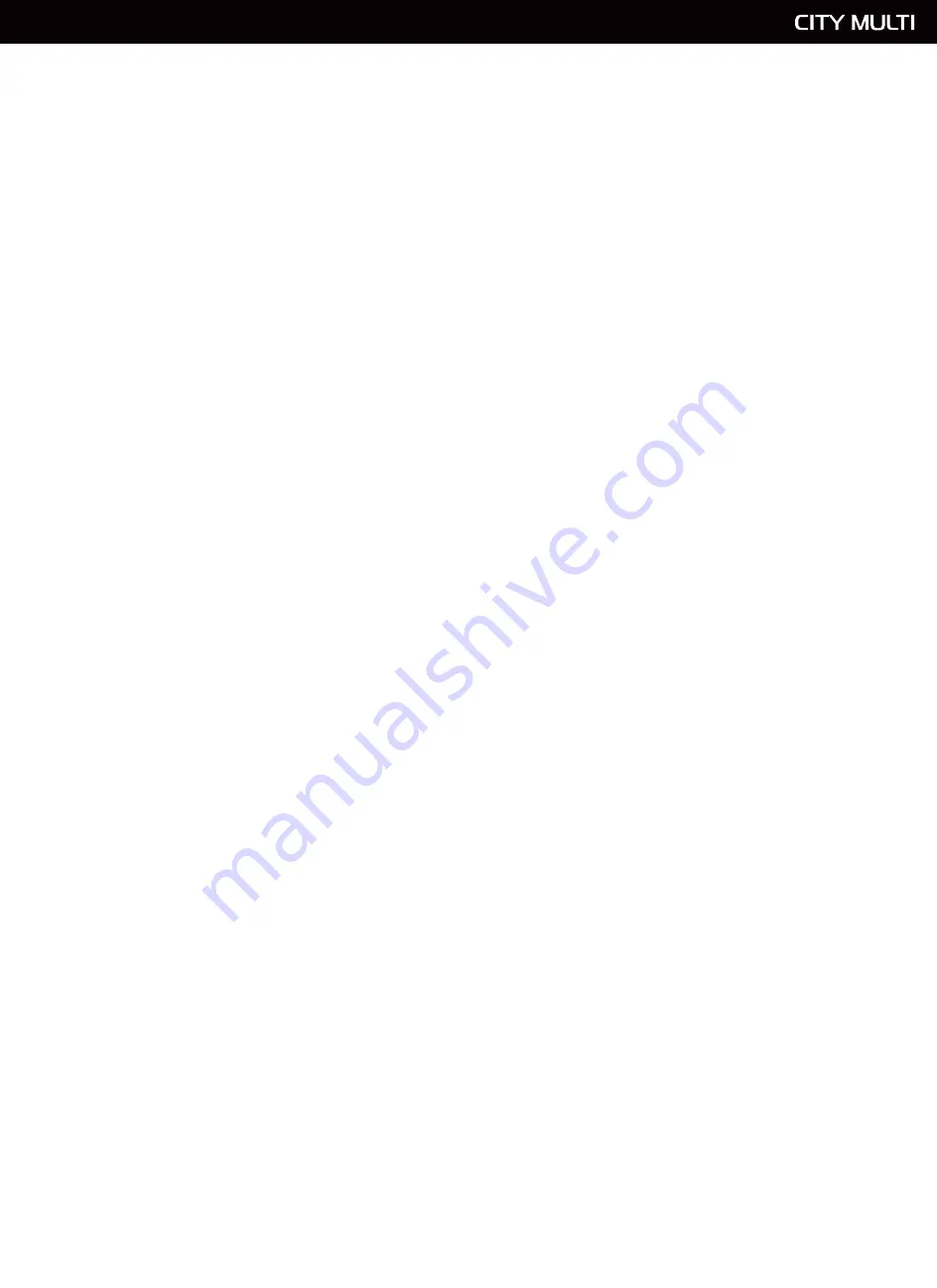
5
R410A flare nuts must also be used. Failure to do so can cause joint failure and refrigerant loss.
Prior to connecting flange and flare connections oil should be applied to the mating faces. Failure to do this causes tearing of
the copper flare surface. This causes leaking joints and joint failure due to material stress. The use of oil on connections also
allows the correct torque to be applied to the flare nut without pipe damage occurring.
Alkyl benzene oil is to be used to lubricate the connections. Alkyl benzene oil is hygroscopic (absorbs moisture) and should be
kept in an air tight container. The use of mineral based oil is not permitted as it contaminates the oil system and causes sludge
to form.
04. DAILY SECTIONAL SYSTEM PRESSURING
During installation of multiple circuit systems, it is recommended that at the end of each day, the pipe work be left pressurised
and any pressure loss be investigated prior to commencement of further piping the next day.
This procedure performs two functions:
1. Isolates any leaks to a small section of piping making it easier to trace and repair.
2. Pressurised pipe work prevents moisture and other foreign objects from entering the pipe work.
It is easier to pressurise the indoor units from the BC connection boxes.
NOTE: Please ensure that both vapour and liquid connections are pressurised (looped) otherwise damage to indoor LEVs can occur.
Risers can be capped prior to the BC boxes and pressurised from the outdoor unit service valve connections.
Pressure for overnight testing to 100 psi using dry nitrogen.
A final system pressure test of 500 psi using dry nitrogen held for 24 hours is required to prove complete system tightness prior
to evacuation. The results
must
be noted.
05. EFFECTIVE EVACUATION TECHNIQUES
• Effective evacuation technique at time of installation is a primary contributor to the long and trouble-free operation of
a refrigerant system. The downstream effects of moisture in a system can vary and include valve blockages, high head
pressures, oil sludging to copper plating of compressor internal parts and eventual compressor failures.
• Triple Evacuation Method must be used when evacuating the system prior to commissioning. The vacuum values reached at
each stage of evacuation
must
be noted on the pre-commissioning sheet contained in this booklet.
• Both the initial and second evacuation must be carried out with the schraedar valve cores removed. This allows the vacuum
pump to work more effectively at removing any moisture, and allows the dry nitrogen purges to be released quicker. Core
removal tools and vacuum charge valves are available, and allow the cores to be removed on the final evacuation.
• A check valve must be fitted to the vacuum pump to prevent the vacuum pump oil being sucked into the City Multi system if
the power is removed from the vacuum pump.
NOTE: Most vacuum pump oil is mineral-based and this is incompatible with the synthetic-based oil in the City Multi system.
Summary of Contents for BDT CITY MULTI
Page 41: ...41 S SERIES OUTDOOR UNIT WIRING INPUTS AND OUTPUTS CITY MULTI ONLY ...
Page 42: ...42 INDOOR UNIT WIRING INPUTS AND OUTPUTS CITY MULTI ONLY INPUTS AND OUTPUTS Continued ...
Page 44: ...44 RECOMMENDED M NET WIRING PROCEDURE CABLE LIMITATIONS AND SYSTEM EXAMPLES ...
Page 47: ...47 ...
Page 48: ...48 BASIC SYSTEM M NET WIRING AND ADDRESSING EXAMPLE M NET ADDRESSING Continued ...
Page 63: ...63 DIP SWITCHES INDOOR UNITS ...