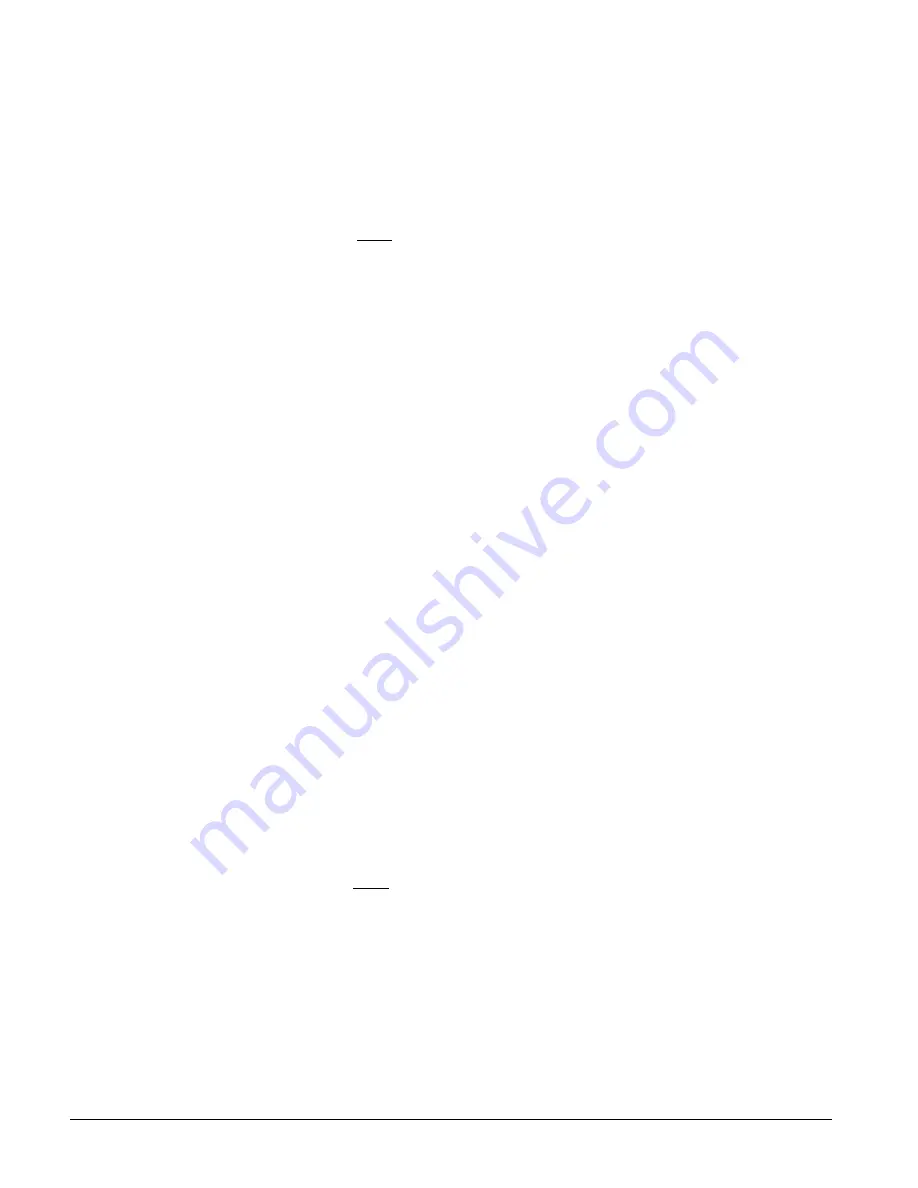
62
AGZ 026B through 130B
IOMM AGZ-5
Required Parameters
•
Number of starts for all compressors
•
Number of run-hours for all compressors
•
Status of all compressors (Available/Unavailable)
•
Compressor number
Compressor Start/Stop Timing-Cool Mode
This section defines when a compressor is to start, or stop, and the scenario for doing
so.
Required Parameters
1. Start Delta setpoint.
2. Max Pulldown Rate setpoint
3. Evap Delta T setpoint
4. Number of Compressors/Circuit setpoint
5. LWT
error
6. LWT
Slope
7. Number of compressors running
8. Interstage timer status
Stage Up
For 2 compressors/circuit:
Control band = Evap Delta T x .25
For 3 compressors/circuit:
Control band = Evap Delta T x .17
IF
[LWT Error > Startup_Delt 0.5(Control band)
AND No Compressors Running
AND Stage Up Timer Expired]
THEN
Stage_Up_Now = YES
ELSE IF
[LWT Error > 0.5(Control band) AND LWT Slope <= Max Pulldown setpoint
AND Stage Up Timer Expired]
THEN
Stage_Up_Now = YES
Stage Down
IF
[LWT Error < -0.5(Control band)
AND Stage Down Timer Expires
]
THEN
Stage_Down_Now = YES
Compressor Start/Stop Timing – Ice Mode
This section defines when a compressor is to start, or stop, and the scenario for doing
so.
Required Parameters
Start Delta setpoint
Evap Delta T setpoint
Number of Compressors/Circuit setpoint
LWT error
Number of compressors running
Interstage timer status
Ice timer status (12 hours between starts)
Summary of Contents for AGZ026BS
Page 103: ...IOMM AGZ 5 AGZ 026B through 130B 103...
Page 104: ...104 AGZ 026B through 130B IOMM AGZ 5...
Page 105: ......