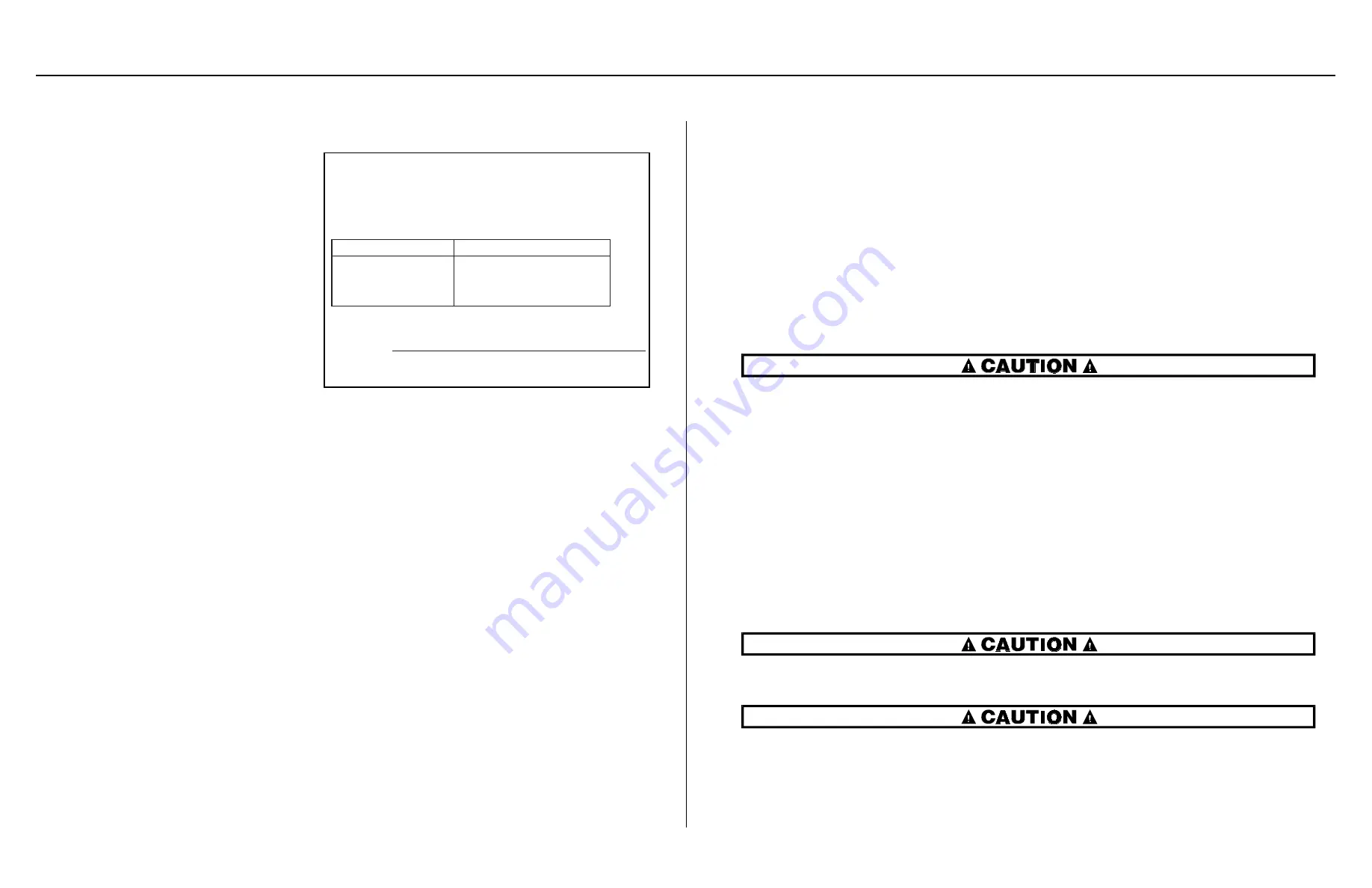
Ê
Piped Inlet Precautions
Machines are supplied with one to three air op-
erated ball valves (functions and positions are shown
in FIGURES 2 through 8). The flow rate of a ball
valve is far greater than that of a globe valve of equal
nominal size. Do not use improperly sized globe type
shut-off valves in front of ball valves (see FIGURE
11). Additional precautions are as follows:
•
Always use unions at the point of connection to
permit removal of the valve assembly for serv-
ice.
•
Do not connect reuse water to any other inlet.
Reuse water has a detrimental effect on devices
(e.g., supply injector) supplied by other inlets.
•
Do not use globe type shut-off valves on reuse
water. Reuse water lint may clog this type of
valve.
•
Inlet valves may experience “water hammer” at higher water pressures. Inlet valve actuators (air cylinders) are
fitted with needle valves to adjust how fast the inlet valve closes. If water hammer is experienced, slightly
reduce the closing rate of the inlet valve. Pressure regulators or shock absorbers may be necessary.
Ë
Steam Requirements
—Steam inlets are located near water inlet valves (except Staph-Guard
®
models). Size
the line from the header to the machine at least one size larger than the steam valve.
Ê
Flushing Water for Supply Injector
NOTE : Tilting, 42", 48", and 64" open pocket machines fitted with flushing supply injectors have an internal
connection to the hot (or cold, if hot is not available) water inlet.
