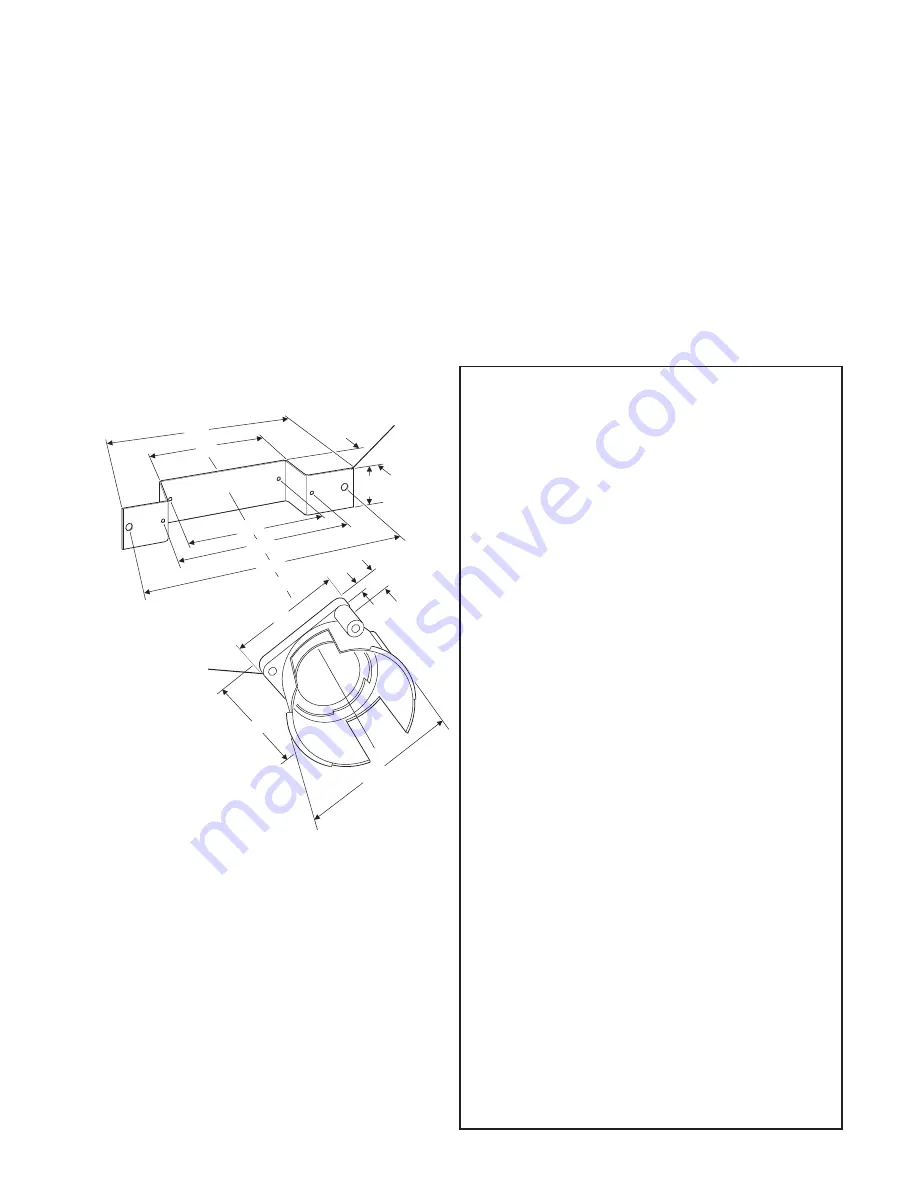
25
Shower Cubicle or Laminated Panel
The built-in shower control incorporates an integral wall mounting bracket assembly
which can be used to install the shower into the front or back face of a shower cubicle
or laminated panel.
Installation on to the Front Face of a Shower Cubicle or Laminated
Panel
Depending on the structure of the shower cubicle or laminated panel it may be possible
to conceal the flanges of the integral wall mounting bracket assembly into the front face
of the wall surface then cover over the fixings with plaster and tiles. The building-in depth
for the integral wall mounting bracket assembly is
58 mm
. The thickness of plaster and
tiles which conceal the integral wall mounting bracket assembly flanges must be between
6
and
23 mm
.
230
134
110
146
214
53
43
67
92 A/F
12
38
Wall
Mounting
Bracket
Backplate
Ø101
1.
Follow the shower control installation
procedure as for
“Solid, Dry-lined,
Stud partition or Dry Partition Wall
Structures”: instructions 1.
to
4.
inclusive.
2.
Cut a circular hole in the panel measuring
145 mm
in diameter.
3.
Follow the shower control installation
procedure as for
“Solid, Dry-lined,
Stud Partition or Dry Partition Wall
Structures”: instructions 6.
to
18.
inclusive to complete the installation.
Summary of Contents for Combiforce 415
Page 51: ...51 Appendix Notes ...