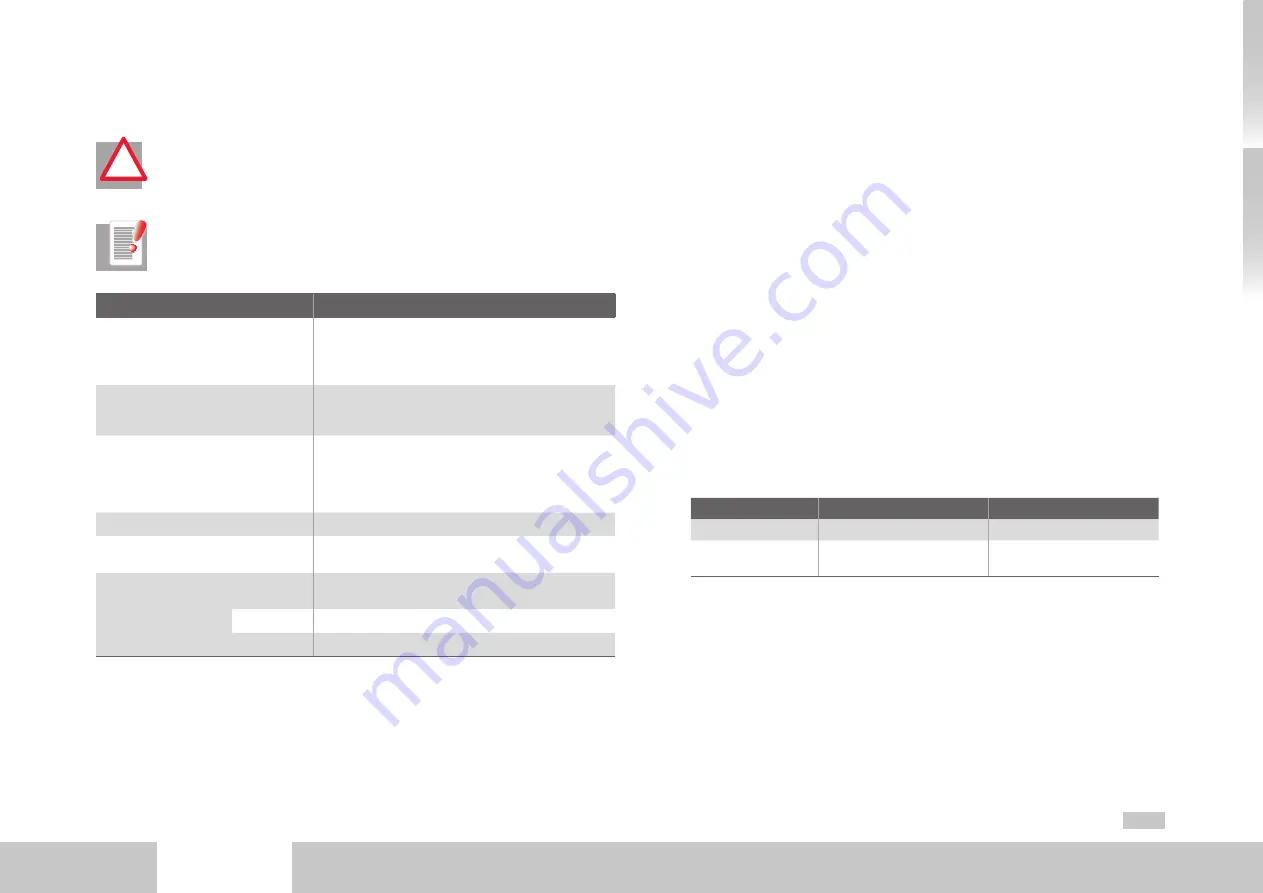
moog
MSD Servo Drive DC-AC Operation Manual
[
]
Appendix
Technical data
81
Id.-No.: CA97554-001 Date: 06/2012
B.7 Hydrological data of liquid cooling
!
ATTENTION!
The temperature of the cooling plate must not be more than
+10 °C (+50 °F) below the ambient temperature. Condensation will result in
destruction of the device.
NOTE:
Customers must provide adequate heat dissipation for the water
cooler. The coolant should be approved by Moog GmbH if it deviates from
the following requirements::
Requirements
Limits
Coolant quality
Recommended: Drinking water + corrosion inhibitor
(e.g. ethylene glycol)
Not permitted: Chlorid ions (Cl- >100 ppm), Calcium
carbonate (CaCO3 >160 ppm)
Pollution
The coolant must be as pure as possible so as not to
clog the ducts. At a suspension concentration above
15 mg/dm³ continuous cleaning is recommended.
Cooler temperature
The coolant temperature may be b5 °C
(+41 °F) and +40 °C (+104 °F). However, the coolant
temperature must not be more than 10 °K below the
ambient temperature, so as to prevent condensation on
the heat sink.
Cooler material
Aluminium
Coolant pressure
(nominal/maximum value)
1 bar / 2 bar
Coolant flow rate
(nominal/maximum
value)
Size 3 to
Size 4
3 l per min / 4 l per min
Size 5
8 l per min / 11 l per min
Size 6A
11 l per min / 13 l per min
Table B.21 Liquid cooling requirements
B.8 Dynamic heat sink temperature
monitoring
If the coolant flow breaks down or is not generated, the power stage may overheat. For
this reason the servo drive is fitted with a dynamichet sink temperature monitor which
shuts off the servo drive in the event of overheating. The servo drive shuts down at a
heat sink temperature of +65 °C (+149 °F) regardless of the temperature gradient.
B.9 UL approbation Size 5 and Size 6A
1. Control board input ratings 24 V DC.
2. Maximum surrounding air tempe40 °C (+104 °F).
3. Internal overload protection operates within max. 3 seconds for Size 5 or max.
10 seconds for Size 6A when reaching 200% of the motor full load current.
4. Suitable for use on a circuit capable of delivering not more than
Size 5:
5.000 Amperes DC, 700 Volts DC maximum.
Size 6A:
10.000 Amperes DC, 700 Volts DC maximum.
5. All wiring terminals shall be marked to indicate proper connections for the power
supply, load and control circuitry.
6. Tightening torque:
DC supply input
Motor terminals
Size 5 (air / liquid)
22-39.8 lb-in
MKDSP25-15: 40 lb-in
Size 6A (air / liquid)
HDFK95-F-VP: 175 lb-in
WGK95VPF: 133 lb-in
UKH95: 175 lb-in
UKH150: 270 lb-in
Table B.22 Tightening torque
7. Use in a pollution degree 2 environment only.
8. Use +75 °C (+ 167 °F) copper conductors only.
9. Wiring terminal intended for connection of a field-installed equipment grounding
conductor shall be marked with “G”, “GR”, “GRD”, “GROUND”, “GROUNDING”
or with a grounding symbol 5019 defined in IEC Publication 417.
10. Inverters are to be supplied by a suitable DC source providing voltage transients
limitation to 4 kV maximum.