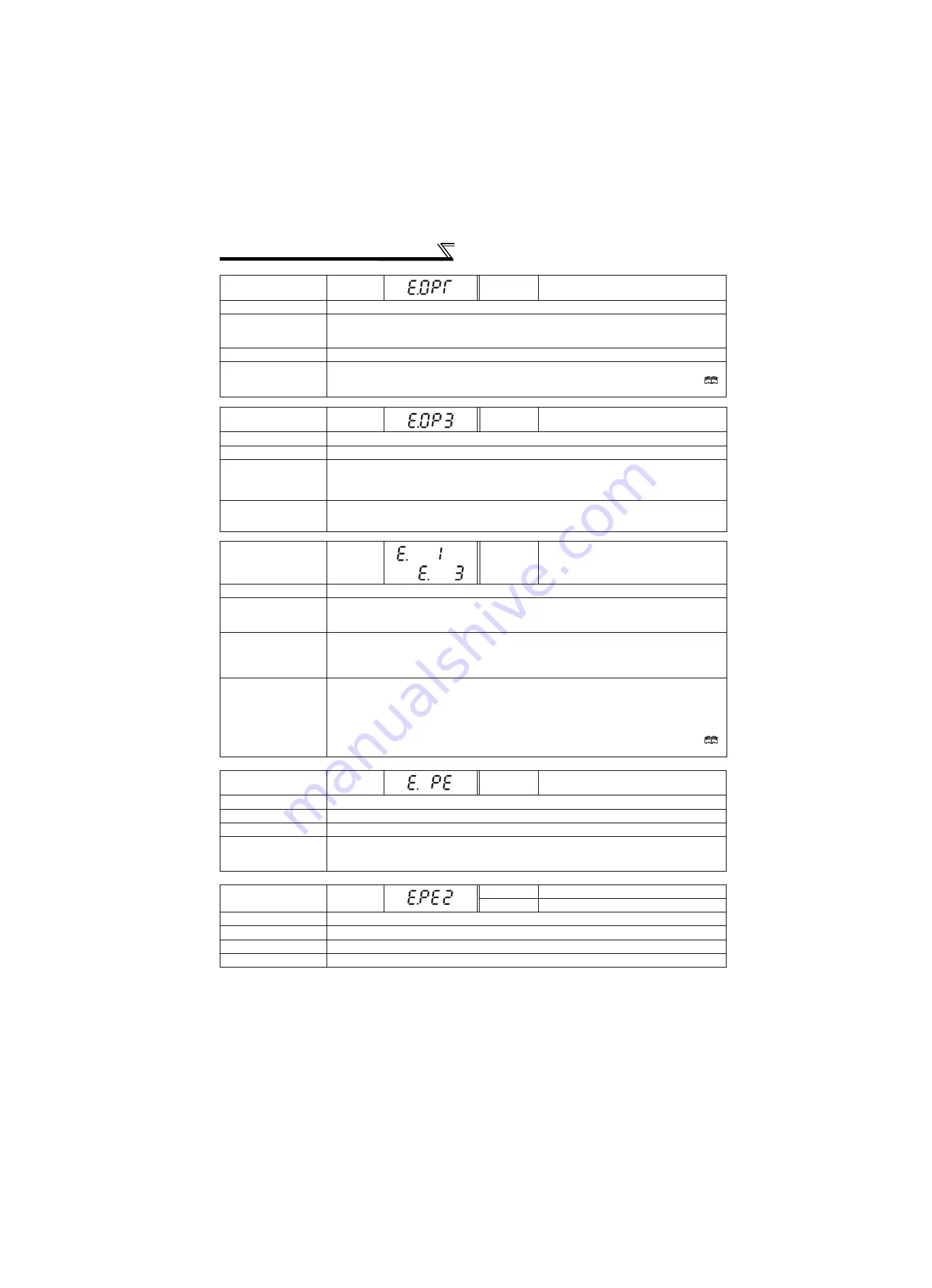
150
Causes and corrective actions
Operation Panel
Indication
E.OPT
FR-PU04
FR-PU07
Option Fault
Name
Option alarm
Description
Appears when torque command by the plug-in option is selected using
Pr. 804 Torque command source
selection
and no plug-in option is mounted.
Appears when the switch for the manufacturer setting of the plug-in option is changed.
Check point
· Check that the plug-in option for torque command setting is connected.
Corrective action
· Check for connection of the plug-in option. Check the
Pr. 804 Torque command source selection
setting.
· Return the switch for the manufacturer setting of the plug-in option to the initial status.
(Refer to
instruction manual of each option)
Operation Panel
Indication
E.OP3
FR-PU04
FR-PU07
Option 3 Fault
Name
Communication option alarm
Description
Stops the inverter output when a communication line error occurs in the communication option.
Check point
· Check for a wrong option function setting and operation.
· Check that the plug-in option is plugged into the connector securely.
· Check for a break in the communication cable.
· Check that the terminating resistor is fitted properly.
Corrective action
· Check the option function setting, etc.
· Connect the plug-in option securely.
· Check the connection of communication cable.
Operation Panel
Indication
E. 1 to
E. 3
FR-PU04
FR-PU07
Fault 1 to Fault 3
Name
Option fault
Description
Stops the inverter output if a contact faullt, etc. of the connector between the inverter and plug-in option
occurs or if a communication option is fitted to the connector 1 or 2.
Appears when the switch for the manufacturer setting of the plug-in option is changed.
Check point
1. Check that the plug-in option is plugged into the connector securely.
(1 to 3 indicate the option connector numbers.)
2. Check for excess electrical noises around the inverter.
3. Check that the communication option is not fitted to the connector 1 or 2.
Corrective action
1. Connect the plug-in option securely.
2. Take measures against noises if there are devices producing excess electrical noises around the inverter.
If the problem still persists after taking the above measure, please contact your sales representative or
distributor.
3. Fit the communication option to the connector 3.
4. Return the switch for the manufacturer setting of the plug-in option to the initial status.
(Refer to
instruction manual of each option)
Operation Panel
Indication
E.PE
FR-PU04
FR-PU07
Corrupt Memry
Name
Parameter storage device fault (control circuit board)
Description
Stops the inverter output if fault occurred in the parameter stored. (EEPROM failure)
Check point
Check for too many number of parameter write times.
Corrective action
Please contact your sales representative.
When performing parameter write frequently for communication purposes, set "1" in
Pr. 342
to enable
RAM write. Note that powering off returns the inverter to the status before RAM write.
Operation Panel
Indication
E.PE2
FR-PU04
Fault 14
FR-PU07
PR storage alarm
Name
Parameter storage device fault (main circuit board)
Description
Stops the inverter output if fault occurred in the parameter stored. (EEPROM failure)
Check point
——————
Corrective action
Please contact your sales representative.
to
Summary of Contents for FR-A741-11K
Page 7: ...MEMO ...
Page 216: ...209 MEMO ...