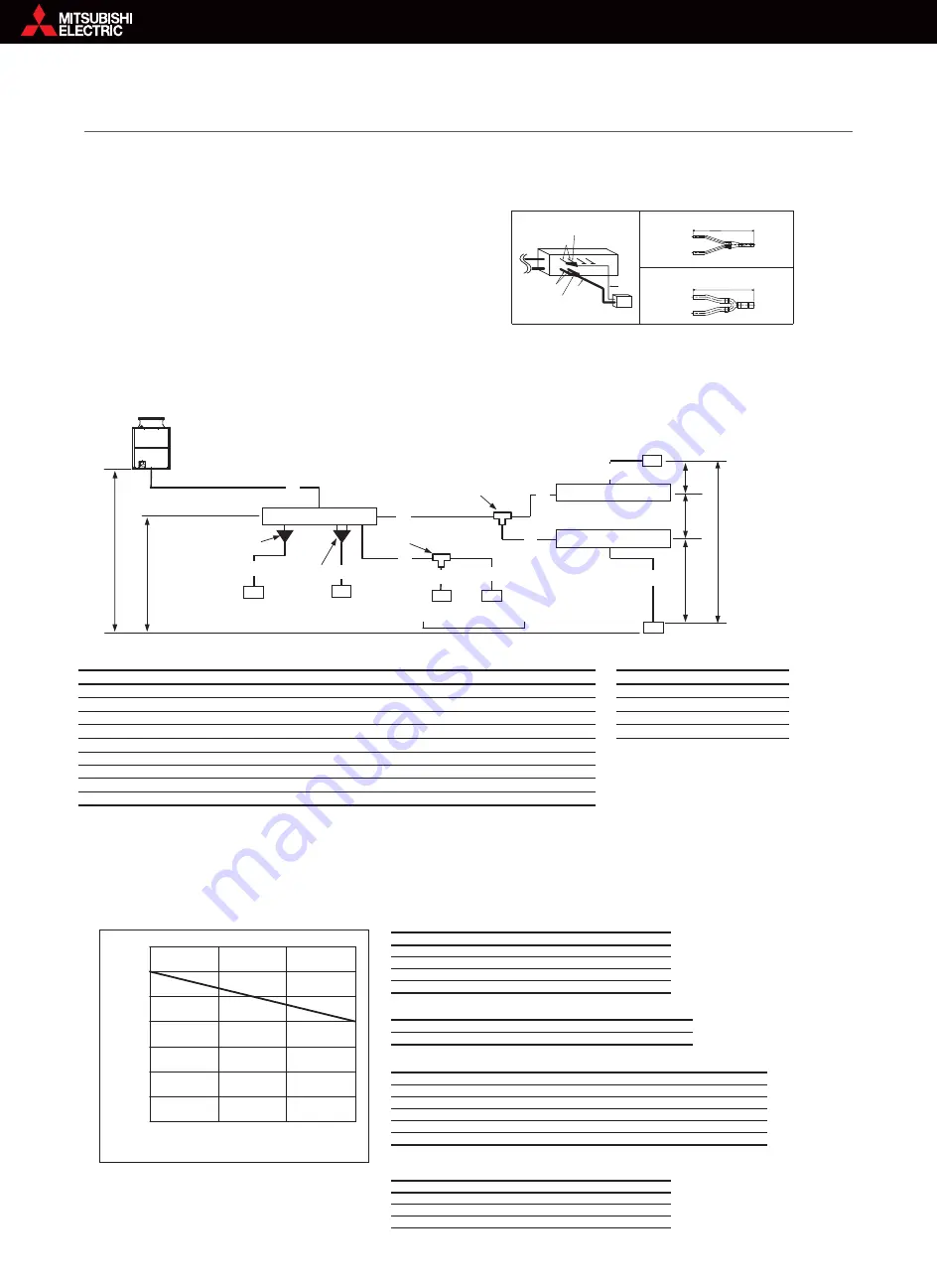
16
R2 SERIES PIPING LIMITATIONS (Continued)
3-2-3. If more than 16 ports are in use, or if there is more than one BC controller in use for one outdoor unit
Table
3-2-2-1
. Piping length limitation
(m [ft.])
