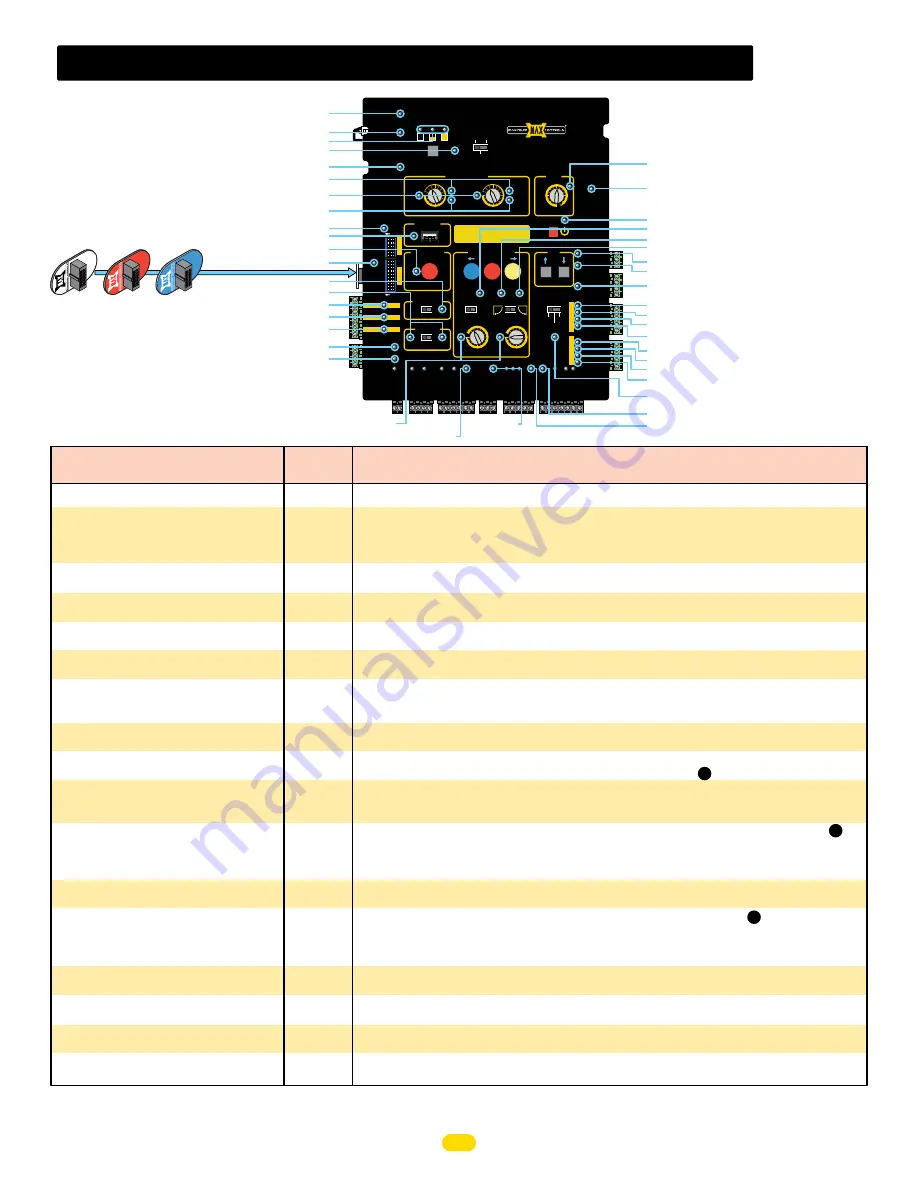
EXIT PWR
ALARM
POWER /
SOLAR IN
BATTERY
INPUT
OPENING
CLOSING
CLOSING
OPENING
ERD
OBD PORT
BLACK BOX
PROGRAMMING
SOLAR MODE
PROGRAM
MOTOR
OVER
LOAD
ERD
MOTOR
OVER
LOAD
MAX
OFF
MAX
SENSE
MAX
SENSE
BATTERY
BACKUP MODE
ERD SENSITIVITY
MOTION CONTROL
OPEN
GATE SPEED
MAG
LOCK
UL
ENTRAP
PRIMARY/
SECONDARY
LINK
STOP
CLOSE
MOTOR
INPUTS
CLOSE
TIMER
MAGLOCK
DELAY
JOG
BATTERY
TEST
INPUT
ERROR
BATTERY
BATTERY
IN USE
REPLACE
BATTERY
LEAVE
CLOSED
LEAVE
OPEN
OPEN
1 TIME
BATTERY VOLTAGE
E
F
1/2
RESET /
MANUAL
RELEASE
ID
PLUG
LINK
OK
MODULE
PORT
MOTOR
POSITION
INPUTS
SLIDER
LIMIT
SWING
LIMIT
GND
OPEN ONLY
NC
OPEN ONLY
10K
PHOTO CLS
NC
OPEN/CLS
NC
GND
12VDC OUT
GND
GND
GND
GND
GND
GND
JOG RIGHT
JOG LEFT
TAMPER IN
TAMPER NO
GATE DISABLE
MANUAL RELEASE
KEYPAD / CARD
GND
(-)
(+)
GND
GND
MAX OPEN
FIRE DEPT
RADIO GND
RADIO SIGNAL
STRIKE
CLOSE
COM
COM
STOP
OPEN
CLS ONLY
10K
OPEN/CLS
10K
12VDC OUT
NO
COM
NC
ID PLUG
ERROR
24VDC OUTPUT
12VDC OUTPUT
GND
GND
GND
LOOP PWR
OFF
PRIMARY
LEFT
ON/OFF
BATTERY
RIGHT
SECONDARY
ON
QUICK
CLOSE
OPEN
LEFT
OPEN
RIGHT
GATE
OFF
1
2
3
4
5
6
7
8
9
10
1
2
3
4
5
6
MIN
MIN
MAX
MAX
ON
OFF
2.5 sec
1.5 sec
FAULTS
OPERATOR
MATRIX III
OFF
OFF
3
1
14
16
