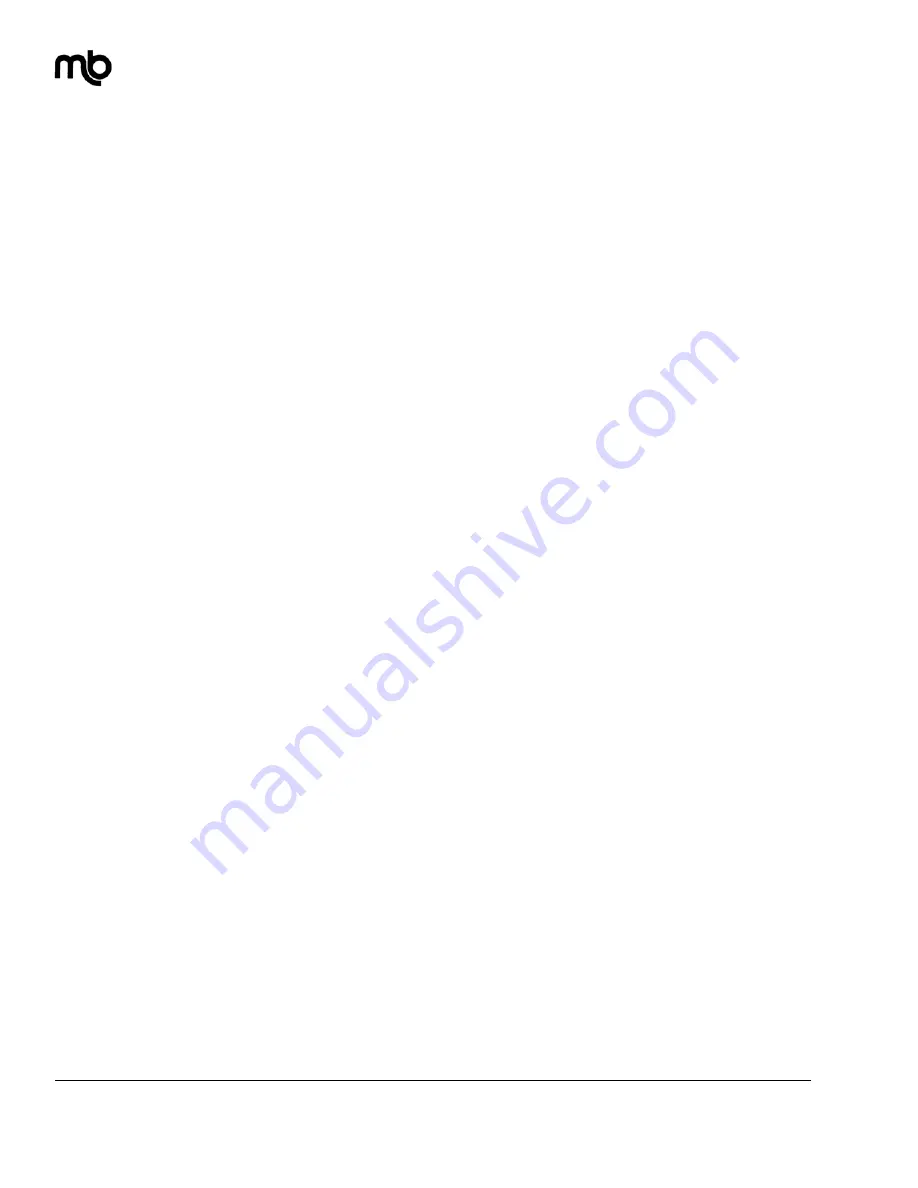
M-B Multi-Service Vehicle
Page 3.20
Vehicle Information
© 2008 M-B Companies Inc.
All Rights Reserved
CAN Network
A Controller Area Network (CAN) is used on the M-B Multi Service
Vehicle to control all hydraulic and engine functions. The CAN is
designed with software switches that compliment other switches and
the joystick. Together, this system activates electric solenoids that
control hydraulic valves. The main interface to the system is the
Monitor Diagnose Control (MDC).
Circuit Breakers
The electrical system is protected by circuit breakers of various sizes
located in the rear control panel in the engine enclosure.
In compliance with engine manufacturer’s requirements, the power
supply for electronic control modules is protected by a fuse pack.
These fuses will be located in the Cab Subpanel.
Attachment Controls
All attachment hydraulic functions, PTO engagement, and some
vehicle control selections are controlled by the MDC and joystick.
Speed Controls
Vehicle controls include the engine throttle and a foot pedal. Each of
these are set using the MDC screens and the joystick to deliver a
controlled variable voltage to an actuator.
Engine speed is controlled by an electronic control module provided by
the engine manufacturer. The operator in the cab uses MDC screens
and joystick which are networked to the Electronic Control Module
(ECM) to set desired engine operating speed.
The auxiliary hydraulic flow rate is controlled from the operators
position in the cab by means of the MDC. The ground drive speed is
controlled by means of the foot pedal. A variable current is delivered to
an electronic displacement control (EDC) on each hydraulic pump for
the particular function. The variable current determines the angle of the
pump swash plate which in turn determines pump displacement.
Wiring
Wiring in the system is color and number coded for ease of tracing,
maintenance, and troubleshooting.
Summary of Contents for Multi-Service Vehicle
Page 2: ...5 19 10 PN 904 154502 ...