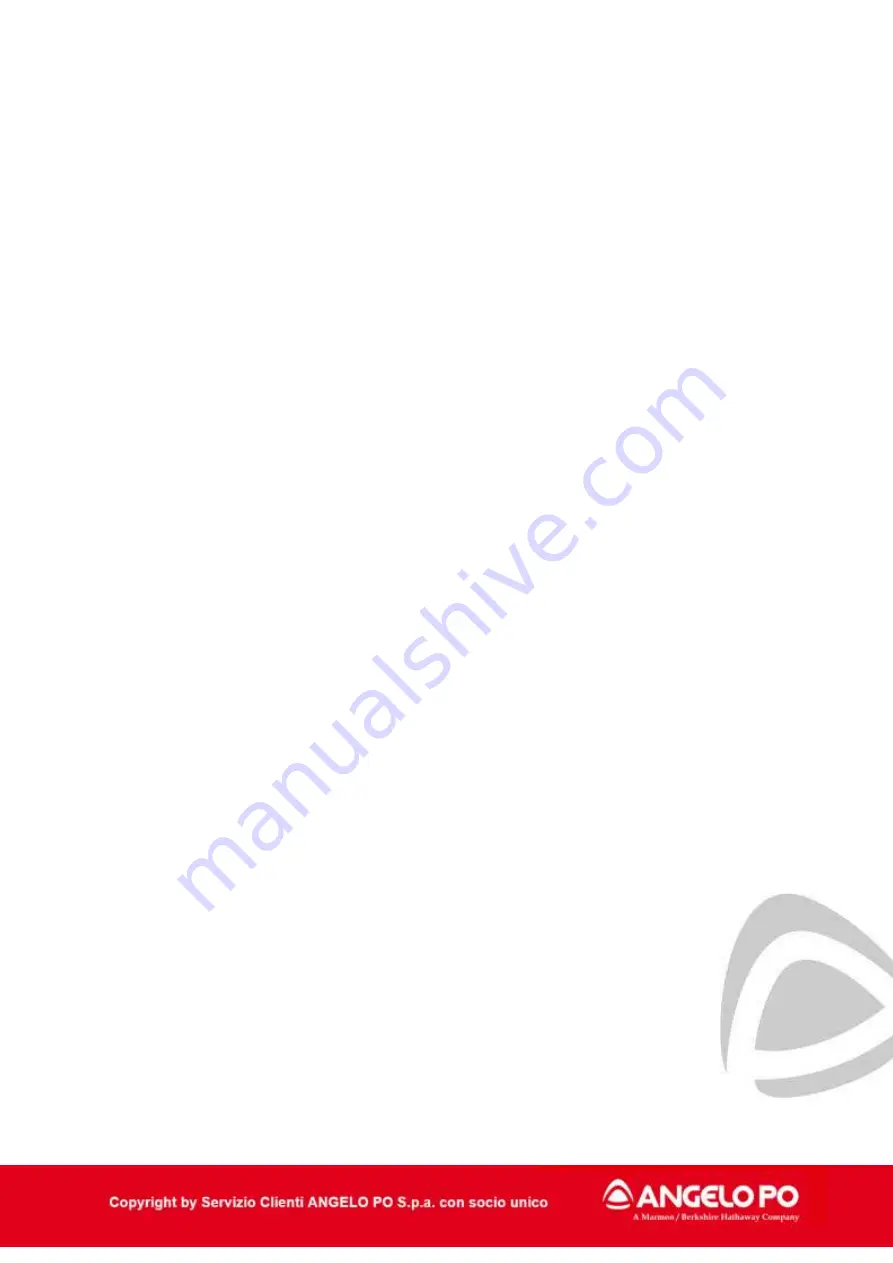
Copyright by Servizio Clienti ANGELO PO Spa
125
6.3.3.1. Rinse
-
Drain valve closure.
-
Water loading
-
Rinsing: the washing pump is activated. Before activating the pump, the cooking
chamber is pre-heated at 70°C but then the heater (heating element or heat exchanger)
is switched off during rinsing.
-
Drain valve opening and tank drain.
-
Collection tank washing: water is dispensed in the collection tank while the valve is
open to wash any residues left in the tank.
N.B. the times of the various phases can change between the 1st and 2nd rinse
6.3.3.2. Drying
-
The drying phase is carried out at 180°C.
Summary of Contents for ANGELO PO ACT.O
Page 1: ...Copyright by Servizio Clienti ANGELO PO Spa Rev 0...
Page 8: ...Copyright by Servizio Clienti ANGELO PO Spa 8 1 3 2 Gas Oven connection diagram...
Page 51: ...Copyright by Servizio Clienti ANGELO PO Spa 51...
Page 67: ...Copyright by Servizio Clienti ANGELO PO Spa 67...
Page 72: ...Copyright by Servizio Clienti ANGELO PO Spa 72...
Page 88: ...Copyright by Servizio Clienti ANGELO PO Spa 88 5 2 9 Heat exchanger...
Page 110: ...Copyright by Servizio Clienti ANGELO PO Spa 110...
Page 115: ...Copyright by Servizio Clienti ANGELO PO Spa 115...
Page 126: ...Copyright by Servizio Clienti ANGELO PO Spa 126 6 4 Operation of the washing system components...
Page 127: ...Copyright by Servizio Clienti ANGELO PO Spa 127 ALARM LOGIC E34...
Page 149: ...Copyright by Servizio Clienti ANGELO PO Spa 149 AT 122 oven...
Page 150: ...Copyright by Servizio Clienti ANGELO PO Spa 150 AT 201 202 ovens...
Page 160: ...Copyright by Servizio Clienti ANGELO PO Spa 160 photo 3 photo 4...
Page 175: ...Copyright by Servizio Clienti ANGELO PO Spa 175...
Page 184: ...Copyright by Servizio Clienti ANGELO PO Spa 184...