MIN
16
MIN
12
9
7
3
1
14
12
9
7
UL SENSOR N.C.
UL SENSOR 10K
POWER
MODE A
MODE B
EXIT
LOOP
LOOP
LOOP
CENTER
SAFETY
GATE OPEN
COM
GATE CLOSED
MIN
MATRIX III
SWING / SLIDE
matrix III led troubleshooting
Table continued on next page
12.
ID PLUG ERROR
15.
EXIT LOOP
14.
PRIMARY/SECONDARY
13.
SOLAR MODE
5.
POWER
6.
ERD
7.
MAX SENSE
8.
MOTOR OVERLOAD
9.
MANUAL RELEASE/RESET
20.
CLOSE TIMER
21.
SLIDER LIMIT
22.
ON/OFF BATTERY
23.
QUICK CLOSE
24.
OPEN LEFT
25.
OPEN RIGHT
26.
GATE OPEN
27.
GATE CLOSED
29.
OPEN ONLY NC
30.
PHOTO CLOSE NC
31.
OPEN / CLOSE NC
32.
12VDC OUT
28.
MAGLOCK
10.
OBD PORT
11.
PROGRAM
4.
REPLACE BATTERY
3.
BATTERY VOLTAGE
2.
BATTERY IN USE
1.
BATTERY INPUT ERROR
16.
CENTER LOOP
17.
SAFETY LOOP
18.
12 VDC
19.
24 VDC
33.
OPEN ONLY 10K
34.
CLOSE ONLY 10K
35.
OPEN / CLOSE 10K
36.
12VDC OUT
37.
UL ENTRAPMENT
42.
GATE SPEED
40.
LINK OK
41.
MANUAL RELEASE
38.
GATE TAMPER
39.
GATE DISABLE
ID plug
MUST
be plugged in.
MAX
1500 PRO
MAX
2200 PRO
MAX
F18 PRO
MAX
1500
MAX 2200
MAX F18
Matrix III LED
Problem Condition
Solution(s) for
Problem Condition
Normal
LED
“BATTERY IN ERROR” LED is ON.
“BATTERY IN USE” LED is ON
“BATTERY VOLTAGE (E 1/2 F)” LEDs, only “E”
is ON.
“REPLACE BATTERY” LED is ON.
