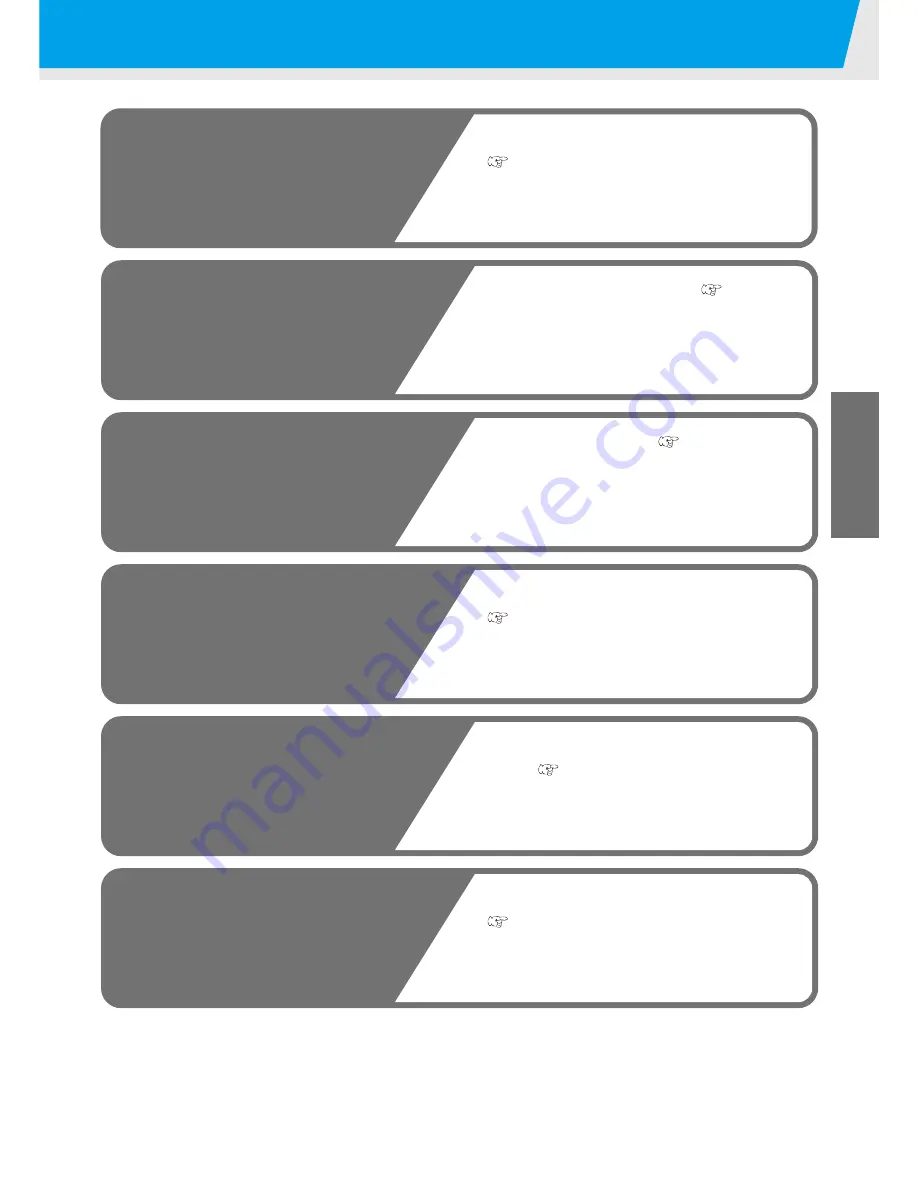
2-3
2
Basic Operations
Operation flow
1
Turning the power ON
2
Setting the media
3
Test drawing
4
Execution of head
cleaning
5
Drawing an image from
source data
6
Turning the power OFF
See "Turning the power ON"
(
P.2-4)
See "Setting the media" (
P.2-5)
See "Test drawing" (
P.2-9)
See "Execution of head cleaning"
(
P.2-10)
See "Drawing an image from source
data" (
P.2-12)
See "Turning the power OFF"
(
P.2-15)
Summary of Contents for JF-1610
Page 32: ...1 14...
Page 48: ...2 16...
Page 68: ...3 20...
Page 128: ...6 6...
Page 140: ...6 18...
Page 141: ...D201645 20 29082008...
Page 142: ...NH FW 2 80 Printed in Japan MIMAKI ENGINEERING CO LTD 2008...