Table3-2-2-2. Bent equivalent length "M"
Item
Piping in the figure
Max. length
Max. equivalent length
Outdoor Model M (m/bent [ft./bent])
Total piping length
A+B+C+D+E+a+b+c+d+e+f
*1
-
P200YLM
0.35 [1.15']
Farthest IU from OU
A+C+E+f
165 [541']
190 [623']
P250YLM
0.42 [1.38']
Distance between OU and BC
A
110 [360'] *1
110 [360'] *1
P300YLM
P350YLM
0.42 [1.38']
Farthest IU from BC controller
B+d or C+D+e or C+E+f
40 [131'] *2*3
40 [131'] *2*3
0.47 [1.54']
Heignt between OU and IU (OU above IU)
H
50 [164'] *6
-
Heignt between OU and IU (OU under IU)
H'
40 [131'] *7
-
Height between IU and BC
h1
15 [49'] (10 [32']) *4
-
Height between IU and IU
h2
15 [49'] (10 [32']) *4
-
Heignt between BC(Main or Sub) and BC(Sub) h3
15 [49'] (10 [32']) *5
-
Fig. 3-2-2-1 Piping length and height between IU and BC controller
Table3-2-2-3. Piping "A"size selection rule
(mm [in.])
Outdoor Model Pipe(High pressure) Pipe(Low pressure)
P200YLM
ø15.88 [5/8"]
ø19.05 [3/4"]
P250YLM
ø19.05 [3/4"]
ø22.20 [7/8"]
P300YLM
P350YLM
ø19.05 [3/4"]
ø22.20 [7/8"]
ø19.05 [3/4"]
ø28.58 [1-1/8"]
Table3-2-2-4. Piping "B" size seleciton rule
(mm [in.])
Total down-stream Indoor capacity
Pipe(Liquid)
Pipe(Gas)
]"
8
/
5
[
8
8
.
5
1
ø
]"
8
/
3
[
2
5
.
9
ø
s
s
e
l
r
o
0
4
1
P
Table3-2-2-5
. Piping "C", "D", "E" size selection rule
(mm [in.])
Total down-stream Indoor capacity
Pipe(Lequid) Pipe(HP Gas)
Pipe(LP Gas)
P200 or less
ø9.52 [3/8"]
ø15.88 [5/8"]
ø19.05 [3/4"]
P201 to P300
ø9.52 [3/8"]
ø19.05 [3/4"]
ø22.20 [7/8"]
P301 to P350
ø12.70 [1/2"] ø19.05 [3/4"]
ø28.58 [1-1/8"]
P351 to P400
ø12.70 [1/2"] ø22.20 [7/8"]
ø28.58 [1-1/8"]
P401 to P450
ø15.88 [5/8"] ø22.20 [7/8"]
ø28.58 [1-1/8"]
HP : High pressure, LP:Low pressure
Table3-2-2-6
. Piping "a", "b", "c", "d", "e", "f" saize selection rule (mm [in.])
Indoor Unit size
Pipe(Lequid) Pipe(Gas)
P15 to P50, GUF-50RD(H)
ø6.35 [1/4"]
ø12.70 [1/2"]
P63 to P140, GUF-100RD(H)
ø9.52 [3/8"]
ø15.88 [5/8"]
P200
ø9.52 [3/8"]
ø19.05 [3/4"]
P250
ø9.52 [3/8"]
ø22.20 [7/8"]
OU : Outdoor Unit ; IU : Indoor Unit ; BC : BC controller
*1. Refer to the section 3-2-7.
*2. Details refer to Fig.3-2-2-1
*3. Farthest Indoor from BC controller "B+d or C+D+e or C+E+f " can exceed 40m till 60m if no Indoor sized P200, P250 connected.
Details refer to Fig.3-2-2-1
*4. Distance of Indoor sized P200, P250 from BC must be less than 10m, if any.
*5. When using 2 Sub BC controllers, max. height "h3" should be considered.
*7. 60m is available depending on the model and installation conditions. For more detailed information, contact your local distributor.
*6. 90m is available depending on the model and installation conditions. For more detailed information, contact your local distributor.
