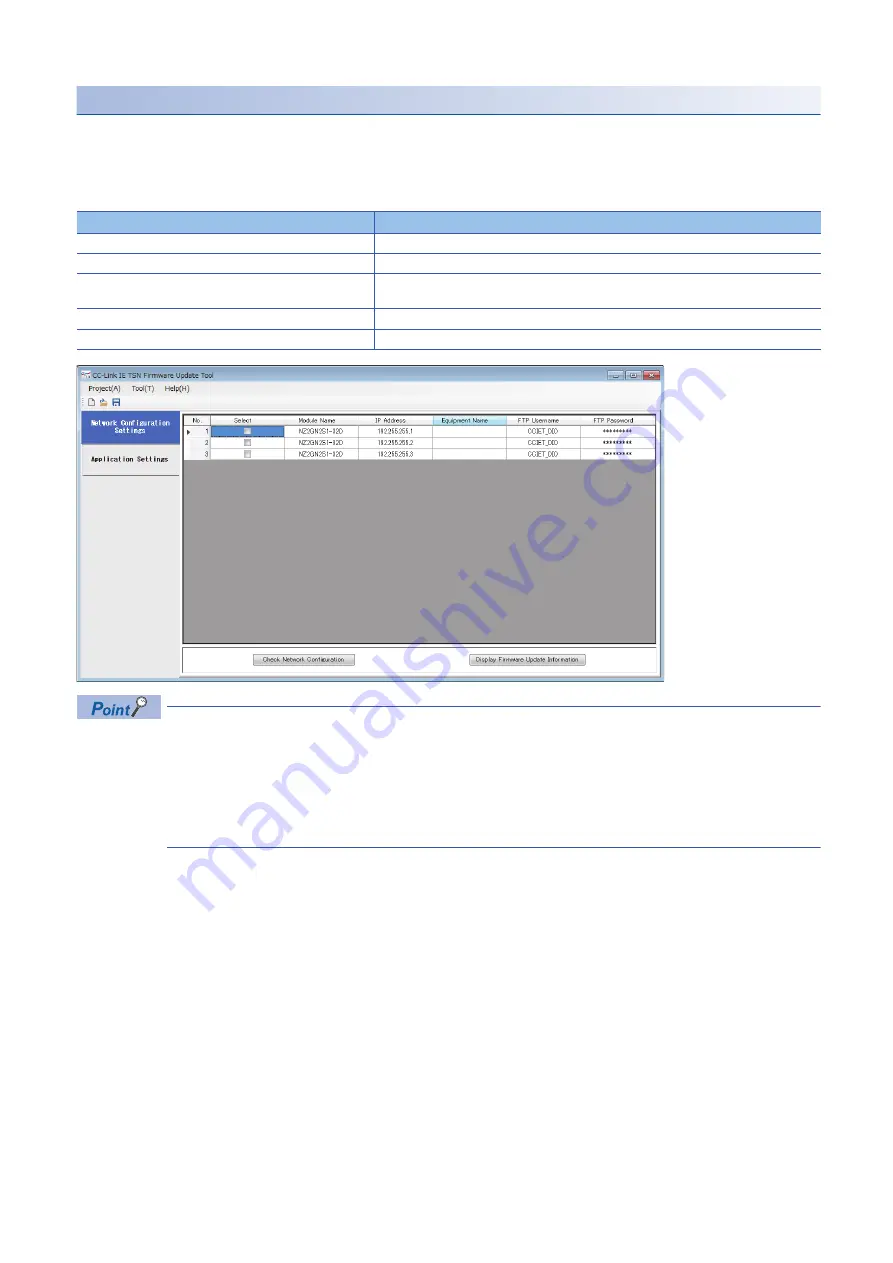
180
8 FUNCTIONS
8.9 Firmware Update Function
Setting procedure
To perform a firmware update on the I/O module, the CC-Link IE TSN Firmware Update Tool must be set.
For details on the CC-Link IE TSN Firmware Update Tool, refer to the "Help".
■
Setting the Network Configuration Settings window
Set the following items in the Network Configuration Settings window.
• When CCIET_DIO is used for "Module Name", CCIET_DIO is automatically set for "FTP User name" and
"FTP Password".
• When the firmware update file to be used is the same, and the strings of the module names set in the CC-
Link IE TSN Firmware Update Tool also match (the model names of the actual devices can differ), a
firmware update can be performed on I/O modules with different model names simultaneously.
Example: All the module names of the firmware update target I/O modules are set to NZ2GN2B1.
Item
Setting details
Module Name
Set the model names of the firmware update target I/O modules.
IP Address
Set the IP addresses of the firmware update target I/O modules.
Equipment Name
This setting is optional.
Set this item when you register multiple pieces of equipment and need to distinguish them.
FTP User name
Set CCIET_DIO in this column.
FTP Password
Set CCIET_DIO in this column.
Summary of Contents for NZ2GN2B1-32D
Page 2: ......
Page 112: ...110 4 PROCEDURES BEFORE OPERATION MEMO ...
Page 193: ...10 MAINTENANCE AND INSPECTION 191 10 MEMO ...
Page 263: ...I 261 MEMO ...
Page 267: ......