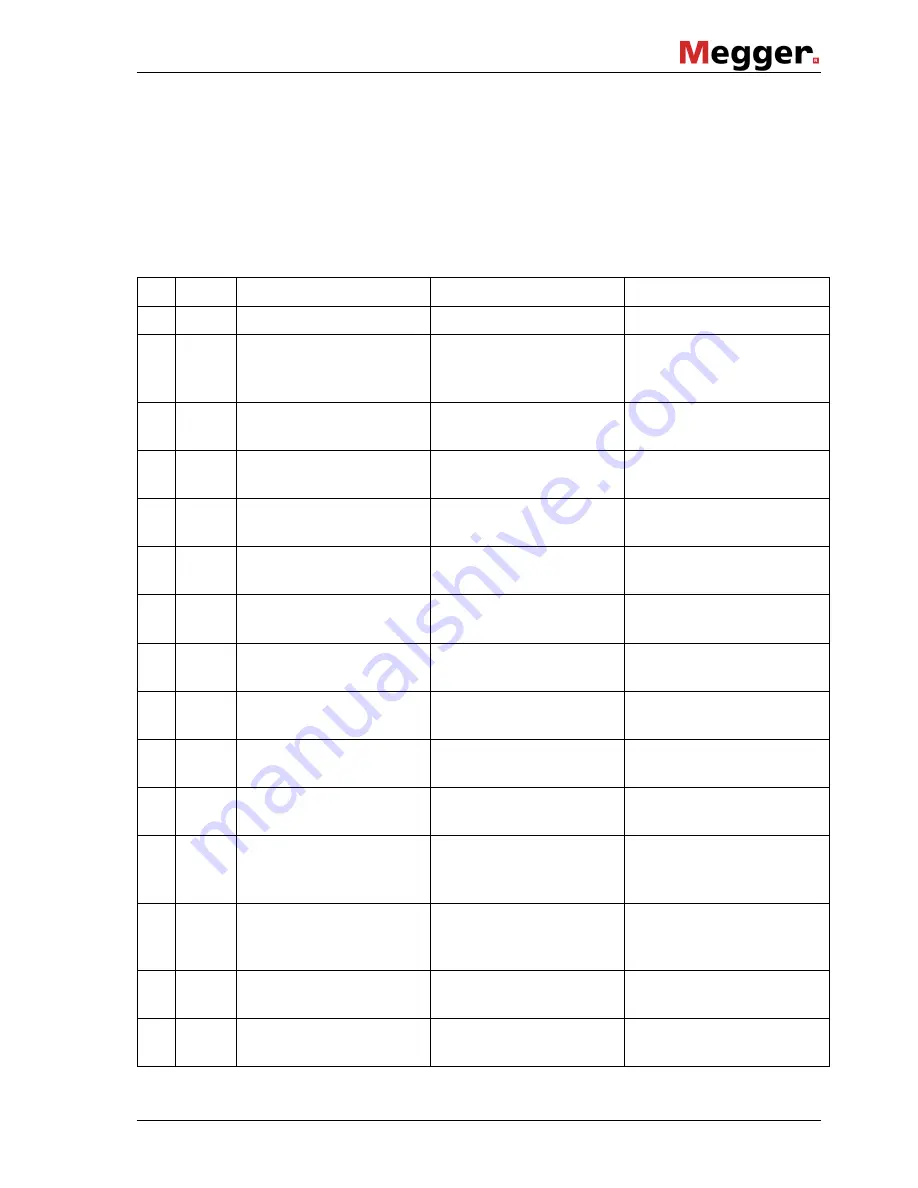
7-59
7.5.2 Operational Messages about State of System
The following operational messages inform the operator about the current state of the
system.
You don´t need to confirm any of them. The system, however, expects the operator to
make one of the entries listed in the table.
Code
Cl.
Operational message Description
Input
- -
[ Start-up screen]
System is starting up.
none
- U
Connecting...
System is connecting
Master and Slave
processors.
none
- U
Initiating system
System is initializing
parameters etc.
none
- U
Remove any card !
No card must be plug-
ged in during start-up.
none
pull out
card !
- U
Ready. OK:Start
System is ready for
starting a test.
OK
(or to
Setup)
- U
By card. OK:Start
System is ready for
starting a test.
OK
(or to
Setup
- U
Stopped. OK:Start
System is ready for
starting a test.
OK
(or to
Setup)
- U
Select mode OK?
System is waiting for
input of mode.
rotary knob + OK
- U
Set voltage OK?
System is waiting for
input of test voltage.
rotary knob + OK
- U
Set test time OK?
System is waiting for
input of test time.
rotary knob + OK
- U
Set pulsing OK?
System is waiting for
input of pulsing rate.
rotary knob + OK
- U
Insert SystemCard
System is waiting for a
system card to be
inserted.
none
insert
card !
- U
Without card only
Operation mode can
only be performed
without system card
none
pull out
card !
- U
Card is invalid !
System card not
readable or invalid.
none
pull out
card !
- U
Card is full !
System card is full.
none
pull out
card !
Summary of Contents for TDS40
Page 2: ......
Page 19: ...2 19 2 6 Testable Cable Capacitance in VLF Mode...
Page 20: ...2 20 2 7 Cable Capacitance that Can be Diagnosed in DAC Mode TDS40 TDS60...
Page 26: ......
Page 32: ......