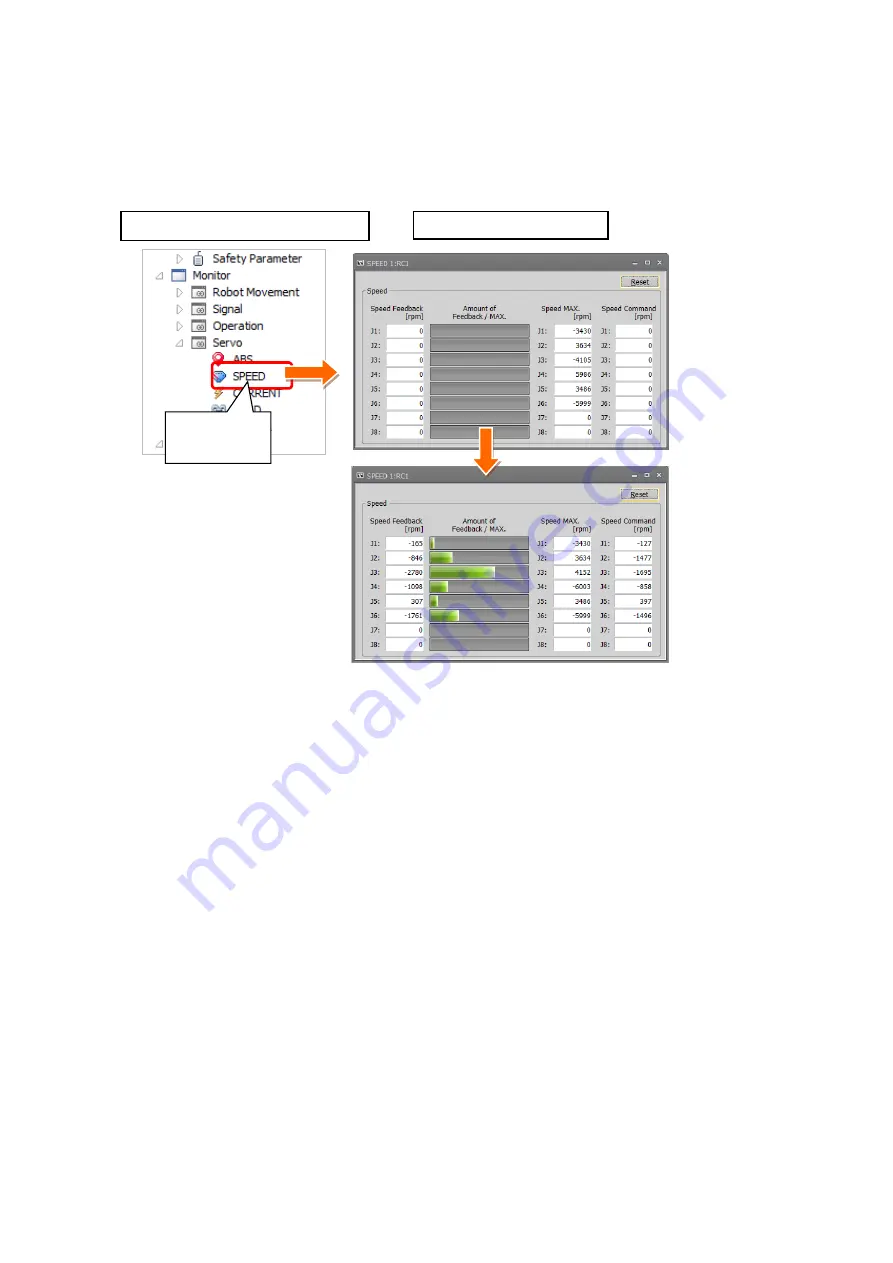
Abnormality detection function 59
How to check the motor speed with the RT ToolBox3 monitor function
1) From the RT ToolBox3 project tree, click [Monitor] - [Servo] and then double-click [Speed] to
display the [SPEED] screen.
2) You can monitor data related to the speed of each axis motor of the robot in action.
1) [Servo]
[SPEED]
1) Speed monitor screen
RT ToolBox3 project tree
Summary of Contents for CR800-D Series
Page 2: ......
Page 25: ...Basic specifications 23 MEMO ...
Page 31: ...Basic specifications 29 MEMO ...
Page 49: ...Startup and initial settings 47 MEMO ...
Page 57: ...Consumption degree calculation function 55 MEMO ...
Page 63: ...Operating information 61 MEMO ...
Page 91: ...Maintenance 89 MEMO ...
Page 193: ...Troubleshooting 191 ...