Divided cylinder, 52", and 72" open pocket non-tilting machines require an external connection. Supply injec-
tors require a dependable hot water supply that does not boil over or contain steam. Use cold water if the hot water
supply does not meet the above conditions.
•
Connect directly from water supply to the supply injector water pressure reducing valve.
•
Use at least one size larger pipe than the water pressure reducing valve.
•
Verify a reading of 28 PSI (1.96 kilograms per square centimeter) on the water pressure gauge. This pressure
protects the downstream supply injector solenoid valves. These valves are rated for a maximum static pres-
sure of 30 PSI (2.10 kilograms per square centimeter). Pressures above this may cause the valve coils to
burn out.
•
If the water pressure reducing valve “chatters” while flushing, verify gauge pressure is 28 PSI. If pressure is
correct then re-locate the water pressure reducing valve approximately 10 feet further upstream.
•
Tubing connection in the top of the pressure reducing valve is a “bleed - off” line and normally discharges into
the supply injector, but can be connected to any convenient drain.
Ë
Optional Cooldown Water Connection
—Open pocket tilting and non-tilting machines that use cool-
down are internally connected to the cold water connection and do not require external connection. Divided cylinder
machines require a separate cold water connection.
Ë
Optional Spray down Water Connection
— Rapid load machines use a separate cold water connec-
tion. A machine equipped for both cooldown and spray down uses one inlet for both functions.
Ë
Liquid Supplies
—Machines equipped with the optional central liquid supply injection in lieu of a flushing
supply have a set of supply valves and a supply manifold.
Never connect hard piping directly to the drain valve outlet.
☞
Drain valves are connected to the suspended portion of the machine, and move up to 3"
in any direction when the machine is operating, and up to 18" along an arc in the case
of tilting machines.
Ë
Drains
—Depending upon whether single or dual drain valves are supplied, the installation should provide for a
single or double recessed trench under the machine, as shown on the dimensional drawing, in order to accommodate
the rapid, large volume outfall which occurs when the drain opens. When dual drain valves are furnished (for water
reuse) the drain-to-sewer is located to the front and the drain-to-reuse, to the rear, unless specified otherwise. These
positions are easily swapped by interchanging the air lines on top of each drain valve air cylinder. Never make
changes to electrical circuits. A short length of flexible hose may be attached to drain valves on non-tilting machines
to control splashing, especially if the drain valve is not centered over the trench. Connecting this flexible hose
directly to hard drain piping is not recommended as this may be too restrictive to allow complete draining. If this is
necessary, the drain valve may in most cases be mounted with the drain outlet facing rearward or forward, to
facilitate the routing of drain piping. Consult Milnor
®
for further information.
Do not connect a powered ventilator to a Staph - Guard
®
as this may defeat the internal
venting mechanism. Consult Milnor
®
for additional information.
The shell vent outlet on tilting machines moves when tilting. Rigid vent connections cannot
be made to tilting machines. Consult Milnor
®
if extenuating circumstances require external
venting.
WARNING
Some of the water inlet and/or steam valves on this machine may
be of the "ball valve" construction. The flow rate of a ball type valve
is far greater than that of an equal size globe valve.
DO NOT USE GLOBE TYPE SHUT OFF VALVES IN FRONT OF
BALL VALVES UNLESS THE GLOBE VALVE IS SELECTED IN
ACCORDANCE WITH THE FOLLOWING TABLE:
BALL VALVE SIZE EQUIVALENT GLOBE VALVE SIZE
1- 1/4" normal flow
1- 1/2" normal flow
2" normal flow
*
2" full port fast flow
2-1/2"
2-1/2"
3"
4"
*
Used as water inlet valves on MILNOR 7244 machines.
NOTICE: IF VALVE IS ACCIDENTLY PIPED TO THE WRONG WATER
LINE, MERELY INTERCHANGE THE AIR TUBE (IF VALVE IS AIR-
OPERATED). NEVER INTERCHANGE ANY ELECTRICAL CONNECTIONS
(NOT APPLICABLE FOR THIS MACHINE ON WHICH A SINGLE
CONNECTION SERVES MORE THAN ONE WATER-USING DEVICE.)
Î
FIGURE 11
(MSIN0201BE)
Î
All Hydro-Cushion
®
Machines
39
Summary of Contents for 42044SR2
Page 2: ......
Page 4: ......
Page 8: ......
Page 9: ...Installation 1 5 ...
Page 37: ...Î FIGURE 8 MSIN0301AE Î Vibration Switch Î FIGURE 9 MSIN0301AE Î 60 Staph Guard 33 ...
Page 51: ...586DA4 BUecU CicdU CSXU QdYS B5EC5 D1 9 CD1 1D9 1 4 5B1D9 C9 1 15 1F _V 47 ...
Page 53: ...Dimensional Drawings 2 49 ...
Page 54: ......
Page 55: ...51 ...
Page 56: ...52 ...
Page 57: ...53 ...
Page 58: ...54 ...
Page 59: ...55 ...
Page 60: ...56 ...
Page 61: ...57 ...
Page 62: ...58 ...
Page 63: ...59 ...
Page 64: ......
Page 65: ...61 ...
Page 66: ...62 ...
Page 67: ...63 ...
Page 68: ...64 ...