0
10
20
30
40
50
60
70
0
5
10
15
Height difference between the main BC controller
and indoor unit (m)
Note1. No Header usable on PURY system.
Note2. Indoor unit sized P100-P250 should be connected to BC controller via Y shape joint CMY-R160-J1 ;
Note3. Indoor unit sized P100-P250 does NOT share BC controller ports with other Indoor units ;
Note4. As bends cause pressure loss on transportation of refrigerant, fewer bends design is better ;
Piping length needs to consider the actual length and equivalent length which bends are counted.
Equivalent piping length (m)=Actual piping "M" x Number of bends.
However, the cooling capacity decreases a little (For details, refer to the chapter OUTDOOR UNITS,
R2 SERIES, 6-4. Correction by port counts of the BC controller).
Note5. Set DIP-SW 4-6 to ON of BC controller, in case of connected Indoor unit sized P100-P140 with 2 ports.
Note6. It is also possible to connect Indoor unit sized P100-P140 with 1 port (set DIP-SW 4-6 to OFF).
Note7. Individual indoor units grouped together to connect to the BC controller via one port cannot operate individually
in heating and cooling modes at the same time. I.e., they must all function in either heating or cooling together.
Note8. For sub BC controller CMB-P
•
V-GB1 the connectable indoor unit capacities may sum to equal that of a
P350 unit or less. However, if two sub controllers are used the TOTAL sum of connectable units
connected to BOTH sub controllers must also not exceed that of a P350 unit.
For sub BC controller CMB-P1016V-HB1 the connectable indoor unit capacities may sum to equal that
or a P350 unit or less. However, if two sub controllers are used the TOTAL sum of connectable units
connected to BOTH sub controllers must also not exceed that of a P450 unit.
Note9. Indoor capactiy is described as its model size. For example, PEFY-P63VMA-E, its capacity is P63.
Note10. Total down-stream Indoor capacity is the summary of the model size of Indoors down-stream.
Note11. To enable the continuous heating mode, set SW4 (848) to ON.
For example, PEFY-P63VMA-E + PEFY-P32VMA-E : Total Indoor capacity = P63 + P32 = P95.
S
T
M
N
CMY-R160-J1
(Gas side)
IU
CMY-R160-J1
(Liquid side)
BC controller
Fig. 3-2-2AA
BC controller (Main BC)
IU
a
IU
C
b
H
H'
h1
h1
IU
(P15-P80)
(P100-P250)
CMY-R160-J1
(Joint)
IU
CMY-Y102SS-G
(Joint)
Max.3 sets for 1 port.
Total capacity < = P80
BC controller (Sub BC)
BC controller (Sub BC)
B
c
d
IU
f
h3
D
E
CMY-Y202S-G2
CMY-Y102LS-G2
CMY-Y102SS-G2
(Joint)
A
IU
e
h1
OU : Outdoor unit, IU : Indoor unit
OU
Reducer (P15-P50)
(attached with BC controller)
h2
Fig. 3-2-2A Piping scheme
(T)ø19.05ID
(N)ø9.52ID
(M)ø3/8"(Brazing)
(M)ø3/8"(Brazing)
(S)ø5/8"(Brazing)
(S)ø5/8"(Brazing)
226
226
Joint CMY-R160-J1 Gas side
Joint CMY-R160-J1 Liquid side
Pipe
length
between
the
main
B
C
controller
and
indoor
unit
(m
)
PURY-P-YLM
Summary of Contents for BDT CITY MULTI
Page 41: ...41 S SERIES OUTDOOR UNIT WIRING INPUTS AND OUTPUTS CITY MULTI ONLY ...
Page 42: ...42 INDOOR UNIT WIRING INPUTS AND OUTPUTS CITY MULTI ONLY INPUTS AND OUTPUTS Continued ...
Page 44: ...44 RECOMMENDED M NET WIRING PROCEDURE CABLE LIMITATIONS AND SYSTEM EXAMPLES ...
Page 47: ...47 ...
Page 48: ...48 BASIC SYSTEM M NET WIRING AND ADDRESSING EXAMPLE M NET ADDRESSING Continued ...
Page 63: ...63 DIP SWITCHES INDOOR UNITS ...