“BATTERY IN USE” and “POWER” LED are
FLASHING
PRIMARY Matrix III “LINK OK” LED is OFF
SECONDARY Matrix III “LINK OK” LED is OFF
“UL Entrap” LED is ON
“ERD” LED is FLASHING
“PHOTO CLS” LED is ON
“CLS ONLY 10K” LED is ON
“PHOTO CLS” LED is flashing
“CLS ONLY 10K” LED is flashing
“OPEN ONLY” LED is ON
“OPEN ONLY” LED is FLASHING
“MAX SENSE” LED is ON
“MANUAL RELEASE/RESET” LED is ON but
manual release is not working
“OBD PORT” LED is FLASHING
“PROGRAM” LED is FLASHING
•
“BATTERY Plug” not plugged in to “BATTERY IN” port.
•
AC power is lost, operator is in battery back-up mode.
•
Check if Toroid box AC POWER ON/OFF SWITCH is ON.
•
Measure power input DC voltage on Matrix 1 (“24V/GND” - 2-pin black connector), (expected reading
34 VDC if AC on, 25VDC if on battery back-up).
•
Battery is very LOW. Check if AC power ON/OFF switch is ON. If so, check AC power.
•
Battery needs to be replaced if BATTERY TEST fails and “REPLACE BATTERY” LED is ON.
•
Battery not plugged in to BATTERY INPUT port.
•
Check if limit sensors are plugged into PRIMARY MATRIX III “SLIDER LIMIT” input.
•
Check wiring between PRIMARY RS485 (+,-, gnd) and SECONDARY RS485 (+,-, gnd) terminals,
connect [(+) to (+)], [(-) to (-)] and [GND to GND].
•
Check if limit sensors are plugged into SECONDARY Matrix III “SLIDER LIMIT” input.
•
An entrapment event has occurred, check if an entrapment sensor was triggered (see if PHOTO CLS,
OPEN ONLY, or OPEN/CLS LEDs are on).
•
An ERD event may have occurred. Check for gate obstruction.
•
ERD sensitivity is too high for application. Re-adjust ERD setting, (see ).
•
Sensor on PHOTO CLS or CLS ONLY 10K inputs (photocell or edge) may have detected an obstruction
while closing gate.
•
Photocell on PHOTO CLS or CLS ONLY 10K inputs is misaligned with reflector.
•
Sensor on PHOTO CLS or CLS ONLY 10k inputs (photocell or edge) may not be wired properly, (see ).
•
Sensor is NOT a N.C. monitored sensor that is UL325 2018 compliant.
•
Sensor might need to be re-learned.
•
Sensor is damaged or malfunctioning.
•
Sensor on OPEN ONLY input (photocell or edge) may have detected an obstruction while cycling gate.
•
Photocell on OPEN ONLY input is misaligned with reflector.
•
Sensor on OPEN ONLY input (photocell or edge) may not be wired properly, (see ).
•
Sensor is NOT a N.C. monitored sensor that is UL325 2018 compliant.
•
Sensor on OPEN ONLY is damaged or malfunctioning.
•
Sensor might need to be re-learned.
•
MOST sensitive setting for ERD entrapment detection. Select a less sensitive setting (recommend level
10 thru 16)
•
Connected external device to MANUAL RELEASE input is not working, check wiring. replace device.
•
Up to 8000 event history and error codes are being downloaded to connected flash drive. Up to 5 min.
•
Program button has been pressed and programming mode is active. Press button again to leave
programming mode.
1
OFF
2
OFF
3
OFF
4
OFF / ON
2 / 5
ON
40
ON
40
ON
37
ON
6
OFF
30 / 34
OFF
30 / 34
OFF
29 / 33
OFF
29 / 33
OFF
7
OFF
9 / 41
OFF
10
OFF
11
8
5
5
21
UL 325 2018 Standard - MAX 1500 PRO/2200 PRO/F18 PRO Matrix III Install
Version 7a
Summary of Contents for 1500 PRO
Page 30: ...a...
Page 33: ......
Page 37: ...30 UL 325 2018 Standard MAX 1500 PRO 2200 PRO F18 PRO Matrix III Install Version 7a...
Page 38: ...31 UL 325 2018 Standard MAX 1500 PRO 2200 PRO F18 PRO Matrix III Install Version 7a...
Page 39: ...32 UL 325 2018 Standard MAX 1500 PRO 2200 PRO F18 PRO Matrix III Install Version 7a...