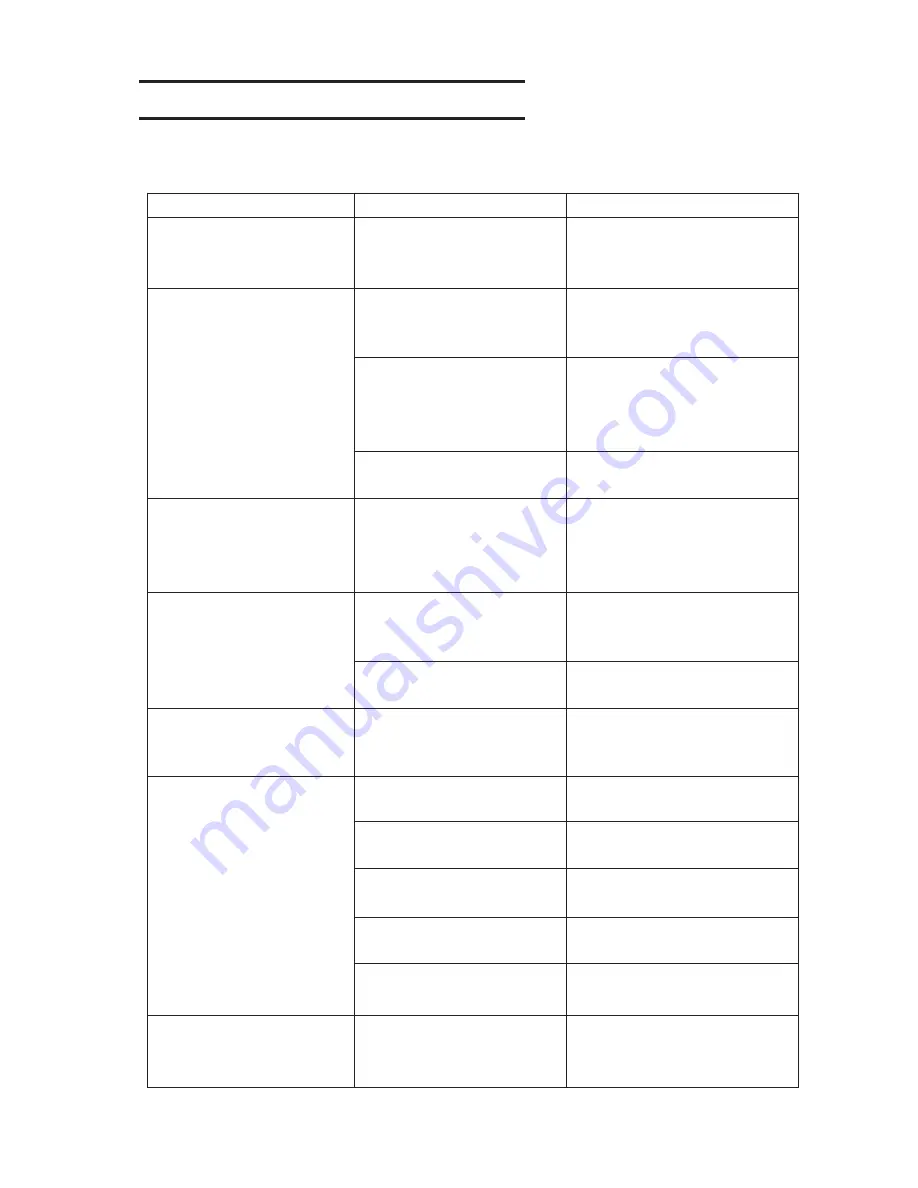
– 4.2 –
Before taking a phenomenon as a trouble
Take appropriate remedies referring to the phenomena described below.
If still the problem cannot be solved, contact us or the dealer.
Cannot turn on the power.
The power supply plug is not
connected firmly.
Connect the power supply cable
between the plotter and the plug
outlet firmly.
The device cannot perform
cutting (protting).
The plotter name specified
on the host computer is
wrong.
Check up the plotter name
specified on the host computer.
The interface cable is not
securely connected to the
device and/or the host com-
puter.
Securely connect the interface
cable.
USB driver has not been
installed.
Install USB driver supplied with
FineCut.
A communication error
arises in prior to receiving
data.
The power to the device and
that to the host computer
have been turned on in
wrong order.
Turn on the power to the host
computer first. Then, turn on
the power to the device.
An error arises on the
device when the host
computer sends data to the
device.
Communication conditions
have not been properly
established.
Check up the communication
conditions.
A wrong operation has been
executed.
Execute the correct operation.
The device cannot detect a
sheet. [** NO SHEET **]
A transparent sheet or a
sheet of which wrong side is
black is used.
Set the sheet sensor function to
OFF.
The device performs cut-
ting to produce broken
lines.
Screw in the tool holder has
loosened.
Tighten the screw.
The blade of the cutter
protrudes excessively.
Adjust the protruding amount of
the blade adequately.
Is the tool condition set to
[HLF].
Set the tool condition to
[CT1]~[CT5].
The blade is chipped or has
worn out.
Replace the blade with a new
one.
Difficulty in turning the blade
tip.
Exchange to a new holder.
Phenomenon
Cause
Remedy
The data length and the
actual cut length differ.
Because of the sheet feeding
length difference according
to the sheet thickness in use.
Correct the error margins by ex-
ecuting the distance compensation
function. ( Refer to Page 3.9 )
Summary of Contents for CG-130FXII
Page 2: ......
Page 16: ...xiv...
Page 150: ...5 14 D201812 12 26112011...
Page 151: ......
Page 152: ...D201812 MIMAKI ENGINEERING CO LTD TM FW 3 00...