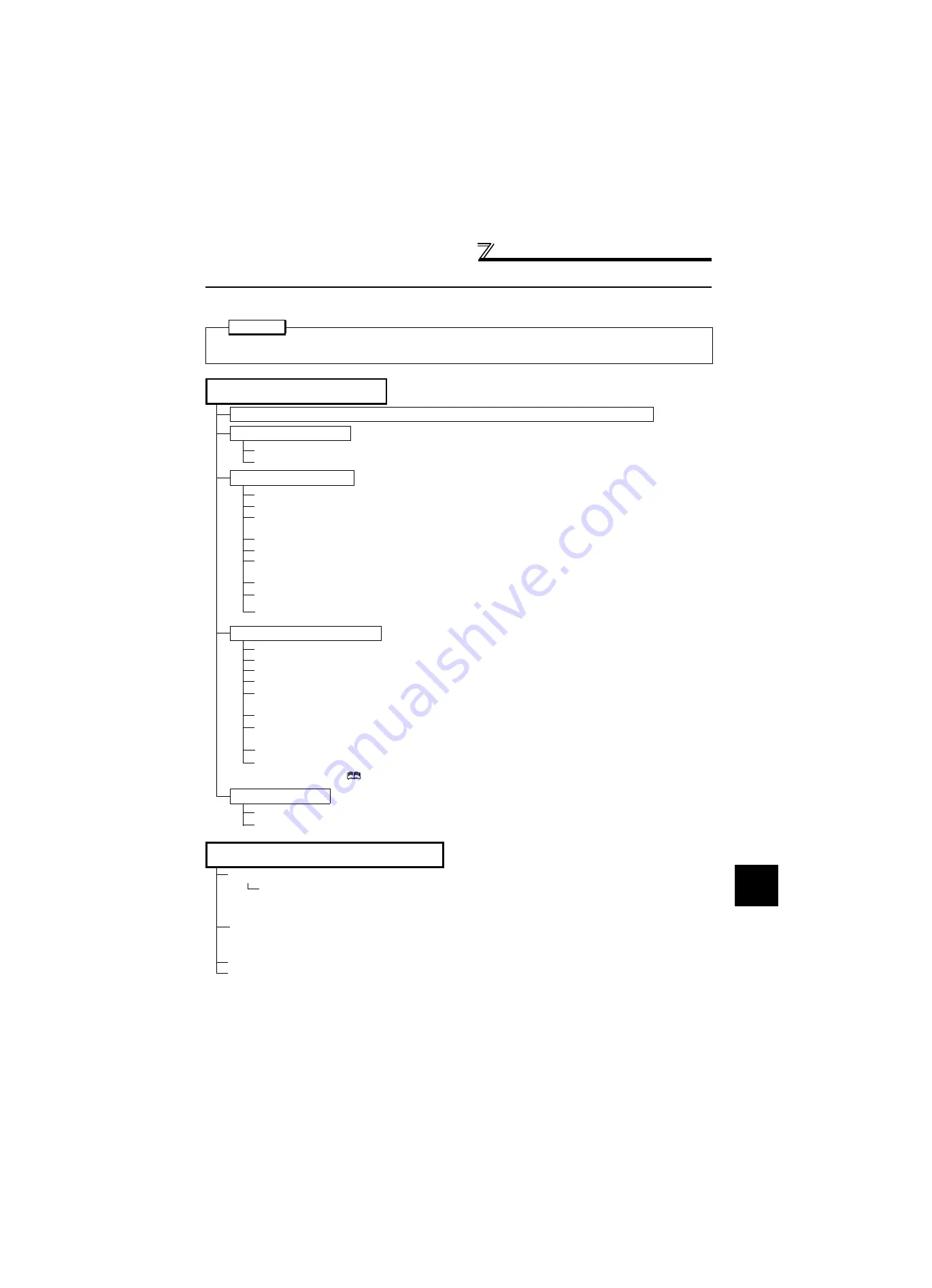
159
Check first when you have troubles
5.6 Check first when you have troubles
POINT
If the cause is still unknown after every check, it is recommended to initialize the parameters (initial value) then reset
the required parameter values and check again.
Check that
Pr. 78
Reverse rotation prevention selection
is not selected.
5.6.1 Motor will not start
1) Check the
Pr.0 Torque boost
setting if V/F control is exercised.
(Refer to page 59)
2) Check the main circuit
Check that a proper power supply voltage is applied (operation panel display is provided).
Check that the motor is connected properly.
3) Check the input signals
Check that start signal is input.
Check that both the forward and reverse rotation start signals are not input simultaneously.
Check that the frequency setting signal is not zero. (When the frequency command is 0Hz and the
start command is entered, FWD or REV LED on the operation panel flickers.)
Check that the AU signal is on when terminal 4 is used for frequency setting.
Check that the output stop signal (MRS) or reset signal (RES) is not on.
Check that the CS signal is not OFF with automatic restart after instantaneous power failure function
is selected (
Pr. 57
≠
"9999").
Check that the sink or source jumper connector is fitted securely.
(Refer to page 23)
4) Check the parameter settings
Check that the
Pr. 79
Operation mode selection
setting is correct.
Check that the bias and gain
(calibration parameter C2 to C7)
settings are correct.
Check that the
Pr. 13
Starting frequency
setting is not greater than the running frequency.
Check that frequency settings of each running frequency (such as multi-speed operation) are not zero.
Check that especially the
Pr. 1
Maximum frequency
setting is not zero.
5) Inspection of load
Check that the load is not too heavy.
Check that the shaft is not locked.
Check that the
Pr. 15 Jog frequency
setting is not lower than the
Pr. 13 Starting frequency
setting.
Check that the encoder wiring is correct. (during encoder feedback control or vector control)
Check that the
Pr. 359 Encoder rotation direction
setting under encoder feed back control or vector
control is correct.
Set "1" in
Pr. 359
if "REV" on the operation panel is on when the forward command is given.
Check that the voltage/current input switch is correctly set for analog input signal (0 to 5V/0 to 10V, 4
to 20mA).
Check that the operation location by
Pr. 550
and
Pr. 551
is correct.
(Refer to chapter 4 of
the instruction manual (applied))
5.6.2 Motor generates abnormal noise
No carrier frequency noises (metallic noises) are generated.
Check for any mechanical looseness.
Soft-PWM control to change the motor tone into an unoffending complex tone is factory-set to valid
by
Pr. 72 PWM frequency selection
.
Adjust
Pr. 72 PWM frequency selection
to change the motor tone.
Contact the motor manufacturer.
Check that the gain value under real sensorless vector control or vector control is not too high. Check the
setting of
Pr. 820 (Pr. 830) Speed control P gain
when speed control is exercised and
Pr. 824 (Pr. 834) Torque
control P gain
when torque control is exercised.
Summary of Contents for FR-A741-11K
Page 7: ...MEMO ...
Page 216: ...209 MEMO ...